Investment casting, also known as lost wax casting, offers several advantages that enhance efficiency and cost-effectiveness in metal production. The process has undergone advancements and optimization over the years, resulting in improved productivity, reduced waste, and enhanced overall economic benefits. In this response, we will explore how investment casting achieves efficiency and cost-effectiveness in metal production.
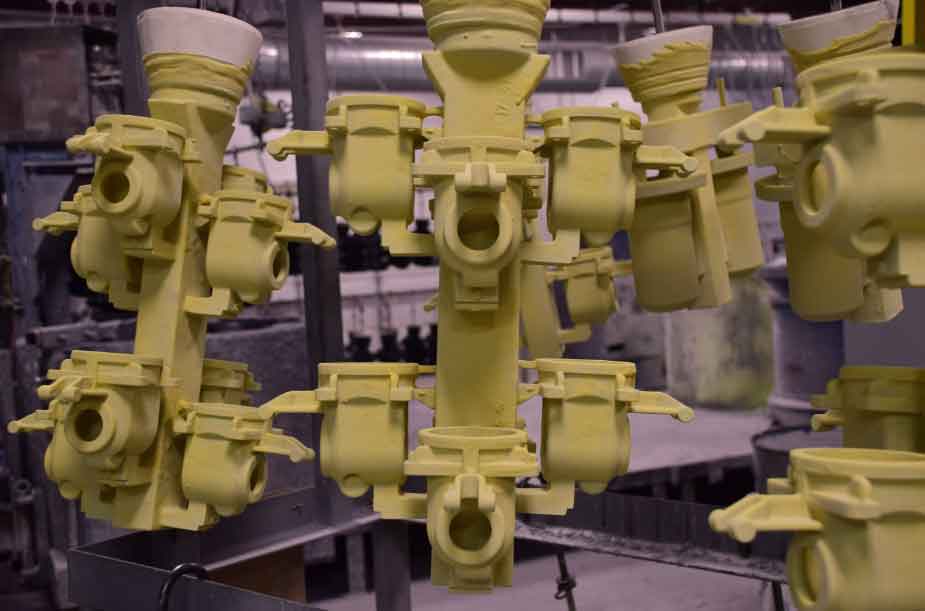
- Near-Net Shape Manufacturing: Investment casting is known for its ability to produce near-net shape components. This means that the casting process can create parts that require minimal additional machining or finishing operations. By closely matching the final shape and dimensions of the desired component, investment casting reduces material waste and machining costs associated with traditional subtractive manufacturing methods. The near-net shape capability significantly improves efficiency and reduces production time and costs.
- Complex Geometries and Intricate Details: Investment casting enables the production of complex geometries and intricate details that would be difficult or impractical to achieve through other manufacturing methods. The process captures fine features, thin walls, undercuts, and internal cavities with high precision. This eliminates the need for multiple assembly steps or joining processes, reducing labor costs and potential points of failure. The ability to produce complex components as a single, integrated piece enhances efficiency and cost-effectiveness in metal production.
- Material Efficiency: Investment casting optimizes material usage by minimizing waste. The process allows for the precise allocation of materials, reducing excess material in the final component. The near-net shape manufacturing capability further contributes to material efficiency by minimizing the need for material removal during post-casting operations. This reduction in material waste leads to cost savings and a more sustainable manufacturing process.
- Design Flexibility and Lightweighting: Investment casting offers design flexibility, enabling engineers to optimize component designs for weight reduction without compromising structural integrity. By strategically removing excess material, such as thick sections or unnecessary reinforcements, investment casting helps achieve lightweight designs. Lightweight components result in various benefits, including improved fuel efficiency, reduced transportation costs, and enhanced performance. The ability to produce complex, lightweight parts through investment casting adds to the overall cost-effectiveness of the process.
- Economies of Scale and Batch Production: Investment casting is well-suited for batch production and economies of scale. Multiple components can be cast simultaneously using a single mold, reducing setup time and cost per part. As the number of parts increases, the cost per unit decreases, making investment casting a cost-effective choice for large production runs. This scalability allows manufacturers to leverage the benefits of investment casting for various applications, from small, intricate components to large, complex structures.
- Process Automation and Control: Automation plays a significant role in enhancing efficiency and cost-effectiveness in investment casting. Automated systems can handle various tasks, such as wax pattern production, shell formation, and shell removal, with precision and consistency. This reduces labor costs, improves process control, and increases production throughput. Automation also enables faster production cycles, shorter lead times, and better resource utilization, resulting in overall cost savings.
- Reduced Tooling Costs: Investment casting typically requires less expensive tooling compared to other manufacturing methods, such as die casting or machining. Tooling for investment casting can be made from materials like silicone, epoxy, or even 3D-printed patterns, which are more cost-effective than producing complex molds or dies. The lower tooling costs make investment casting an attractive option for small to medium production runs, prototypes, and custom components.
Investment casting offers several features and advantages that enhance efficiency and cost-effectiveness in metal production. Its near-net shape manufacturing, ability to produce complex geometries, material efficiency, design flexibility, scalability, automation, and reduced tooling costs contribute to optimized production processes, reduced waste, and improved economic benefits. Investment casting continues to be a competitive and viable manufacturing method in various industries, offering cost-effective solutions for the production of high-quality metal components.