In recent years, innovations in grey cast iron casting techniques have focused on improving precision and performance, enabling manufacturers to produce high-quality components with enhanced properties. Some of the key advancements in grey cast iron casting include:
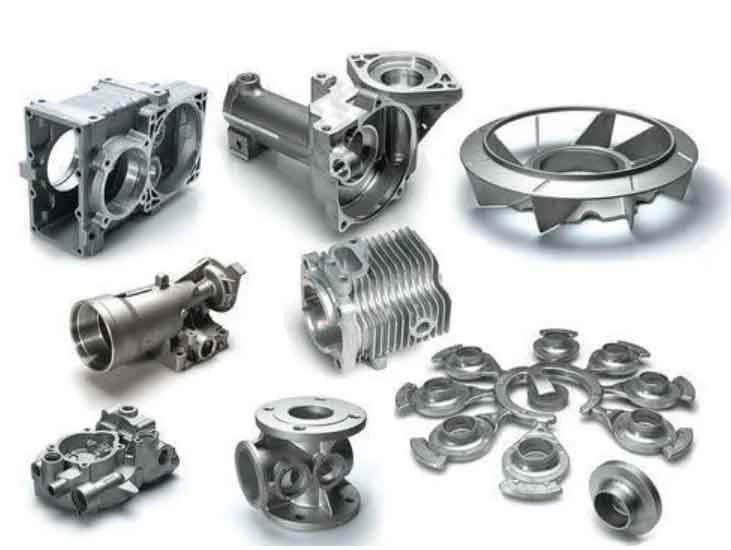
- Computer-Aided Design and Simulation: The use of computer-aided design (CAD) software and simulation tools has revolutionized the casting process. Engineers can now create complex 3D models of the casting, simulate the filling and solidification stages, and predict potential defects. This helps in optimizing the casting process and improving the final product’s quality.
- Additive Manufacturing (3D Printing): Additive manufacturing, commonly known as 3D printing, has found applications in the casting industry. Using 3D printing to create sand molds or patterns allows for intricate designs and reduces lead time. It also enables the production of prototypes and small batch sizes with improved precision.
- Improved Sand Mixtures: Innovations in sand mixing techniques and the development of advanced binders have led to better sand molds and cores. These advancements result in higher dimensional accuracy and smoother surfaces of the castings.
- Mold Coatings: The application of specialized mold coatings has improved the surface finish of grey cast iron castings. These coatings reduce surface defects and improve the release properties, leading to better surface quality and reduced post-casting machining.
- Rapid Solidification Techniques: By controlling the cooling rate during solidification, rapid solidification techniques have been developed to refine the microstructure of grey cast iron. This process produces a finer graphite structure, leading to improved mechanical properties, such as higher tensile strength and enhanced wear resistance.
- Inoculation and Alloying: Controlled inoculation and alloying with elements like nickel, chromium, and molybdenum have been employed to modify the microstructure of grey cast iron. This results in tailored mechanical properties and improved performance in specific applications.
- Automated Casting Processes: Automation and robotics have been integrated into various stages of the casting process, such as mold handling, pouring, and cleaning. This enhances process consistency, reduces human errors, and increases overall productivity.
- Real-Time Monitoring and Control: Advanced sensors and real-time monitoring systems are now utilized to collect data during the casting process. This data helps operators monitor critical parameters, make adjustments, and maintain consistent casting quality.
- Environmentally Friendly Practices: The casting industry is increasingly adopting sustainable and environmentally friendly practices. Recycling sand, optimizing energy consumption, and reducing waste generation are some of the initiatives that align with global environmental concerns.
- Digital Twins and Predictive Maintenance: Digital twins, virtual representations of physical casting processes, are used for optimization and predictive maintenance. These tools allow for real-time analysis of casting conditions and the identification of potential issues before they occur.
These innovations in grey cast iron casting techniques have significantly enhanced the precision and performance of cast components. They have also contributed to the overall sustainability and efficiency of the casting process, making grey cast iron a versatile material for a wide range of applications in industries such as automotive, construction, machinery, and more.