Ductile iron casting has been a reliable and widely used manufacturing method for decades, but ongoing innovations in the field are continuously advancing the manufacturing techniques associated with this process. These innovations aim to improve efficiency, enhance quality, and expand the capabilities of ductile iron casting. This article explores some of the recent innovations in ductile iron casting that are advancing manufacturing techniques.
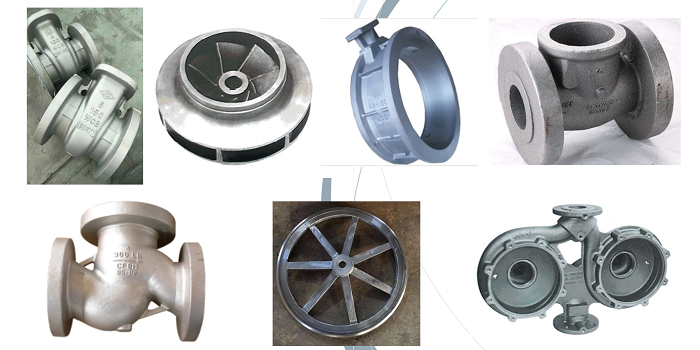
- Advanced Simulation and Modeling: Computer-aided simulation and modeling tools have revolutionized the design and optimization of ductile iron casting processes. Advanced software allows engineers to simulate and visualize the entire casting process, predicting potential defects, optimizing gating and riser designs, and analyzing solidification patterns. This enables more precise control over the casting process, reducing trial and error and enhancing overall casting quality.
- Improved Molding and Core Making: Innovations in molding and core making have contributed to better quality and efficiency in ductile iron casting. Automated molding systems and high-precision molding machines ensure consistent mold quality and dimensional accuracy. Core-making processes have also been enhanced, with improved core materials and technologies that enable complex core designs and better dimensional control.
- Enhanced Melting and Pouring Techniques: Melting and pouring techniques play a crucial role in ductile iron casting. Innovations in this area focus on improving energy efficiency, reducing metal loss, and ensuring consistent metal quality. Induction melting systems, advanced pouring systems, and precise temperature control devices have been developed to optimize the melting and pouring stages, resulting in better castings with reduced defects.
- Optimized Riser and Feeding Systems: Riser and feeding systems are essential for ensuring proper feeding of molten metal and minimizing the risk of shrinkage defects. Innovations in this area include the use of exothermic sleeves, insulated feeding systems, and engineered riser designs that enhance the feeding efficiency and minimize the need for extensive post-casting machining. These advancements contribute to improved casting integrity and reduced material waste.
- Process Monitoring and Control: Real-time process monitoring and control systems have been developed to enhance quality control in ductile iron casting. Sensors and data acquisition systems are used to monitor crucial parameters such as temperature, pressure, and solidification behavior. This data is analyzed and fed back to the process control system, allowing for adjustments and interventions to ensure consistent quality throughout the casting production.
- Automation and Robotics: Automation and robotics have made significant strides in ductile iron casting, enabling increased productivity and precision. Automated pouring systems, robotic handling and finishing operations, and robotic inspection systems have streamlined the manufacturing process, reducing labor requirements and improving overall efficiency. Robotics also offer enhanced safety by performing tasks in hazardous environments.
- Material and Process Innovations: Innovations in materials and processes have expanded the capabilities of ductile iron casting. The development of new alloy compositions, heat treatment techniques, and surface treatments has led to improved mechanical properties, enhanced corrosion resistance, and increased wear resistance of ductile iron castings. These advancements have opened up new opportunities for ductile iron casting in demanding applications.
In conclusion, innovations in ductile iron casting are continuously advancing manufacturing techniques, leading to improved efficiency, quality, and capabilities. Through the use of advanced simulation tools, improved molding and core making techniques, enhanced melting and pouring methods, optimized riser and feeding systems, process monitoring and control systems, automation and robotics, and material and process innovations, the ductile iron casting process continues to evolve and meet the evolving demands of various industries. These innovations enable manufacturers to achieve higher productivity, better quality control, and expanded applications for ductile iron castings.