Lost foam casting is indeed a revolutionary casting technique that harnesses the full potential of the process for various applications. This advanced method offers several key advantages that make it stand out in the world of casting. Here’s a closer look at how lost foam casting revolutionizes the industry:
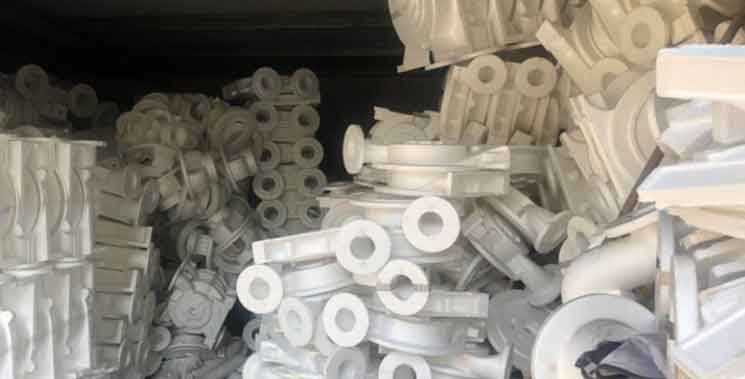
- Complex Geometry and Intricacy:
- Lost foam casting enables the production of complex and intricate geometries with exceptional precision.
- The foam patterns used in the process can be easily shaped, assembled, and manipulated to create highly intricate and detailed parts.
- This capability opens up new possibilities for the manufacturing of components with intricate features, undercuts, and thin walls that would be challenging to produce using traditional casting methods.
- Design Freedom and Versatility:
- Lost foam casting offers unparalleled design freedom and versatility, allowing for creative and innovative part designs.
- The flexibility of foam patterns allows for the exploration of unconventional shapes and optimized designs without the limitations of traditional tooling constraints.
- Designers and engineers can push the boundaries of what is achievable, leading to groundbreaking and innovative products.
- Near-Net Shape Casting:
- Lost foam casting excels in producing near-net shape castings, minimizing the need for extensive post-casting machining or finishing operations.
- The foam patterns accurately replicate the final part geometry, resulting in minimal material waste and reduced machining requirements.
- This leads to significant time and cost savings, improved production efficiency, and faster time-to-market for manufacturers.
- Enhanced Production Efficiency:
- Lost foam casting offers notable production efficiency gains compared to traditional casting methods.
- The process eliminates the need for core-making, core removal, and complex mold assembly, reducing labor-intensive operations.
- The streamlined process leads to shorter lead times, increased productivity, and improved overall production efficiency.
- Cost-Effectiveness:
- Lost foam casting provides cost advantages for manufacturers, particularly in terms of tooling and material savings.
- The elimination of expensive permanent molds or complex sand molds reduces tooling costs.
- The near-net shape capability minimizes material waste, resulting in cost savings in material consumption and machining operations.
- Additionally, the reduced need for post-casting machining operations translates to lower labor and equipment costs.
- Excellent Dimensional Accuracy:
- Lost foam casting achieves high dimensional accuracy and repeatability, ensuring precise reproduction of intricate features.
- The foam patterns accurately represent the final part geometry, minimizing dimensional variations and ensuring consistent and accurate castings.
- This dimensional accuracy eliminates the need for extensive post-casting machining or rework, saving time and resources.
- Material Versatility:
- Lost foam casting is compatible with a wide range of metals and alloys, offering versatility in material selection.
- Manufacturers can cast various metals, including aluminum, iron, steel, and non-ferrous alloys, to meet specific application requirements.
- This flexibility enables the production of components for diverse industries and applications.
- Environmental Sustainability:
- Lost foam casting promotes environmental sustainability through reduced material waste and energy consumption.
- The foam patterns used in the process are easily recyclable or disposable, minimizing environmental impact.
- The absence of sand molds and binders reduces the generation of harmful emissions or byproducts.
Lost foam casting is a truly revolutionary casting technique that harnesses the full potential of the process, providing advantages in complex geometry production, design freedom, near-net shape casting, production efficiency, cost-effectiveness, dimensional accuracy, material versatility, and environmental sustainability. With its transformative capabilities, lost foam casting is reshaping the manufacturing industry and driving innovation in a wide range of applications.