Chapter 1: Investment Casting Process
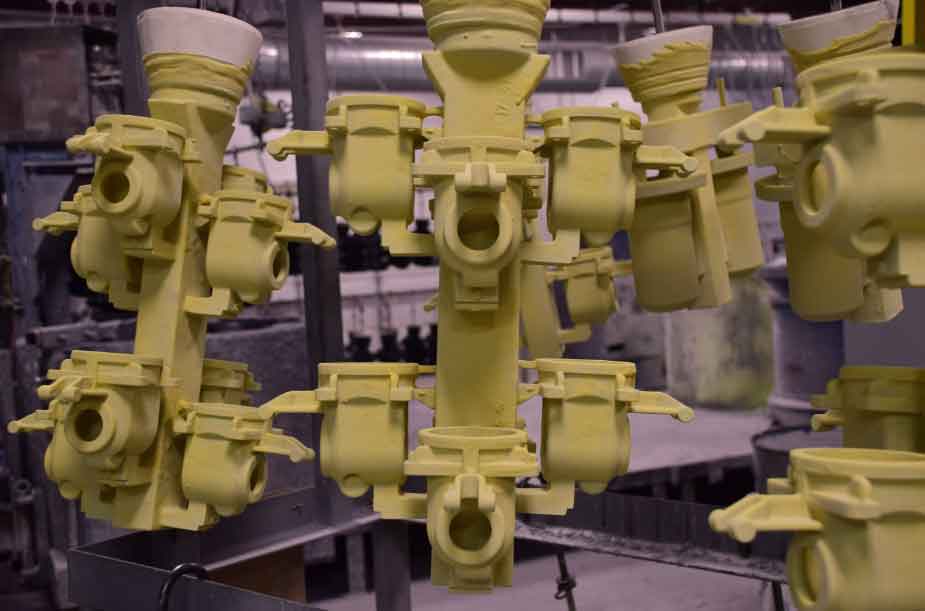
The melting process in investment casting involves melting the chosen alloy, preparing the ceramic shell, and pouring the molten metal into the shell to create the final casting. Here’s an overview of the melting process in investment casting:
1. Alloy Melting:
- The selected casting alloy is melted in a furnace. The furnace type and melting temperature vary based on the specific alloy being used.
- The alloy is heated to its liquid state, ensuring that it is fully molten and homogeneous.
2. Investment Treatment:
- Before pouring the molten metal, the ceramic shell must be prepared to receive the metal. This involves several steps:2.1 Preheating: The ceramic shell mold is preheated in an oven to a temperature that helps prevent thermal shock when the molten metal is poured.2.2 Shell Assembly: Multiple ceramic shells may be assembled together to form a larger mold for batch casting or to create complex shapes.2.3 De-Watering: The preheated shell is dewatered to remove any residual moisture that could lead to steam formation during metal pouring.2.4 Binder Burnout: Any remaining binder materials from the ceramic shell are burned out during the preheating process, preventing defects in the casting.
3. Pouring Process:
- Once the ceramic shell is prepared, the molten alloy is poured into the mold cavity.
- Pouring can be done manually or using automated equipment, depending on the scale and complexity of the casting operation.
4. Solidification:
- As the molten metal fills the mold, it begins to solidify and take the shape of the mold cavity.
- Controlled solidification ensures that the casting retains its desired shape and properties.
5. Cooling and Removal:
- After solidification, the casting is allowed to cool and solidify further in the mold.
- Once cooled, the ceramic shell is broken or removed to reveal the cast metal part.
6. Post-Casting Processes:
- The cast part is cleaned to remove any remaining ceramic shell material or other impurities.
- It may undergo additional processes such as machining, heat treatment, and surface finishing to achieve the desired final specifications.
The melting process in investment casting requires careful coordination of alloy melting, mold preparation, and pouring to ensure that the molten metal flows smoothly into the mold cavity, minimizing defects and achieving the desired casting properties. Proper temperature control, preheating, and shell treatment are crucial to successful investment casting.
Chapter 2: The Basic Concepts of Investment Casting
Investment casting, also known as lost-wax casting, is a precision casting process used to create intricate and complex metal parts with high accuracy and detail. The process involves several steps to create a final product. Here are the basic concepts of investment casting:
Process Overview:
- Pattern Creation: A wax or other material pattern is produced, replicating the shape of the desired final metal part.
