Investment casting, also known as lost wax casting, is a metal casting process that involves the creation of a wax pattern, investment of the pattern in a ceramic shell, and the subsequent casting of molten metal into the shell to create the final part. Let’s explore the step-by-step process of investment casting:
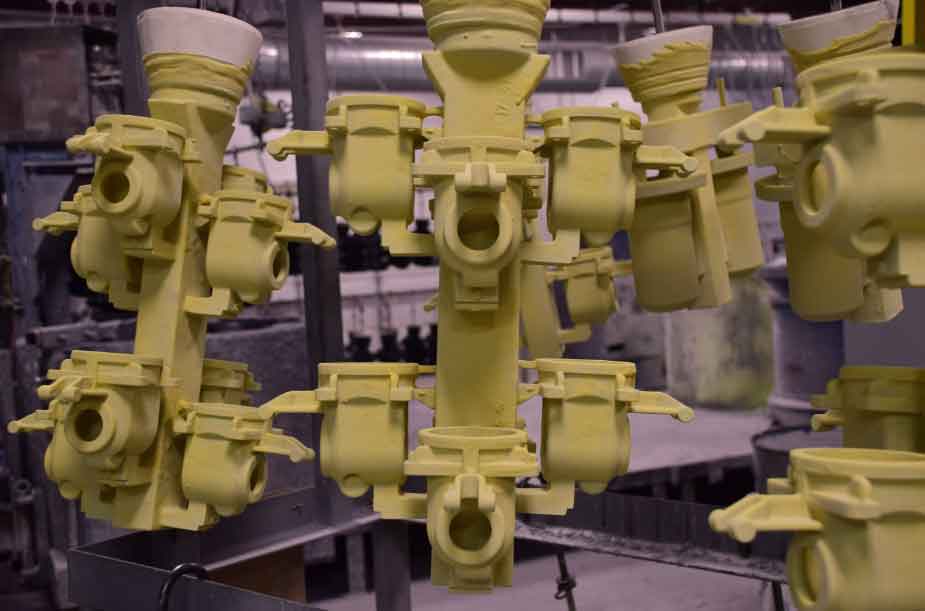
- Pattern Creation: The investment casting process begins with the creation of a pattern, typically made from wax or a similar material. The pattern is an exact replica of the desired final part. It can be produced using various methods, including injection molding, machining, or hand sculpting. The pattern must account for any necessary allowances for shrinkage and surface finish.
- Pattern Assembly: Once the patterns are created, they are attached to a gating system, which includes channels and gates to allow the molten metal to flow into the mold cavity and any required vents to allow the escape of gases during the casting process. The pattern assembly, together with the gating system, is called the “tree” or “cluster.”
- Investment: The pattern assembly is then invested in a ceramic shell. The shell is formed by repeatedly dipping the pattern assembly into a ceramic slurry and coating it with a refractory material, such as silica or zircon. This process is typically done multiple times to build up a thick and durable shell.
- Dewaxing: After the ceramic shell is built, the next step is to remove the wax from the shell. This can be done through several methods, including autoclaving, steam dewaxing, or flashfire. The removal of the wax creates a cavity in the shell that will be filled with molten metal during casting.
- Preheating: Once the wax is removed, the ceramic shell is preheated to a specific temperature to remove any remaining moisture and ensure it is ready to withstand the high temperatures of the molten metal.
- Casting: The preheated ceramic shell is placed in a casting flask and filled with molten metal. The metal is typically poured into the mold through the gating system, allowing it to fill the cavity created by the wax pattern.
- Solidification and Cooling: Once the molten metal is poured, it solidifies within the ceramic shell, taking the shape of the wax pattern. The casting is left to cool and solidify completely.
- Shell Removal and Finishing: After the casting has cooled, the ceramic shell is broken away or dissolved, revealing the solid metal part. The part may undergo further finishing operations, such as removal of excess material, machining, grinding, polishing, and surface treatment, to achieve the desired final shape, dimensions, and surface finish.
- Inspection and Quality Control: The finished part is thoroughly inspected to ensure it meets the required specifications and quality standards. This may include dimensional checks, visual inspection, non-destructive testing, and mechanical testing.
- Finishing and Assembly: If necessary, the cast part may undergo additional finishing processes, such as heat treatment or coating, to enhance its mechanical properties or protect it from corrosion. In some cases, multiple castings may need to be assembled or welded together to create the final product.
The investment casting process combines artistry and precision to create intricate and high-quality metal parts. It offers the advantage of producing complex shapes with excellent surface finish and dimensional accuracy. Investment casting is widely used in industries such as aerospace, automotive, medical, and jewelry, where the ability to create intricate and customized components is essential.