Despite its long history, gray cast iron technology has seen significant advancements in recent years, further enhancing the material’s properties and expanding its applications. Some notable innovations in gray cast iron technology include:
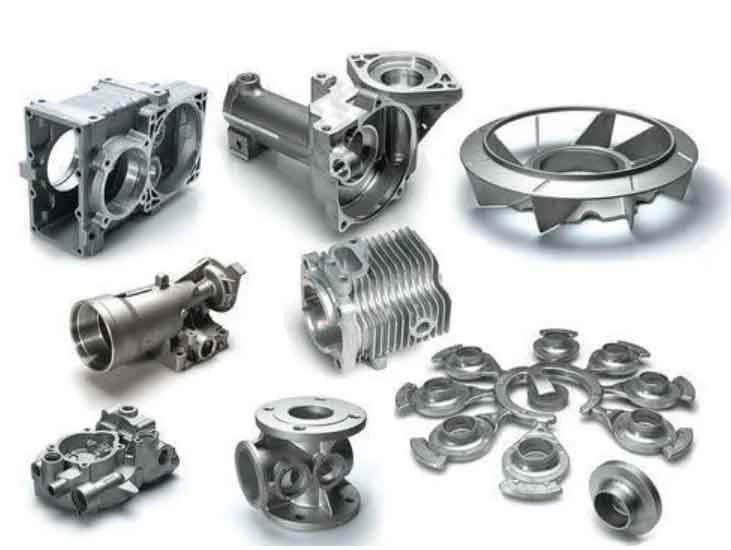
- Alloying and Microstructure Control: Advances in metallurgy have enabled the development of new alloying elements and improved microstructure control in gray cast iron. This has resulted in enhanced strength, wear resistance, and overall performance of gray cast iron components.
- Heat Treatment Techniques: New heat treatment techniques, such as austempering, have been applied to gray cast iron to optimize its microstructure and mechanical properties. Austempered gray cast iron exhibits improved toughness, strength, and ductility compared to conventionally treated cast iron.
- Thin-Wall Casting: Innovations in molding and casting techniques have allowed for the production of thin-wall gray cast iron components with complex geometries. This has expanded the applications of gray cast iron into industries where weight reduction and space optimization are critical.
- Enhanced Damping Properties: Researchers have been working on tailoring the microstructure of gray cast iron to further enhance its damping capacity. This has led to the development of gray cast iron grades that offer improved vibration and noise damping, making them suitable for more precise engineering applications.
- 3D Printing (Additive Manufacturing): 3D printing technologies have been explored for casting gray iron, allowing for the production of custom, intricate components with reduced material waste. This has opened up new possibilities for creating complex designs that were previously challenging to achieve through traditional casting methods.
- Simulation and Modeling: Advanced computer simulations and modeling techniques have been employed to optimize the casting process, predict microstructure formation, and identify potential defects. This has resulted in improved casting quality and reduced manufacturing time and costs.
- Surface Coatings and Treatments: Various surface coatings and treatments, such as thermal spray coatings and laser surface modification, have been applied to gray cast iron to enhance its wear resistance and corrosion resistance in demanding environments.
- Recycling and Sustainability: The focus on sustainability and environmental impact has led to advancements in recycling technologies for gray cast iron, enabling better utilization of scrap and reducing the overall environmental footprint of the material.
- Improved Quality Control: Automation and advanced inspection techniques have been implemented to ensure consistent and high-quality gray cast iron products, reducing the occurrence of defects and enhancing overall reliability.
- Integration with Composite Materials: Research has explored the integration of gray cast iron with other materials, such as polymers and composites, to create hybrid components with optimized properties and performance.
These innovations, along with ongoing research and development, continue to position gray cast iron as a valuable and relevant material in modern engineering. As industries demand improved performance, efficiency, and sustainability, gray cast iron remains a key player in meeting these challenges with its unique set of properties and adaptability to technological advancements.