Lost foam casting defects can occur due to various reasons, including process parameters, material characteristics, and mold quality. Understanding the root causes of these defects is essential to implement effective countermeasures. Here are some common lost foam casting defects, their possible causes, and suggested countermeasures:
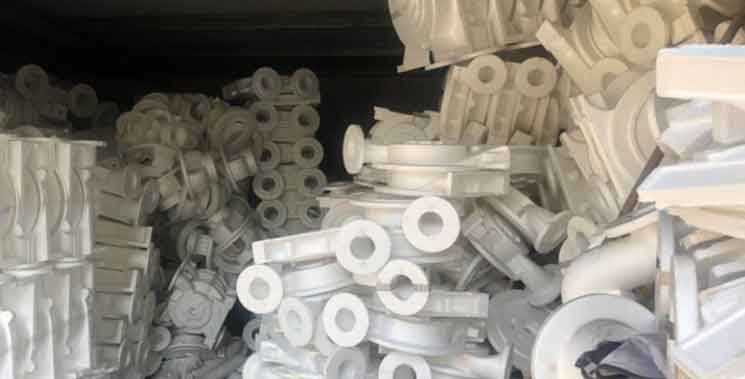
- Incomplete Filling or Misrun:
- Cause: Insufficient pouring temperature or pouring rate, improper gating design, inadequate venting.
- Countermeasures: Increase pouring temperature or rate, optimize gating system design, ensure proper venting, and use effective mold coatings.
- Shrinkage and Porosity:
- Cause: Insufficient feeding, improper riser design, inadequate mold venting, high metal temperature.
- Countermeasures: Optimize riser design for proper feeding, ensure adequate mold venting, control metal temperature, use feeding aids like insulating sleeves or exothermic materials.
- Blowholes or Gas Porosity:
- Cause: Entrapped air or gas in the mold, inadequate mold venting, excessive moisture in the mold, improper pouring technique.
- Countermeasures: Improve mold venting, ensure proper drying of the mold, use proper pouring technique to minimize turbulence, implement effective degassing techniques.
- Distortion or Warping:
- Cause: Thermal expansion mismatch, inadequate cooling or solidification control, improper gating or riser placement.
- Countermeasures: Optimize cooling and solidification control, consider dimensional compensations in pattern design, ensure proper gating and riser placement.
- Surface Defects (Cracks, Sand Sticking):
- Cause: Improper mold release, thermal stress, inadequate coating, improper shakeout process.
- Countermeasures: Improve mold release agent application, control cooling rates to reduce thermal stress, apply proper mold coating, ensure effective shakeout process.
- Dimensional Inaccuracies:
- Cause: Pattern distortion, mold expansion or contraction, inadequate gating or venting.
- Countermeasures: Ensure proper pattern construction and handling, control mold expansion or contraction, optimize gating and venting design.
- Sand Inclusion or Mold Erosion:
- Cause: Poor mold compaction, inadequate mold coating, erosion due to metal turbulence.
- Countermeasures: Optimize mold compaction and density, apply appropriate mold coatings, improve gating and pouring design to minimize turbulence.
- Metal Runouts:
- Cause: Improper gating or pouring technique, inadequate mold venting.
- Countermeasures: Optimize gating and pouring technique, improve mold venting, use proper venting components like vents or filters.
It’s important to note that the specific causes of defects may vary depending on the casting design, materials, and process parameters. Therefore, a thorough analysis of the specific defect and process conditions is essential to determine the most appropriate countermeasures. Regular monitoring, process optimization, and continuous improvement efforts will help in reducing defects and improving the quality of lost foam castings.