- Assembly: The pattern is attached to a gating system, which includes sprues, runners, and gates. This creates a pathway for molten metal to flow into the mold cavity.
- Investment Molding: The pattern assembly is dipped multiple times into a ceramic slurry and coated with a refractory material (investment), forming a ceramic shell around the pattern.
- Dewaxing: The coated assembly is heated to remove the wax or other pattern material, leaving a hollow ceramic mold.
- Preheating: The ceramic shell mold is preheated to prepare it for metal pouring.
- Metal Pouring: Molten metal is poured into the preheated ceramic mold.
- Solidification: The molten metal cools and solidifies inside the ceramic mold, taking the shape of the desired part.
- Shell Removal: Once the metal has solidified, the ceramic shell is broken or removed, revealing the cast metal part.
- Finishing: The cast part is cleaned, finished, and may undergo additional processes such as machining, polishing, or heat treatment to achieve the desired final specifications.
Principles and Working Mechanisms:
- Pattern Replication: The investment casting process is based on the principle of replicating the pattern’s shape precisely in the final metal part. The pattern is created using wax, plastic, or other materials with low melting points. It is designed with allowances for shrinkage and other factors that affect the final part.
- Ceramic Shell Formation: The pattern assembly is coated with multiple layers of ceramic slurry, which hardens into a ceramic shell. This shell provides the mold for the molten metal.
- Wax Removal: Dewaxing involves melting or vaporizing the wax or pattern material from the ceramic shell. This leaves behind a hollow mold cavity.
- Metal Pouring and Solidification: The preheated ceramic mold is filled with molten metal. The metal cools and solidifies within the mold, adopting its shape.
- Precision and Detail: Investment casting is capable of producing parts with intricate details, thin walls, and complex shapes that might be challenging to achieve through other casting methods.
- Dimensional Accuracy: Investment casting offers high dimensional accuracy and tight tolerances, reducing the need for post-casting machining.
- Material Variety: A wide range of metals and alloys can be used in investment casting, including steel, aluminum, bronze, and more.
Investment casting is utilized in industries where precision, complexity, and quality are crucial, such as aerospace, automotive, jewelry, medical equipment, and art. Its ability to produce intricate and high-quality parts makes it a valuable process for creating components that require both functionality and aesthetics.
Chapter 3: The Application of Investment Casting
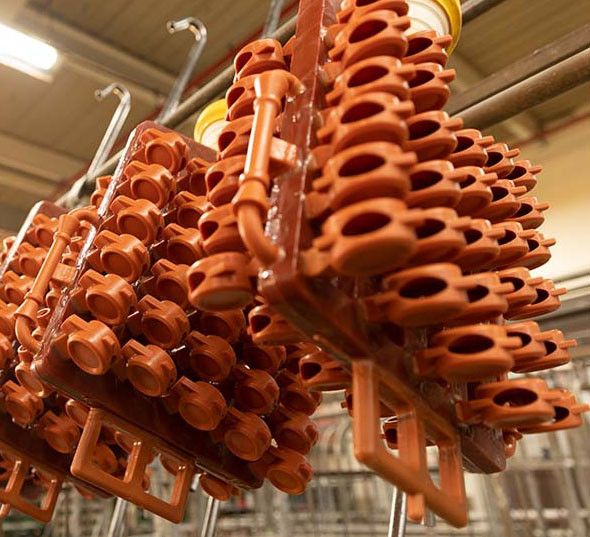
Investment casting, also known as lost-wax casting, is a versatile manufacturing process used across various industries to produce complex and intricate components with high precision and excellent surface finish. Here are some examples of the application of investment casting in different industries:
1. Aerospace Industry:
- Investment casting is widely used in aerospace for manufacturing critical components such as turbine blades, vanes, engine components, and structural parts.
- The process allows for the production of intricate and heat-resistant parts with precise dimensions, contributing to the efficiency and performance of aircraft engines.
2. Automotive Manufacturing:
- Investment casting is employed in the automotive industry to produce engine components, transmission parts, suspension components, and other critical parts.
- It enables lightweighting, improved fuel efficiency, and the creation of complex geometries that may be challenging to achieve through traditional machining methods.
3. Energy and Power Generation:
- Investment casting is utilized in the energy sector for producing turbine blades, vanes, and other components used in gas and steam turbines for power generation.
