Investment casting, also known as lost-wax casting, is a casting method that combines traditional craftsmanship with modern manufacturing techniques. It has been practiced for centuries and has evolved over time to incorporate technological advancements, making it a versatile and precise casting process. Here’s how investment casting combines the best of traditional craftsmanship and modern manufacturing:
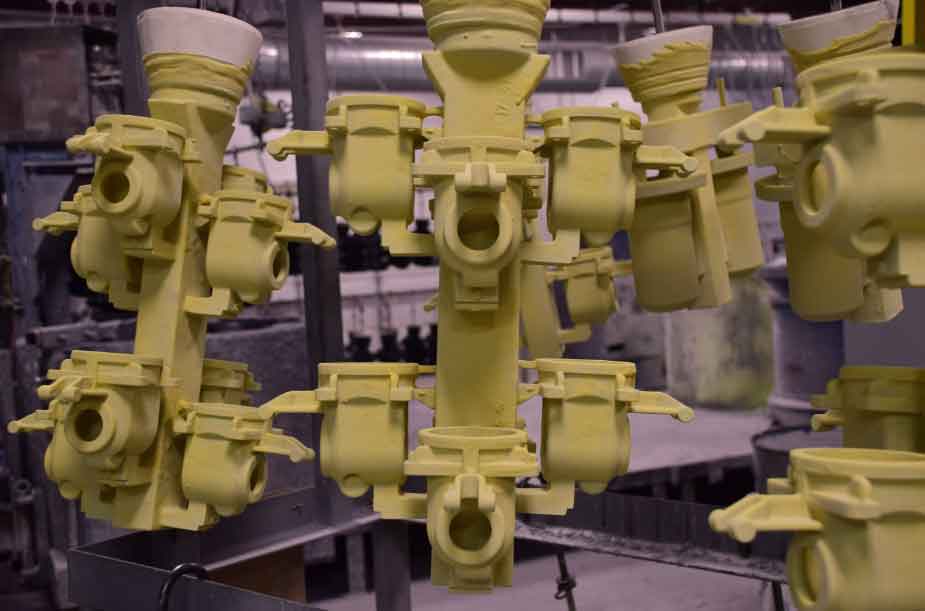
- Pattern Creation: The investment casting process begins with the creation of a pattern, which can be made using traditional methods such as hand carving or by using modern techniques like 3D printing or CNC machining. Traditional craftsmanship allows for intricate details and artistic designs to be captured in the pattern, while modern techniques offer precision and efficiency in pattern production.
- Mold Making: Once the pattern is created, it is used to produce a mold, or investment, which is typically made of ceramic material. Traditional craftsmanship is applied in the meticulous process of creating the mold, ensuring that the pattern is accurately replicated. Modern manufacturing techniques such as computer-aided design (CAD) and computer-aided manufacturing (CAM) help streamline the mold-making process, ensuring accuracy and consistency.
- Wax Pattern Assembly: In investment casting, wax patterns are created by injecting molten wax into the mold. These wax patterns are then assembled onto a gating system, which includes channels and gates to facilitate the flow of molten metal during casting. Traditional craftsmanship is applied in the careful assembly and positioning of the wax patterns, ensuring proper alignment and minimizing any potential defects.
- Shell Building: The assembled wax patterns are coated with a ceramic slurry and then covered with a refractory material to create a shell. This shell provides the mold cavity for the final casting. Traditional craftsmanship is employed in the application of the ceramic slurry and the careful building of layers to create a strong and precise shell. Modern techniques such as automated dipping and robotic coating systems enhance the efficiency and consistency of the shell building process.
- Melting and Casting: Once the shell is complete, it undergoes a dewaxing process where the wax inside the shell is melted out, leaving behind a hollow cavity. The shell is then heated to a high temperature to prepare it for casting. Molten metal is poured into the preheated shell, filling the cavity and taking the shape of the desired part. Modern technology such as induction furnaces and precise temperature control systems ensure accurate and controlled melting and casting processes.
- Finishing and Inspection: After the casting solidifies, the shell is removed, and the casting is cleaned and finished. Traditional craftsmanship comes into play during the finishing process, where skilled artisans remove any imperfections, smooth rough edges, and achieve the desired surface finish. Modern inspection techniques, such as non-destructive testing and dimensional measurement tools, ensure the quality and integrity of the final castings.
By combining traditional craftsmanship with modern manufacturing techniques, investment casting offers the best of both worlds. It allows for the creation of intricate and complex parts with excellent dimensional accuracy and surface finish, while benefiting from the efficiency, precision, and quality control offered by modern technology. This synergy between traditional and modern approaches makes investment casting a versatile and reliable process for a wide range of applications in various industries.