Sand casting, a traditional manufacturing process, has also witnessed advancements and innovations over time, leading to improved quality, efficiency, and expanded applications in various industries. Let’s explore some of the notable advancements and applications of sand casting in industry.
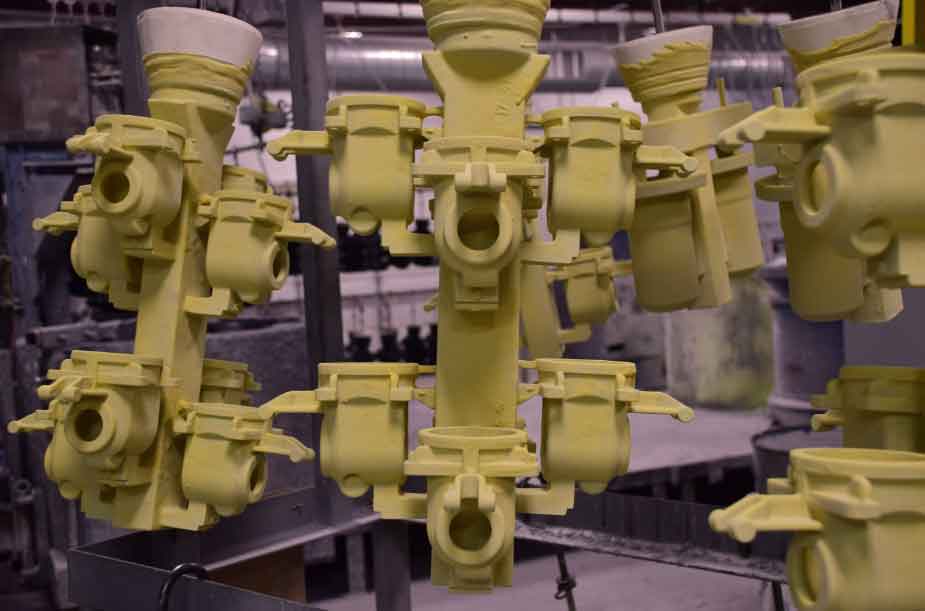
Advanced Simulation and Modeling
Computer-aided design (CAD) and simulation tools have revolutionized the sand casting process. Advanced software allows for the virtual design and analysis of casting processes, optimizing parameters such as mold filling, solidification, and cooling. This helps identify potential defects, optimize gating systems, and predict casting quality before physical production begins. Simulation techniques have greatly improved the efficiency and success rate of sand casting, reducing costly trial-and-error iterations.
Additive Manufacturing and Sand Casting
The integration of additive manufacturing, commonly known as 3D printing, with sand casting has opened up new possibilities for design freedom and customization. 3D printing allows for the creation of complex and intricate sand molds directly from digital models, eliminating the need for traditional pattern-making and reducing lead times. This combination of additive manufacturing and sand casting enables the production of highly customized, one-off parts or small production runs with reduced costs and shorter lead times.
Improved Sand and Binder Systems
Advancements in sand and binder systems have enhanced the quality and efficiency of sand casting. Specialized sands with improved thermal stability, dimensional accuracy, and surface finish are available, allowing for better mold quality and reduced defects. Advanced binder systems provide better control over the curing process, resulting in improved mold strength, reduced gas emissions, and better collapsibility of the mold after casting. These developments contribute to higher-quality castings and increased process efficiency.
Advanced Materials and Alloys
Sand casting has expanded its reach into new industries through the use of advanced materials and alloys. With advancements in metallurgy, sand casting can now handle exotic alloys, high-performance materials, and specialized compositions. This enables the production of parts with superior mechanical properties, corrosion resistance, and high-temperature capabilities. The ability of sand casting to accommodate a wide range of materials makes it a suitable choice for industries such as aerospace, automotive, energy, and defense.
Large-Scale Sand Casting
Sand casting has also seen innovations in handling larger and heavier castings. Advanced molding techniques, such as pit molding and machine molding, have enabled the production of large-scale castings used in industries like marine, construction, and power generation. These techniques provide precise control over the molding process, ensuring dimensional accuracy and reducing the risk of defects in oversized castings.
Sustainable Sand Casting
Sustainability has become a key focus in manufacturing, and sand casting has made progress in this area. The development of environmentally friendly binder systems and the recycling of sand have reduced the environmental impact of sand casting. The use of organic or water-based binders and the implementation of sand reclamation processes help minimize waste generation and reduce the consumption of natural resources.
Conclusion
The advancements in sand casting, including advanced simulation tools, the integration of additive manufacturing, improved sand and binder systems, the use of advanced materials, and large-scale capabilities, have expanded the applications and improved the efficiency of the process. Sand casting continues to be a cost-effective and versatile manufacturing method, catering to a wide range of industries and producing high-quality metal parts with complex geometries. The ongoing innovations in sand casting ensure its relevance and adaptability in the ever-evolving landscape of modern manufacturing.