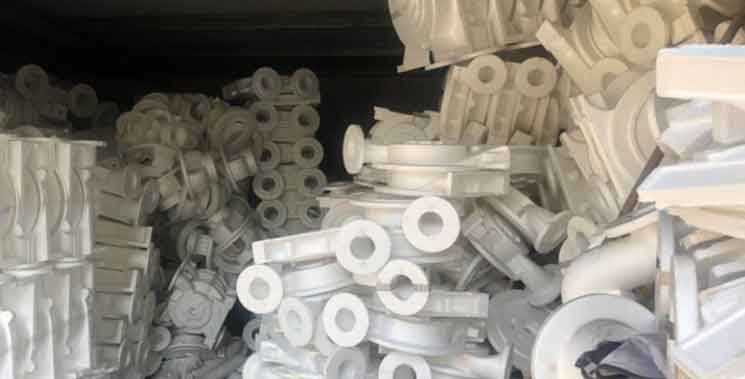
Lost foam casting has indeed been pushing the boundaries of design and functionality in the realm of metal component production. This casting method offers unique advantages that enable the creation of complex and intricate components that may have been challenging or even impossible to achieve through traditional casting techniques. Here’s how lost foam casting is revolutionizing design and functionality:
1. Design Freedom:
Lost foam casting allows for a high degree of design freedom due to the versatility of foam patterns. Designers can create intricate and complex shapes with undercuts, thin walls, and internal features that would be difficult to achieve using traditional patterns or cores. This opens up new possibilities for innovative and aesthetically appealing designs.
2. Complex Geometry:
Lost foam casting excels in producing components with complex geometry. The foam pattern can be easily shaped and molded to achieve intricate designs that conventional casting methods may struggle to replicate. As a result, engineers and designers can push the boundaries of what’s possible in terms of design complexity and functionality.
3. Lightweighting:
Lost foam casting is particularly advantageous for lightweighting initiatives in various industries. The ability to create thin-walled and intricate components allows for the reduction of material usage, leading to lighter parts without compromising strength and performance. This is especially beneficial in automotive and aerospace applications, where weight reduction can improve fuel efficiency and overall performance.
4. Integration of Features:
Lost foam casting enables the integration of multiple features into a single casting, eliminating the need for separate components and assembly operations. This results in more compact and efficient designs with improved structural integrity and reduced assembly time.
5. Prototype to Production:
Lost foam casting is well-suited for producing both prototypes and production parts. The simplicity of foam pattern production allows for rapid prototyping and design iterations, enabling faster development cycles. Once the design is finalized, lost foam casting can smoothly transition to mass production, providing a seamless and cost-effective manufacturing process.
6. Cost-Effective Complexity:
Lost foam casting offers cost-effective solutions for creating complex components. Traditional manufacturing methods, such as machining or fabricating intricate shapes, can be expensive and time-consuming. Lost foam casting streamlines the process, reducing the need for post-casting machining and assembly, leading to cost savings in both material usage and labor.
7. Functionality Enhancements:
By embracing the design possibilities of lost foam casting, engineers can create components with enhanced functionality. This includes components with optimized fluid flow, improved heat transfer, better vibration damping, and reduced weight, resulting in improved overall performance and efficiency.
8. Customization and Personalization:
Lost foam casting facilitates customization and personalization of components, making it suitable for producing unique and one-of-a-kind parts. Whether for art installations, architectural elements, or specialized industrial applications, lost foam casting allows for individualized solutions tailored to specific needs.
Lost foam casting has been pushing the boundaries of design and functionality, transforming the way complex metal components are manufactured. Its versatility, design freedom, lightweighting capabilities, and integration of features make it a valuable technique across various industries. As technology and materials continue to advance, lost foam casting is likely to play an even more significant role in shaping the future of metal component production.