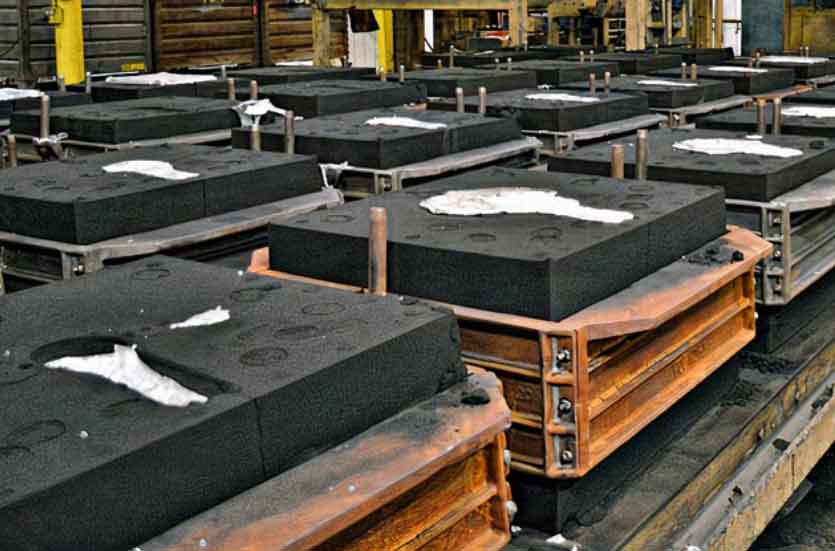
Resin sand casting indeed enables foundries to push the boundaries of traditional casting methods, allowing for innovative designs and intricate details in metal components. The use of resin-bonded sand as the molding material brings several advantages that enable the production of complex and high-quality castings. Here are some ways resin sand casting helps push the boundaries in metal component manufacturing:
1. Complex Geometries:
- Resin sand casting excels in creating intricate and complex geometries that are challenging to achieve with other casting methods. The mold material’s ability to capture fine details and maintain dimensional accuracy enables the production of intricate components with unique shapes and designs.
2. Thin-Walled Castings:
- Resin sand casting is capable of producing thin-walled castings with consistent thickness. This capability is especially valuable in applications where lightweight components are desired without compromising on structural integrity.
3. Fine Surface Finish:
- The use of resin-bonded sand results in superior surface finish compared to traditional green sand casting. This enables the production of castings that require minimal post-casting finishing, saving time and resources.
4. Customization and Prototyping:
- Resin sand casting offers flexibility and cost-effectiveness in producing small batch sizes and prototypes. This allows for quick iteration and customization during the design and development phase, facilitating product improvements and innovation.
5. Rapid Tooling and Short Lead Times:
- The use of 3D-printed patterns in resin sand casting enables rapid tooling and reduced lead times for new component designs. This agility in tooling allows foundries to respond quickly to customer demands and market trends.
6. Part Consolidation:
- Resin sand casting enables the creation of complex castings that integrate multiple components into a single piece. This part consolidation reduces assembly time, minimizes potential weak points in the component, and optimizes overall performance.
7. Internal Cavities and Cores:
- Resin sand casting allows for the creation of intricate internal cavities and complex cores, enabling the production of hollow or semi-hollow components that are structurally sound and have unique functionalities.
8. Design Freedom:
- Resin sand casting provides designers with greater freedom to explore innovative shapes and configurations that were previously challenging or impossible with other casting methods.
9. Increased Material Options:
- Resin sand casting accommodates a wide range of materials, including various metals and alloys, expanding the possibilities for component design and performance.
By leveraging the benefits of resin sand casting, foundries can achieve a higher level of creativity, versatility, and precision in their castings. This process is particularly well-suited for applications where design innovation, intricate details, and complex geometries are essential requirements. As the demand for advanced and customized metal components grows, resin sand casting continues to play a crucial role in pushing the boundaries of what is possible in modern metal casting.