Sand casting is a widely used metal casting process that involves the creation of a mold from a mixture of sand and a binding agent. This process is known for its versatility, cost-effectiveness, and ability to produce complex shapes. Here is a comprehensive guide to the sand casting process:
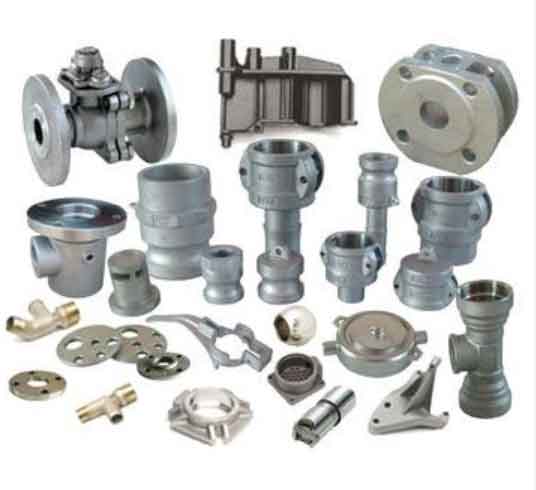
- Pattern Creation: The first step in sand casting is the creation of a pattern, which is a replica of the desired part. Patterns can be made from various materials such as wood, plastic, or metal. The pattern is typically slightly larger than the final part to account for the shrinkage that occurs during the solidification of the metal.
- Mold Preparation: A mold is created by placing the pattern in a box called a flask. The flask is divided into two halves: the upper half is called the cope, and the lower half is called the drag. The pattern is positioned in the drag, and the cope is placed on top. The two halves of the mold are securely clamped together.
- Molding Material: Sand mixed with a binder, such as clay, is packed around the pattern inside the flask. This mixture is known as molding sand. The sand should have good flowability and compactability to ensure a well-formed mold. The pattern is carefully removed, leaving a cavity in the sand mold that represents the shape of the desired part.
- Core Placement: If the part requires internal features or cavities, cores made of sand or other materials are placed inside the mold before closing it. Cores provide the negative space needed to create internal features in the final casting.
- Mold Assembly: Once the sand is packed and any necessary cores are placed, the cope and drag are joined together, forming a complete mold. Channels called sprues, runners, and gates are included in the mold to allow for the flow of molten metal and the removal of gases.
- Melting and Pouring: The mold is prepared for the pouring of molten metal. The metal is typically melted in a furnace and brought to the desired temperature. The molten metal is then poured into the mold through the sprue, allowing it to flow through the runners and gates and fill the cavity.
- Solidification and Cooling: After the mold is filled, the molten metal begins to solidify within the cavity. The cooling time depends on the size and complexity of the casting as well as the type of metal used. Proper cooling ensures the formation of a solid and well-defined casting.
- Mold Breakout: Once the casting has solidified and cooled, the mold is broken apart to reveal the metal casting. This is usually done by vibrating or mechanically separating the mold. The casting is then cleaned to remove any residual sand or mold materials.
- Finishing Operations: The casting may undergo additional processes to remove any excess material, smooth rough surfaces, and achieve the desired shape and dimensions. These processes can include grinding, machining, heat treatment, and surface finishing.
- Inspection and Quality Control: The final casting is inspected for any defects or irregularities. Non-destructive testing methods such as visual inspection, X-ray examination, or ultrasonic testing may be employed to ensure the quality of the casting.
Sand casting offers numerous advantages, including the ability to produce large and complex parts, cost-effectiveness, and versatility in material selection. It is widely used in various industries such as automotive, aerospace, construction, and more. The process requires skill and expertise to ensure proper mold preparation, molten metal handling, and quality control to achieve high-quality castings.