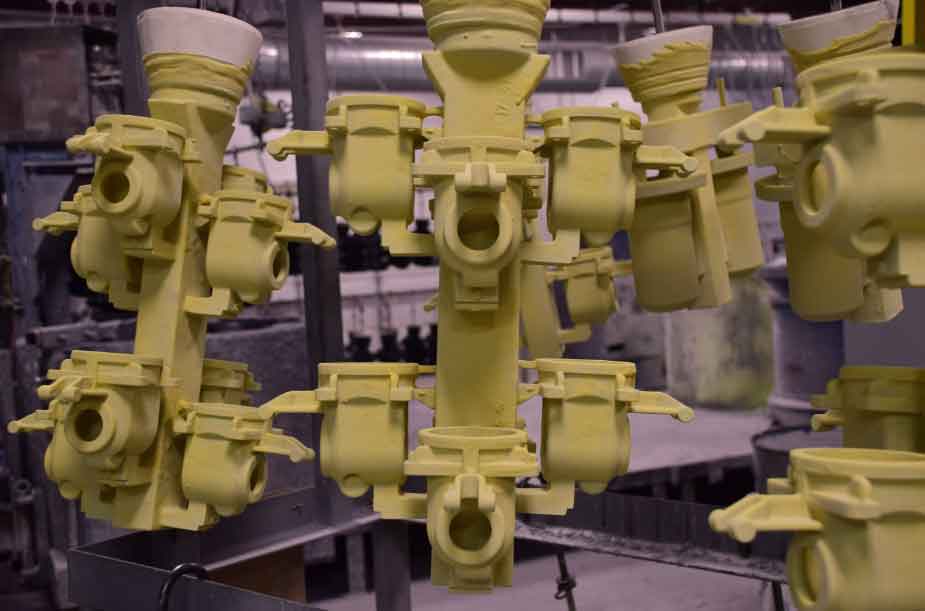
Investment casting, also known as lost-wax casting, plays a vital role in meeting the demands of high-performance applications in the aerospace industry. Here’s how investment casting addresses the specific requirements of aerospace applications:
1. Complex Geometries:
Investment casting allows for the production of complex geometries with intricate features, thin walls, and internal cavities. This capability is crucial in aerospace applications where components need to be lightweight, aerodynamic, and highly efficient.
2. Weight Reduction:
Investment casting enables designers to consolidate multiple parts into a single casting, reducing the overall weight of aerospace components. By eliminating the need for fasteners or joining methods, investment casting helps achieve weight reduction goals, which are critical for improving fuel efficiency and maximizing payload capacity.
3. Heat Resistance:
The aerospace industry often requires components that can withstand high temperatures, such as turbine blades and engine components. Investment casting supports the use of high-temperature alloys, including superalloys, that exhibit excellent heat resistance and mechanical properties, making it suitable for these demanding applications.
4. High Strength-to-Weight Ratio:
Investment casting allows for the production of components with a high strength-to-weight ratio, which is essential in aerospace applications. By utilizing lightweight materials and optimizing the design for strength, investment casting helps achieve the desired balance between structural integrity and weight reduction.
5. Design Flexibility:
Investment casting offers design flexibility, enabling engineers to create intricate shapes, curved surfaces, and aerodynamically optimized components. This flexibility allows for the customization of aerospace components to meet specific performance requirements, ensuring optimal functionality and efficiency.
6. Material Selection:
Investment casting supports a wide range of materials suitable for aerospace applications. This includes stainless steel, titanium, nickel-based superalloys, and other high-performance alloys. The ability to select the most appropriate material based on factors such as strength, corrosion resistance, and temperature resistance is crucial in meeting the demanding requirements of aerospace applications.
7. Precision and Dimensional Accuracy:
Investment casting provides excellent dimensional accuracy and surface finish, meeting the stringent requirements of aerospace components. The high precision and consistency of investment casting ensure proper fit and alignment of complex parts, reducing the need for additional machining or assembly operations.
8. Quality and Reliability:
Investment casting undergoes rigorous quality control measures to ensure the integrity and reliability of aerospace components. Non-destructive testing techniques such as X-ray inspection, ultrasonic testing, and dye penetrant testing are employed to detect any defects or flaws that could compromise the component’s performance and safety.
Investment casting has proven to be an effective manufacturing method in the aerospace industry, delivering complex and high-quality components that meet the industry’s stringent requirements. By enabling the production of lightweight, high-strength, and heat-resistant components with precise dimensions and intricate geometries, investment casting contributes to the advancement of aerospace technology and the achievement of performance goals in this demanding industry.