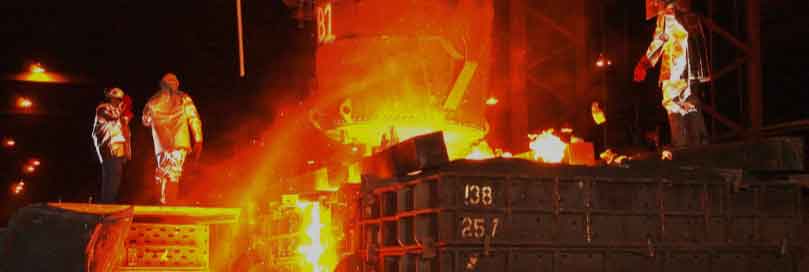
White cast iron and ductile iron, also known as nodular cast iron, are two distinct types of cast iron with different microstructures and properties. Let’s compare white cast iron and ductile iron in terms of their microstructure, mechanical properties, and applications:
White Cast Iron:
- Microstructure: White cast iron has a microstructure consisting of cementite (iron carbide) and pearlite. It lacks graphite, giving it a white appearance.
- Mechanical Properties: White cast iron is very hard and brittle, offering high hardness and excellent wear resistance. However, it has low toughness, ductility, and impact resistance.
- Applications: White cast iron is primarily used in applications that require exceptional wear resistance, such as mining equipment, grinding balls, and wear-resistant parts subjected to abrasive wear.
Ductile Iron (Nodular Cast Iron):
- Microstructure: Ductile iron has a microstructure characterized by spherical graphite nodules dispersed in a matrix of ferrite, pearlite, and small amounts of other phases. The presence of graphite nodules provides ductility and impact resistance.
- Mechanical Properties: Ductile iron exhibits higher tensile strength, elongation, and impact resistance compared to white cast iron. It offers improved toughness and can withstand higher loads and impacts.
- Applications: Ductile iron is widely used in applications that require both strength and ductility, such as automotive components, pipes, gears, and heavy machinery parts.
In summary, white cast iron and ductile iron have distinct microstructures and mechanical properties that make them suitable for different applications. White cast iron provides exceptional wear resistance but lacks ductility and impact resistance. Ductile iron, on the other hand, offers a combination of strength, ductility, and impact resistance, making it suitable for applications that require both toughness and load-bearing capacity. The selection between white cast iron and ductile iron depends on the specific requirements of the application, considering factors such as wear resistance, strength, toughness, and the ability to withstand impacts or loads.
White Cast Iron
White cast iron is characterized by its hard and brittle structure, primarily due to the presence of carbides in its composition. This type of cast iron does not contain graphite flakes but rather carbides, which make it hard.
- Strength: White cast iron has a high compressive strength and excellent wear resistance, making it suitable for applications involving abrasive wear.
- Hardness: It’s significantly hard due to the carbides, with a Brinell hardness value of approximately 600 MPa.
- Brittleness: However, this hardness comes at the cost of brittleness, making it unsuitable for applications requiring impact resistance or ductility.
- Thermal Conductivity: White cast iron has lower thermal conductivity compared to ductile iron, with values ranging between 15 – 30 W/(m.K).
Ductile (Nodular) Cast Iron
Ductile iron, on the other hand, is known for its excellent ductility and toughness, which are achieved by adding nodulizing agents to the iron, causing the carbon to form into spherical nodules rather than flakes or carbides. This modification provides it with mechanical properties that are similar to steel.
- Mechanical Properties: Ductile iron has superior tensile strength (up to 900 Mpa) and elongation (up to 18%), with a Brinell hardness of approximately 150 – 180 MPa.
- Impact and Fatigue Resistance: It has good impact resistance, even at low temperatures, and exhibits excellent fatigue resistance.
- Versatility and Cost: While ductile iron can be slightly more expensive to produce than grey cast iron due to the addition of nodulizing agents, it remains cost-effective, especially when compared to malleable and austenitic irons. Its production technology is mature, with many foundries capable of producing high-quality ductile iron.
- Applications: Due to its properties, ductile iron is used in demanding applications where a combination of strength, wear resistance, and ductility is required, such as in automotive components, pipes, and machinery parts.
Key Differences and Selection Criteria
- Tensile Strength and Ductility: Ductile iron outperforms white cast iron in both tensile strength and ductility, making it more suitable for applications requiring resistance to shock and stress.
- Wear Resistance: White cast iron offers superior wear resistance but lacks the ductility and toughness provided by ductile iron.
- Cost and Production Complexity: Ductile iron has a higher production cost than white cast iron but offers better mechanical properties and versatility.
- Application Specificity: The choice between white and ductile iron depends on the specific requirements of the application. White cast iron is preferred for wear-resistant surfaces where brittleness is not a major concern, whereas ductile iron is chosen for parts requiring toughness and ductility.
In conclusion, both white and ductile cast irons have their unique advantages and are selected based on the specific needs of the application. Understanding their distinct properties helps in making an informed choice to match the engineering requirements