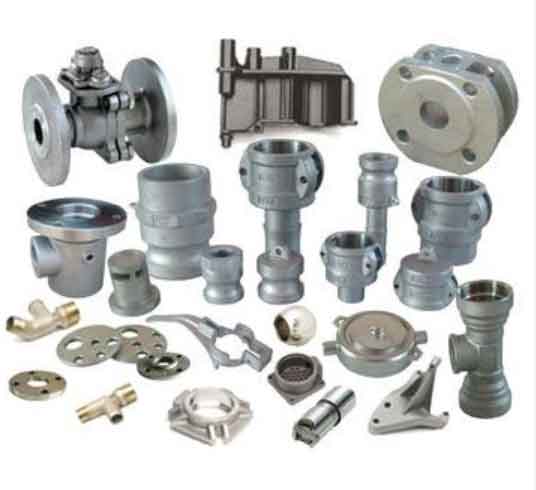
In recent years, there have been several innovations in sand casting technology aimed at enhancing efficiency and quality in the casting process. These innovations leverage advancements in materials, equipment, and process control to achieve improved results. Here are some notable innovations in sand casting technology:
- Digitalization and simulation: Digitalization technologies, such as computer-aided design (CAD) and computer-aided engineering (CAE), are widely used to design and simulate casting processes. Advanced software programs allow for virtual testing and optimization of mold designs, gating systems, and process parameters before physical production. This helps to identify and address potential issues early on, reducing time and costs associated with trial-and-error methods.
- 3D printing of sand molds and cores: Additive manufacturing, or 3D printing, has gained traction in sand casting. It enables the production of complex molds and cores with intricate geometries that would be challenging or impossible to achieve using traditional methods. 3D printed sand molds and cores provide greater design flexibility, reduce lead times, and allow for more efficient use of material.
- Automated mold and core making: Automation has been introduced in mold and core making processes to improve efficiency and consistency. Automated systems for sand preparation, mold assembly, and core production help streamline the process, reduce labor requirements, and enhance quality control. These systems can provide precise sand mixing, uniform compaction, and accurate mold assembly, resulting in better mold quality and dimensional accuracy.
- Real-time process monitoring and control: Advanced sensing technologies and data analytics are being used to monitor and control key process parameters in real time. Sensors placed within the mold or on the casting equipment can collect data on variables such as temperature, pressure, and vibration. This data is then analyzed to detect deviations and optimize process conditions, leading to improved casting quality and reduced scrap rates.
- Improved sand and binder formulations: Researchers have developed new sand and binder formulations that offer better flowability, compaction, and thermal stability. These improved formulations result in higher-quality molds with enhanced surface finish and dimensional accuracy. Additionally, eco-friendly binders with reduced emissions and improved recyclability are being developed to address environmental concerns.
- Robotics and automation in handling and finishing: Robotics and automation play a significant role in handling and finishing castings. Automated systems can efficiently handle the pouring, shakeout, and cleaning processes, reducing manual labor and ensuring consistent results. Robotic systems equipped with advanced sensors and algorithms can perform precise grinding, polishing, and inspection tasks, improving the overall quality of the finished castings.
- Advanced non-destructive testing (NDT) techniques: Non-destructive testing methods, such as X-ray, ultrasonic testing, and 3D scanning, have evolved to provide more accurate and efficient defect detection and characterization. These advanced NDT techniques enable thorough inspection of castings, ensuring that any defects or abnormalities are identified and addressed promptly.
These innovations in sand casting technology contribute to higher efficiency, improved casting quality, and reduced costs in the manufacturing process. By leveraging these advancements, manufacturers can achieve enhanced productivity, greater design flexibility, and increased competitiveness in the market.