- The process helps enhance turbine efficiency, reduce maintenance requirements, and increase the overall performance of power plants.
4. Medical and Dental:
- Investment casting is applied in the medical and dental fields to manufacture implants, orthopedic devices, and dental prosthetics.
- The precision and biocompatibility of investment-cast components are crucial for ensuring successful medical procedures.
5. Defense and Military:
- Investment casting is used to produce components for defense applications, such as firearm parts, optics mounts, and specialized equipment.
- The process allows for the creation of durable and precise components for defense systems.
6. Industrial Equipment:
- Investment casting is employed in various industrial equipment, including pumps, valves, and industrial machinery components.
- The process offers the advantage of producing parts with complex shapes and excellent surface finish.
7. Jewelry and Art:
- Investment casting is utilized in the creation of jewelry and artistic sculptures due to its ability to capture intricate details and produce high-quality surface finishes.
8. Marine and Shipbuilding:
- Investment casting is applied in marine and shipbuilding industries for producing marine engine components, propellers, and other specialized parts.
9. Sports and Recreation:
- Investment casting is used in the production of components for sports equipment such as golf club heads, fishing reels, and bicycle components.
These are just a few examples of how investment casting finds application across various industries. Its ability to produce intricate and complex components with high accuracy and surface finish makes it a valuable manufacturing process in fields where precision, quality, and performance are paramount.
Chapter 4: The Commonly Used Materials in Investment Casting
In investment casting, a variety of materials are used for both making molds (ceramic shells) and for casting alloys. The choice of materials depends on factors such as the desired properties of the final casting, the specific application, and the overall process requirements. Here are the commonly used materials in investment casting:
Materials for Making Molds (Ceramic Shells):
- Ceramic Slurry: Ceramic slurries are used to coat the wax or pattern assembly to create the ceramic shell. The slurry is made from a mixture of ceramic powder, binder, and water. Different ceramic powders, such as zircon, alumina, and silica, can be used to create the desired shell properties.
- Stucco: Stucco is a dry powder consisting of fine ceramic particles that is applied to the wet ceramic shell. It helps build up the thickness of the shell layers and adds to the shell’s strength.
- Backing Material: After the ceramic shell is created, a backing material is often used to provide support during casting. This can be a sand-based material or a refractory substance.
Alloys for Castings:
- Steel Alloys: Investment casting is commonly used for various steel alloys, including carbon steels, stainless steels, and tool steels. These alloys offer a balance of strength, durability, and corrosion resistance.
- Aluminum Alloys: Aluminum investment castings are lightweight and offer good corrosion resistance. They are used in aerospace, automotive, and other industries where weight reduction is important.
- Bronze and Brass Alloys: These copper-based alloys are often used for artistic and decorative castings, as well as in applications requiring good wear resistance.
- Nickel-Based Alloys: These alloys have excellent high-temperature properties and are used in applications requiring heat resistance, such as aerospace and power generation.
- Cobalt-Based Alloys: Similar to nickel-based alloys, cobalt-based alloys offer high-temperature performance and are used in specialized applications.
- Titanium Alloys: Investment casting is also used for titanium and its alloys, which offer high strength-to-weight ratios and corrosion resistance, making them suitable for aerospace and medical applications.
- Super Alloys: These high-performance alloys are used in extreme environments, such as high temperatures and aggressive corrosion conditions.
The choice of casting alloy depends on factors like mechanical properties, thermal characteristics, corrosion resistance, and cost. Similarly, the selection of mold materials depends on the casting process and the desired properties of the final castings. Investment casting provides flexibility in material selection, enabling the production of a wide range of components with varying properties and characteristics.
