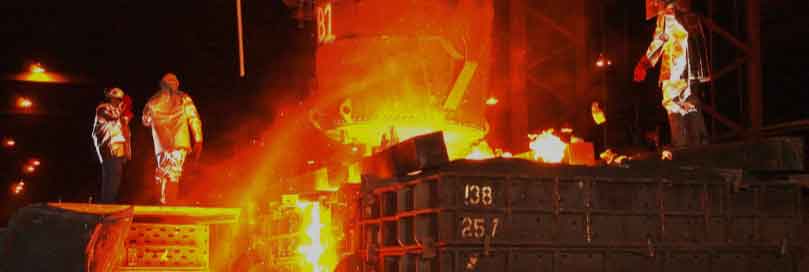
Next-generation foundry technology is revolutionizing the manufacturing landscape by enabling faster, more efficient, and more cost-effective production processes. Foundries are facilities where metal castings are produced by melting and pouring molten metal into molds. Traditionally, foundries have relied on labor-intensive processes and older technologies, but the advent of next-generation foundry technology is changing the game.
One of the key advancements in next-generation foundry technology is the use of digitalization and automation. By incorporating advanced sensors, data analytics, and robotics, foundries can monitor and control the production process with greater precision and efficiency. Real-time data collection and analysis allow for proactive maintenance, optimization of process parameters, and reduced downtime, leading to increased productivity and improved quality control.
Another significant development is the implementation of additive manufacturing, also known as 3D printing, in foundries. Additive manufacturing allows for the production of complex metal parts with intricate geometries that would be challenging or even impossible to achieve using traditional casting methods. This technology enables faster prototyping, customization, and reduced material waste, making it highly advantageous for industries such as aerospace, automotive, and healthcare.
Next-generation foundry technology also focuses on sustainable manufacturing practices. Energy-efficient equipment, recycling and reusing of materials, and the reduction of harmful emissions are all key considerations. Foundries are adopting cleaner and greener technologies, such as electric arc furnaces and induction melting, to minimize their environmental impact.
Furthermore, the integration of advanced simulation tools and modeling techniques plays a crucial role in optimizing the foundry process. Computer simulations can accurately predict the behavior of molten metal during casting, allowing for the optimization of mold design, material flow, and solidification processes. This reduces the need for costly and time-consuming trial-and-error experiments, leading to faster production cycles and improved overall efficiency.
The emergence of the Industrial Internet of Things (IIoT) has also made a significant impact on next-generation foundry technology. By connecting various machines, devices, and systems, foundries can create a networked environment where data is seamlessly exchanged, facilitating better process monitoring, remote control, and predictive maintenance. The IIoT enables the concept of a “smart foundry,” where real-time data and analytics drive intelligent decision-making and process optimization.
In summary, next-generation foundry technology is transforming the manufacturing landscape by leveraging digitalization, automation, additive manufacturing, sustainability, simulation tools, and the Industrial Internet of Things. These advancements enable foundries to enhance productivity, achieve higher precision, reduce waste, improve quality control, and adopt more sustainable practices. As a result, industries that rely on metal castings can benefit from faster, more efficient, and cost-effective production processes, leading to increased competitiveness and innovation.