The control of the composite interface focuses on two aspects: one is to ensure the flatness of the composite interface, and the other is to avoid poor bonding caused by the cold iron water and decomposition products in front of the flow. The simulation of the mold filling process of high chromium cast iron using the lost foam casting module of the simulation software is shown in Figure 1.
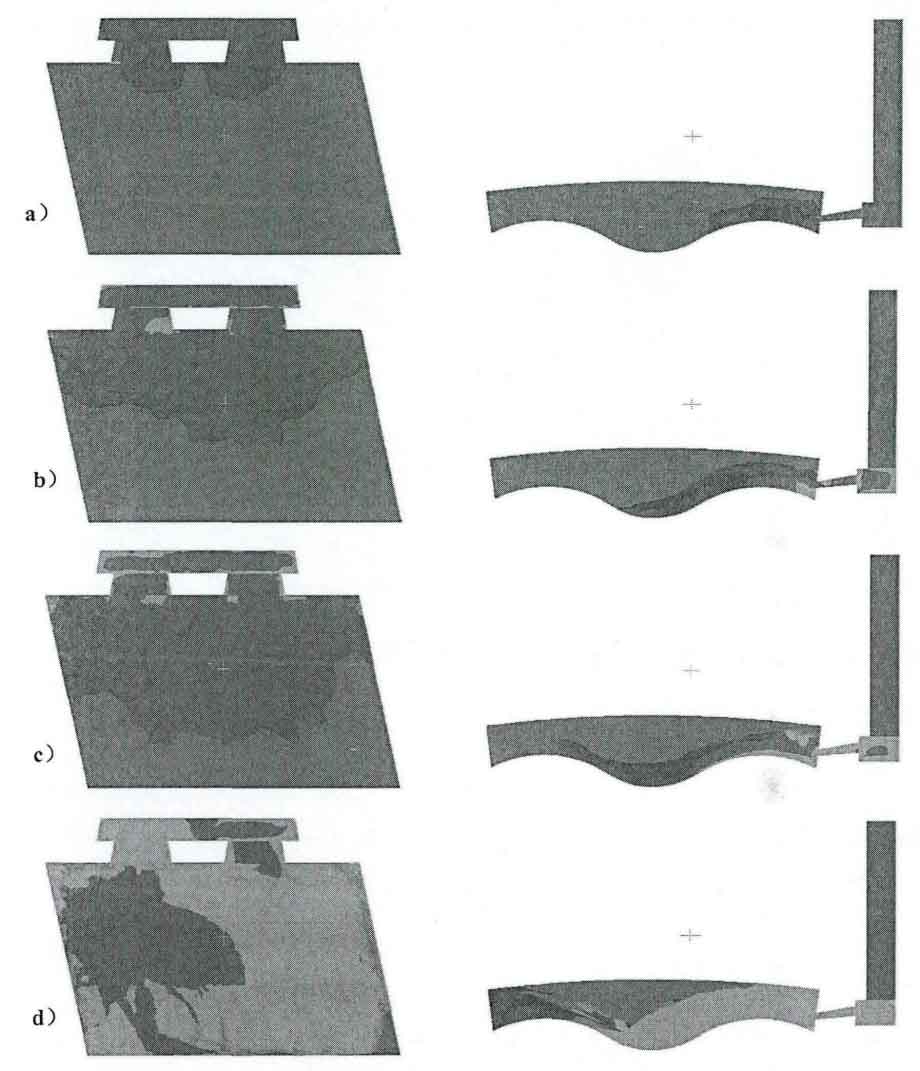
From the side view of Figure 1, it can be observed that molten iron can evenly fill the space belonging to the high chromium cast iron layer at the bottom of the casting lining plate, but the molten iron will occupy the space belonging to the carbon steel layer at the last moment of filling. However, it can be inferred that when the pouring of molten iron is stopped for 12.5s, the molten iron that previously occupied the space of the carbon steel layer will fall due to its own weight and fill the hollow space in the middle of the high chromium cast iron layer, So as to form a relatively flat bonding interface; From the top view, it can be observed that the last filling area of molten iron is at the far end angle of the casting lining plate, so the overflow riser should be set at the far end angle, and the overflow riser should be overlapped with the carbon steel horizontal bypass. With the help of the carbon steel vertical bypass, the overhead riser should be formed to facilitate the smooth discharge of decomposition gas. The complete riser winding process system is shown in Figure 2.
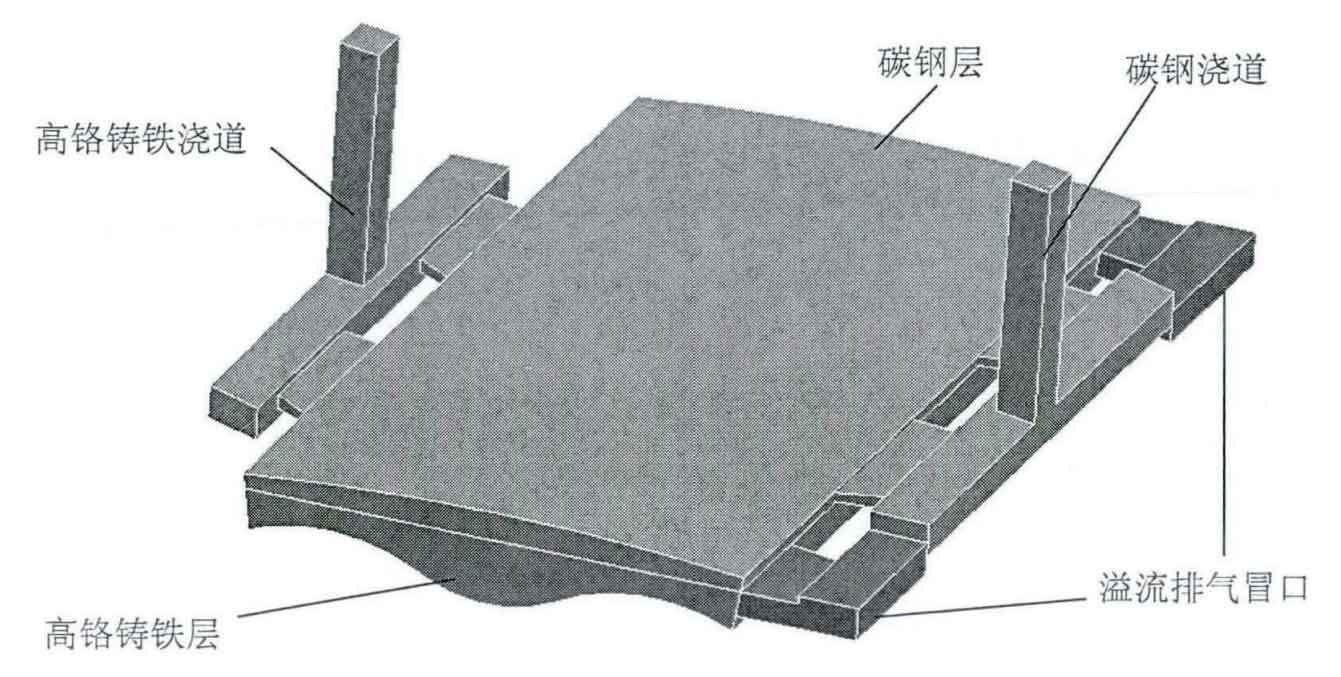