Chapter 5: The Molds for Investment Casting
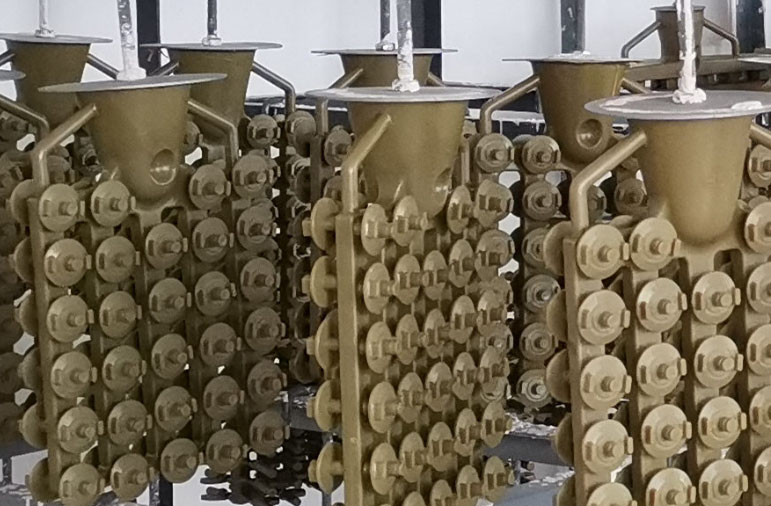
The mold preparation process in investment casting is a critical step that involves selecting the mold material, designing the mold, and manufacturing the mold to create the ceramic shell for the casting. Here’s an overview of the mold preparation process in investment casting:
1. Mold Material Selection:
- The mold material, also known as the ceramic slurry, is a mixture of ceramic powder, binder, and water.
- The choice of ceramic powder depends on factors such as the desired shell properties (strength, thermal stability), casting material, and process requirements.
- Common ceramic powders used include zircon, alumina, silica, and combinations of these materials.
2. Mold Design:
- The mold design includes the layout of the gating system, sprues, runners, and gates that allow molten metal to flow into the mold cavity and gases to escape.
- The design also considers factors such as pattern removal, shrinkage allowances, and overall part geometry.
- The gating system should ensure even filling of the mold cavity to prevent defects.
3. Mold Manufacturing Process:
- The mold manufacturing process involves several steps to create the ceramic shell that will encase the wax pattern and later receive the molten metal.
3.1 Wax Pattern Assembly:
- The wax pattern, created to replicate the shape of the desired part, is attached to a gating system (sprues, runners, gates) to form an assembly.
3.2 Ceramic Coating (Slurry Coating):
- The wax pattern assembly is repeatedly dipped into a ceramic slurry, which adheres to the pattern surface.
- After each dip, the assembly is coated with a fine ceramic stucco to build up shell thickness and strength.
3.3 Dewaxing (Burnout):
- The coated assembly is heated to remove the wax pattern. This can be done using autoclaves or ovens.
- The dewaxing process leaves behind a hollow mold cavity inside the ceramic shell.
3.4 Preheating:
- The ceramic shell is preheated to a specific temperature to ensure proper metal flow and solidification during casting.
3.5 Metal Pouring and Solidification:
- Molten metal is poured into the preheated ceramic shell mold, filling the mold cavity.
3.6 Shell Removal and Finishing:
- Once the metal has solidified, the ceramic shell is broken or removed to reveal the cast metal part.
- The casting is then cleaned, finished, and may undergo additional processes, such as machining or heat treatment.
The mold preparation process in investment casting is crucial to achieving accurate and high-quality castings. Proper mold design and manufacturing ensure that the molten metal flows evenly into the mold cavity, minimizing defects and achieving the desired part geometry. The choice of mold material and meticulous attention to each step of the process contribute to the success of the investment casting process.
Chapter 6: Investment Casting Cooling and Solidification in Molds
The cooling and solidification process of investment casting is a critical phase that directly affects the microstructure, mechanical properties, and overall quality of the castings. Proper control of the cooling and solidification process is essential to achieve desired casting characteristics. Here’s an overview of the cooling and solidification process in investment casting and how to control the solidification structure of castings:
Cooling and Solidification Process:
- Initial Solidification: As the molten metal is poured into the ceramic shell mold, it comes into contact with the cooler mold surfaces. This initiates the solidification process.
- Nucleation: Nucleation sites form where the solidification process begins. These sites are influenced by factors like mold material, shell thickness, and temperature gradient.
- Growth of Solid Crystals: As solidification progresses, crystals (grains) of the casting material grow from the nucleation sites. The arrangement and size of these grains determine the microstructure of the casting.
- Directional Solidification: Investment casting often involves directional solidification, where the solidification front progresses from the pouring gate towards the mold cavity. This can help control the formation of defects like porosity and shrinkage.
- Solidification Shrinkage: As the metal transforms from liquid to solid, it contracts and undergoes solidification shrinkage. This can lead to the development of internal stresses and potential defects.
