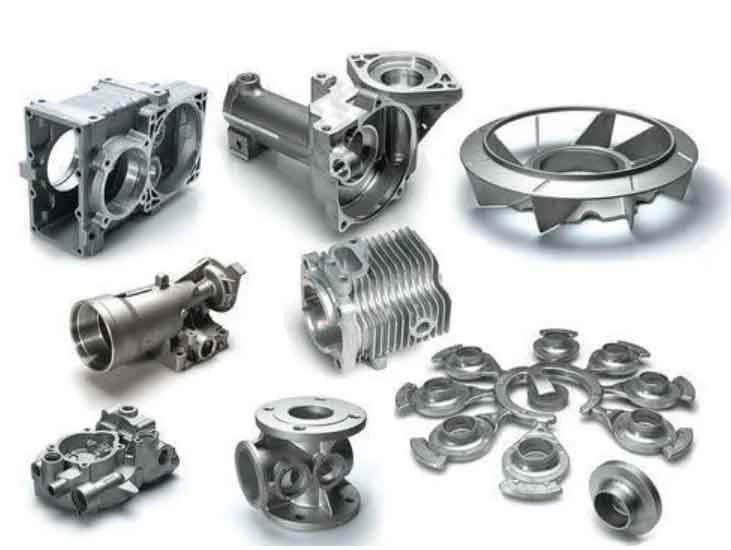
In recent years, there have been several innovations in resin sand casting technology aimed at enhancing efficiency and precision in the foundry industry. These advancements leverage new materials, process automation, and digital technologies to improve the overall casting process. Here are some notable innovations in resin sand casting:
1. 3D Printing for Pattern and Core Production:
- Additive manufacturing, or 3D printing, is increasingly used to produce complex patterns and cores directly from digital designs. This eliminates the need for traditional pattern-making techniques, reduces lead times, and allows for rapid prototyping.
2. Digital Simulation and Modeling:
- Advanced computer simulation and modeling software are used to optimize mold filling, solidification, and cooling processes. These simulations help predict potential defects and optimize mold designs for improved casting quality.
3. Robotics and Automation:
- Automation of various foundry processes, such as sand handling, core assembly, and mold handling, improves process efficiency and reduces labor requirements. Robots can handle repetitive tasks, allowing human operators to focus on more complex and value-added activities.
4. Real-Time Monitoring and Control:
- Sensors and data analytics are employed to monitor key process parameters in real-time. This data is then used to make informed decisions and adjustments to optimize casting quality and reduce scrap rates.
5. Advanced Resin Binders and Sand Additives:
- New resin binders and additives have been developed to enhance the properties of the sand molds, such as improving strength, reducing gas-related defects, and achieving higher-quality surface finishes.
6. Inorganic Core Technology:
- Inorganic core technology, such as sodium silicate-based cores, offers improved core strength and dimensional stability, especially in high-temperature casting applications.
7. Vacuum Sealing and Degassing:
- Vacuum sealing and degassing techniques help remove trapped air and gas from the sand molds, reducing the risk of defects like porosity and improving casting quality.
8. Binder Jetting for Sand Molds:
- Binder jetting technology, which involves selectively depositing a binder on a layer of sand, is explored for sand mold production, offering potential cost savings and design flexibility.
9. Eco-Friendly Resins and Binders:
- Foundries are exploring eco-friendly resin and binder options to reduce environmental impact and promote sustainability.
These innovations in resin sand casting technology contribute to increased efficiency, reduced production costs, and improved casting precision. By adopting these advancements, foundries can enhance their competitiveness and produce high-quality castings for a wide range of industries, from automotive and aerospace to machinery and beyond.