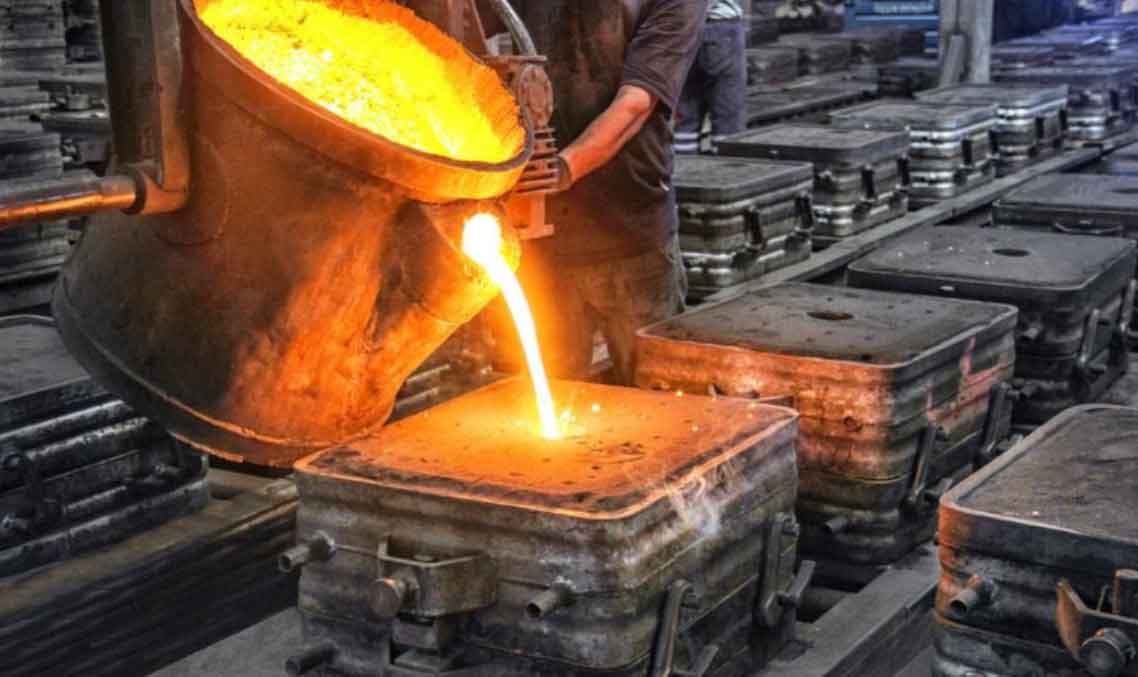
Material selection in sand casting is a critical aspect that directly impacts the performance, cost, and quality of the final castings. Experienced sand casting manufacturers consider several key factors when choosing materials. Here are some insights from experienced manufacturers on material selection:
1. Application Requirements:
- The first consideration is the specific requirements of the casting’s intended application. Manufacturers assess factors such as mechanical properties, corrosion resistance, wear resistance, thermal conductivity, and temperature stability to determine the most suitable material.
2. Alloy Availability and Cost:
- Manufacturers consider the availability and cost of different alloys. Commonly used materials like aluminum, steel, and iron may be more cost-effective due to their wide availability, while specialty alloys may be chosen for unique properties despite higher costs.
3. Casting Complexity:
- The complexity of the casting’s design and geometry is taken into account. Certain materials may be more challenging to cast for intricate shapes, while others offer better flowability and mold fill characteristics.
4. Weight and Density:
- The weight and density of the casting are important considerations, especially in automotive, aerospace, and transportation industries where lightweight materials are often preferred for fuel efficiency.
5. Heat Treatment and Post-Processing:
- Manufacturers consider how easily the chosen material can be heat-treated or post-processed to achieve desired properties and surface finishes.
6. Casting Process Compatibility:
- The material must be compatible with the sand casting process. Some materials may require special handling or processing techniques, impacting overall production efficiency.
7. Dimensional Stability:
- Materials with good dimensional stability are preferred to ensure the casting maintains its shape and size throughout its service life.
8. Service Environment:
- The environmental conditions in which the casting will operate play a significant role in material selection. Corrosive environments, extreme temperatures, and aggressive chemicals all influence material choice.
9. Regulatory Compliance:
- Manufacturers must ensure that the chosen material meets relevant industry standards and regulatory requirements, especially in applications where safety is critical.
10. Previous Experience and Expertise:
- Manufacturers may lean towards materials they are familiar with and have extensive experience casting. Familiarity with a material streamlines the production process and reduces the risk of defects.
11. Customer Preferences:
- Customer preferences and specific contractual requirements also influence material selection. Manufacturers work closely with customers to identify the most suitable material based on their needs and preferences.
12. Eco-Friendly Considerations:
- In line with sustainable practices, manufacturers may prioritize materials that are recyclable, have low environmental impact, or are sourced responsibly.
Experienced manufacturers draw from their knowledge of materials and their real-world application to make informed decisions about material selection. They collaborate closely with design engineers and customers to ensure that the chosen material aligns with performance requirements, production feasibility, and budget considerations.