Control of Solidification Structure:
- Chill Plates or Cores: The use of chill plates or cores in the mold can influence the solidification rate and direction, helping to control grain structure and minimize defects.
- Mold Design and Gating: Proper mold design, including gating and riser systems, helps control the flow of molten metal and can promote directional solidification.
- Riser Design: Well-designed risers (feeders) ensure that molten metal is available to compensate for solidification shrinkage, reducing the likelihood of porosity and defects.
- Cooling Rate: Controlling the cooling rate of the mold influences the grain growth and microstructure. Slower cooling rates may lead to finer grain structures and improved mechanical properties.
- Alloy Composition: The composition of the casting alloy also affects solidification behavior. Alloying elements can influence the size and distribution of grains and the formation of phases.
- Ceramic Shell Properties: The properties of the ceramic shell, such as its thermal conductivity and insulation, influence the rate of heat transfer and, consequently, the solidification process.
- Heat Treatment: Post-casting heat treatment processes can be applied to control the microstructure and improve mechanical properties.
By carefully controlling the cooling and solidification process and implementing appropriate strategies, investment casting manufacturers can achieve desired microstructures, minimize defects, and produce castings with consistent and desired mechanical properties. Solidification control is a critical aspect of ensuring high-quality investment castings.
Chapter 7: The Method of Demolding Investment Castings
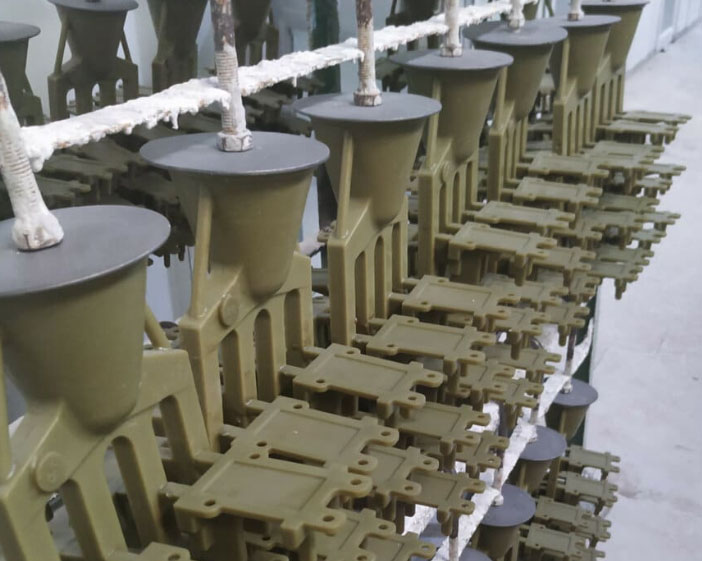
Demolding investment castings and post-treatment processes are essential steps to ensure that the castings are free of mold residues, defects, and have the desired surface finish and properties. Here are the methods of demolding investment castings and common post-treatment processes:
1. Demolding Investment Castings:
- After solidification, the ceramic shell needs to be removed to reveal the cast metal part. Demolding can be achieved through various methods:1.1 Mechanical Knockout: The ceramic shell is mechanically broken or knocked off the casting using hammers, vibrations, or pneumatic tools.1.2 Thermal Shock: Heating the casting quickly and then rapidly cooling it can cause the ceramic shell to crack, facilitating its removal.1.3 Abrasive Blasting: Abrasive materials, such as sand or grit, are directed at the casting to remove the ceramic shell through abrasion.1.4 Chemical Dissolution: Immersing the casting in a chemical solution that dissolves the ceramic shell, leaving the metal casting intact.
2. Removing Mold Residues:
- After demolding, some mold residues might still adhere to the casting. These residues need to be removed to ensure a clean surface:2.1 Sandblasting: Abrasive blasting using sand or other media can remove remaining shell residues and provide a uniform surface finish.2.2 Chemical Cleaning: Immersing the casting in a chemical solution can dissolve remaining mold residues. Proper handling of chemicals is essential.
