Lost foam casting is continuously evolving as advancements in materials, equipment, and process control push the boundaries of metal casting technology. Some of the key innovations in lost foam casting include:
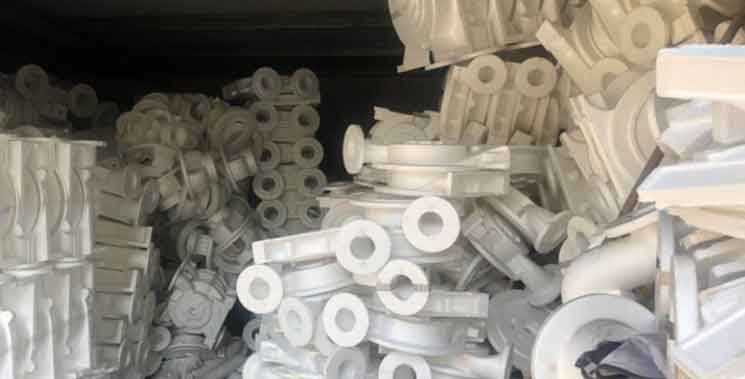
- Advanced Foam Materials: Manufacturers are developing new foam materials with improved thermal properties and dimensional stability, allowing for the production of larger and more complex foam patterns.
- 3D Printing of Foam Patterns: Additive manufacturing technologies, such as 3D printing, are being integrated into lost foam casting to create intricate and customized foam patterns directly from CAD models, reducing lead times and increasing design flexibility.
- Computer Simulation and Process Optimization: Advanced computer simulation tools are being used to model and optimize the lost foam casting process, allowing for better prediction of defects and improved process control to achieve higher quality castings.
- Robotics and Automation: Robotics and automation are being incorporated into the lost foam casting process to handle foam patterns, improve consistency, and enhance production efficiency.
- Innovative Refractory Coatings: New refractory coatings with improved properties, such as better resistance to thermal cracking and increased refractoriness, are being developed to enhance mold quality and casting surface finish.
- Improved Pouring Techniques: Innovative pouring techniques, such as vacuum-assisted or pressure-assisted casting, are being employed to achieve better metal filling and reduce the risk of defects.
- In-Situ Foam Pattern Testing: Real-time monitoring and testing of foam patterns during the casting process are being explored to detect defects early and ensure the quality of the final casting.
- Green Sand Molding for Lost Foam Casting: Combining green sand molding with lost foam casting allows for the reuse of sand, reducing environmental impact and lowering costs.
- Alternative Binder Systems: Researchers are exploring alternative binder systems for the foam patterns, such as bio-based or water-soluble binders, to make the lost foam casting process even more environmentally friendly.
- Alloy Development: Innovations in alloy development, including advanced alloys with superior mechanical properties, are expanding the range of applications for lost foam castings.
These innovations, along with ongoing research and development, are transforming lost foam casting from a specialized niche process to a mainstream manufacturing technique capable of producing complex, high-quality metal components for various industries. As lost foam casting gains wider acceptance and integration with other advanced manufacturing technologies, its role in the metal casting industry is set to continue growing in the future.