As the casting industry evolves, new innovations and technological advancements have been introduced to mitigate common casting defects like porosity, shrinkage, and inclusions. This article discusses some of these innovative approaches in minimizing casting defects.
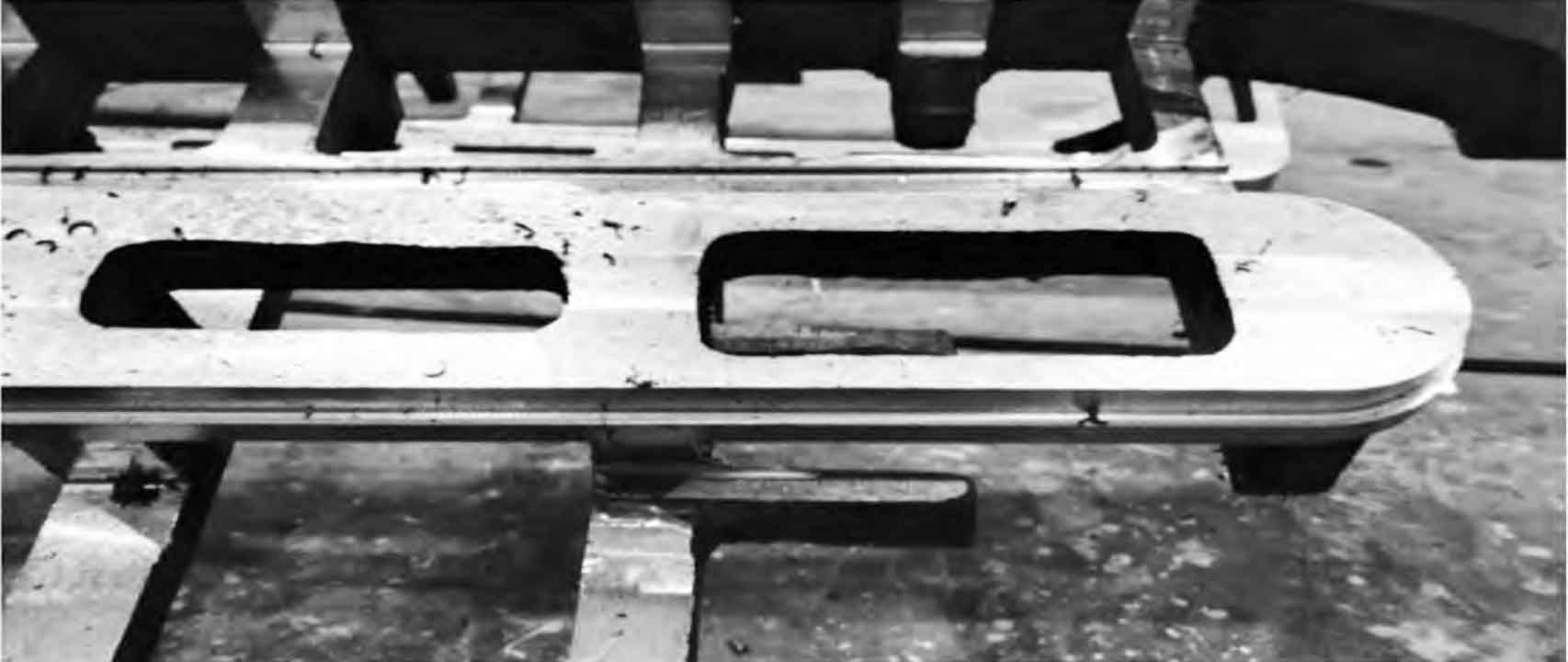
- Advanced Simulation Software: Simulation software offers a virtual way to evaluate casting designs and processes before they are physically implemented. Advanced simulation can predict potential defects related to solidification, cooling, and mold filling. This allows engineers to modify designs or processes to mitigate potential problems before the actual casting process.
- 3D Printing of Molds: 3D printing allows for the creation of precise, complex mold geometries that can help mitigate defects. By using additive manufacturing to create molds, intricate venting systems and cooling channels can be integrated, reducing the risk of gas porosity and shrinkage.
- Automated Pouring and Process Control: Automation in the casting process reduces human error and provides consistent and controlled pouring conditions, which can significantly reduce defects. Advanced process control systems can monitor and adjust process parameters in real time, improving quality and consistency.
- In-line Quality Inspection Technologies: Technologies such as computed tomography (CT) scanning and real-time X-ray imaging allow for non-destructive inspection of casting quality during the manufacturing process. These techniques can detect internal and surface defects, enabling immediate correction and reducing the number of defective castings.
- Advanced Metallurgical Control: Advanced metallurgical techniques allow for precise control over the alloy composition and casting conditions to reduce defects. This includes the use of degassing techniques, fluxes, and filtration systems to reduce gas and inclusion defects.
- Machine Learning and Artificial Intelligence: AI and machine learning algorithms can analyze vast amounts of data from the casting process to predict defects and suggest corrective actions. These technologies are paving the way for predictive maintenance and process optimization in the casting industry.
Innovations in technology and process control are providing foundries with more tools than ever to mitigate common casting defects. As the industry continues to embrace these advancements, the ability to reduce defects, increase productivity, and improve casting quality will only continue to grow. By investing in these innovative solutions, foundries can significantly enhance their casting processes and produce high-quality, defect-free products.