3. Surface Treatment:
- Surface treatment processes enhance the appearance, durability, and corrosion resistance of the casting:3.1 Machining: Machining processes such as milling, turning, and grinding are used to achieve precise dimensions and surface finish.3.2 Grinding and Polishing: Grinding and polishing processes can improve surface smoothness and appearance.3.3 Shot Peening: Small metal beads or shot are directed at the casting’s surface to improve surface finish and impart compressive stress for increased fatigue resistance.3.4 Plating and Coating: Applying a protective plating or coating (e.g., chrome, nickel, zinc) can enhance corrosion resistance and aesthetics.
4. Heat Treatment:
- Heat treatment processes are used to alter the material properties of the casting, such as hardness, strength, and dimensional stability:4.1 Annealing: Heating and slow cooling to relieve internal stresses and improve machinability.4.2 Tempering: Reheating and controlled cooling to adjust hardness and toughness.4.3 Solution Heat Treatment: Heating and quenching to dissolve alloying elements and then aging to achieve desired properties.
5. Inspection and Testing:
- Comprehensive inspection and testing ensure that the castings meet quality and performance requirements:5.1 Visual Inspection: Examining the casting for surface defects, dimensional accuracy, and overall appearance.5.2 Non-Destructive Testing (NDT): Techniques like X-ray, ultrasonic testing, and dye penetrant inspection are used to detect internal defects.5.3 Mechanical Testing: Conducting tensile, hardness, impact, and other tests to evaluate mechanical properties.5.4 Dimensional Inspection: Measuring the casting’s dimensions using precision instruments to ensure adherence to specifications.
Each step in the demolding and post-treatment processes contributes to the quality, appearance, and performance of investment castings. Proper execution of these steps is crucial to producing castings that meet the desired standards and application requirements.
Chapter 8: The Quality Control and Testing of Investment Casting
Quality control and testing are essential aspects of ensuring that investment castings meet the desired standards and performance requirements. Various methods are employed to assess the quality and integrity of investment casting castings. Here’s an overview of quality control and testing methods for investment castings:
1. Visual Inspection:
- Visual inspection involves examining the casting’s surface for defects, such as cracks, porosity, surface irregularities, and other visual imperfections.
- Skilled inspectors use visual cues to identify irregularities and ensure that the casting meets aesthetic and surface finish requirements.
2. Dimensional Measurement:
- Precise dimensional measurement ensures that the casting’s dimensions conform to design specifications.
- Coordinate measuring machines (CMM), calipers, micrometers, and other precision instruments are used to measure key features and tolerances.
3. Non-Destructive Testing (NDT):
- NDT techniques are used to detect defects and irregularities without causing damage to the casting. Common NDT methods include:3.1 X-ray Inspection: X-rays are used to examine the internal structure of the casting, revealing defects such as porosity, inclusions, and voids.3.2 Ultrasonic Testing: High-frequency sound waves are used to detect internal flaws, porosity, and voids within the casting.3.3 Dye Penetrant Inspection: A liquid dye is applied to the casting’s surface. After excess dye is wiped away, a developer is applied to reveal surface defects.3.4 Magnetic Particle Inspection: Magnetic particles are applied to the casting’s surface. Defects create magnetic fields that attract the particles, revealing surface cracks and flaws.
4. Material Analysis:
- Material analysis is performed to verify the composition and properties of the casting material:4.1 Spectroscopy: Analyzing the chemical composition of the casting material to ensure it meets specifications.4.2 Hardness Testing: Measuring the hardness of the casting to assess its mechanical properties.
5. Mechanical Testing:
- Mechanical testing evaluates the casting’s strength, ductility, and other mechanical properties:5.1 Tensile Testing: Applying force to a sample to measure its tensile strength, yield strength, and elongation.5.2 Impact Testing: Evaluating the casting’s ability to withstand impact forces.
6. Metallurgical Analysis:
- Metallurgical analysis involves studying the casting’s microstructure to assess grain size, inclusion content, and phase distribution.
7. Pressure Testing:
- Pressure testing involves subjecting the casting to pressurized fluids or gases to detect leaks and assess the integrity of the casting.
8. Surface Finish Testing:
- Surface roughness and finish are measured using specialized equipment to ensure they meet design specifications.
9. Documentation and Traceability:
- Comprehensive documentation of testing results, material certifications, and other relevant data ensures traceability and accountability.
Quality control and testing processes play a crucial role in ensuring that investment castings meet the required standards for performance, reliability, and safety. By employing a combination of these methods, manufacturers can identify and address potential defects and deviations from specifications, thereby delivering high-quality castings to their customers.