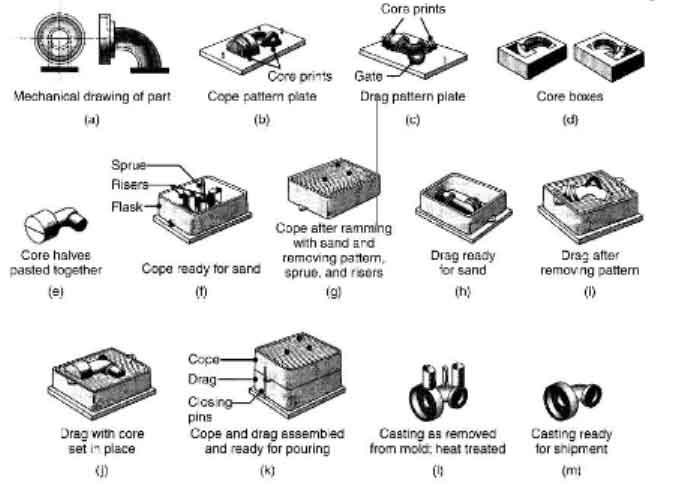
Over the years, sand casting has evolved significantly with innovations that have pushed the boundaries of design and complexity. Some of the key innovations in sand casting include:
- Advanced Mold Materials: The development of advanced mold materials, such as high-temperature-resistant ceramics and refractory coatings, has improved mold life, dimensional accuracy, and surface finish. These materials can withstand higher pouring temperatures and reduce defects in castings.
- Computer-Aided Design (CAD) and Simulation: The integration of CAD software and simulation tools has revolutionized sand casting. Engineers can now design intricate and complex parts virtually, simulate the casting process, identify potential defects, and optimize the design and process parameters before physical production. This reduces trial and error and shortens development cycles.
- 3D Printing for Patterns: Additive manufacturing, specifically 3D printing, has gained traction in sand casting. 3D printed patterns provide greater design freedom, allowing for the creation of complex geometries that were previously challenging to achieve with traditional patterns.
- Rapid Prototyping: The combination of 3D printing with sand casting enables rapid prototyping of designs, reducing lead times for product development. This approach allows for quick iterations and design validation before committing to expensive tooling.
- Automated Casting Equipment: Automation and robotics have been integrated into sand casting processes, enhancing consistency and reducing labor-intensive tasks. Automated pouring systems, mold handling, and part removal increase efficiency and reduce the risk of human errors.
- Improved Sand Mixtures: Advances in sand mixtures, binder systems, and additives have resulted in better sand properties, such as higher strength, reduced gas defects, and improved collapsibility, leading to better casting quality.
- Vacuum Casting: Vacuum-assisted sand casting helps reduce gas porosity and other defects by drawing vacuum on the mold during pouring. This ensures a denser casting with improved mechanical properties.
- Metal Additives: The addition of various alloys and elements to the base metal can enhance the properties of the casting, such as increasing strength, wear resistance, or corrosion resistance.
- Advanced Casting Simulation Software: Casting simulation software has become more sophisticated, providing comprehensive insights into the casting process, solidification behavior, thermal analysis, and stress prediction. These simulations aid in optimizing gating systems and preventing defects.
- Sustainable Practices: Environmental concerns have prompted innovations in sand casting to reduce waste, energy consumption, and emissions. Recycling sand and using more sustainable binders are examples of such initiatives.
These innovations have enabled sand casting to compete with other advanced casting methods, such as investment casting and die casting, for complex and high-precision parts. Sand casting continues to be a reliable and cost-effective method for a wide range of applications, and its ongoing advancements contribute to the continued growth and evolution of the manufacturing industry.