With the improvement of the world’s technological level, people’s demand for energy is increasing day by day, and material conservation has become the goal of various countries’ efforts. Traditional casting in the casting industry consumes both manpower and financial resources, while investment casting can better achieve minimal and no surplus processing. The combination of computer simulation and actual casting processes has been increasingly applied in the casting industry, resulting in products that have scientific basis and can meet standards for production practice. The stainless steel ball valve has a wide range of applications and can be used on control valves for related fluid transportation control routes. It bears high pressure, so the production quality requirements for stainless steel ball valves are also quite strict, and cracks, cold shuts, and shrinkage porosity are not allowed. Stainless steel ball valves produced under the original process conditions are generally formed by empirical methods, and there are often shrinkage defects at the valve body and flange corners, resulting in a low yield. In order to reduce shrinkage defects, improve the yield of stainless steel ball valves, and save development costs, redesigning the molding process gating system is a major way to reduce defects.
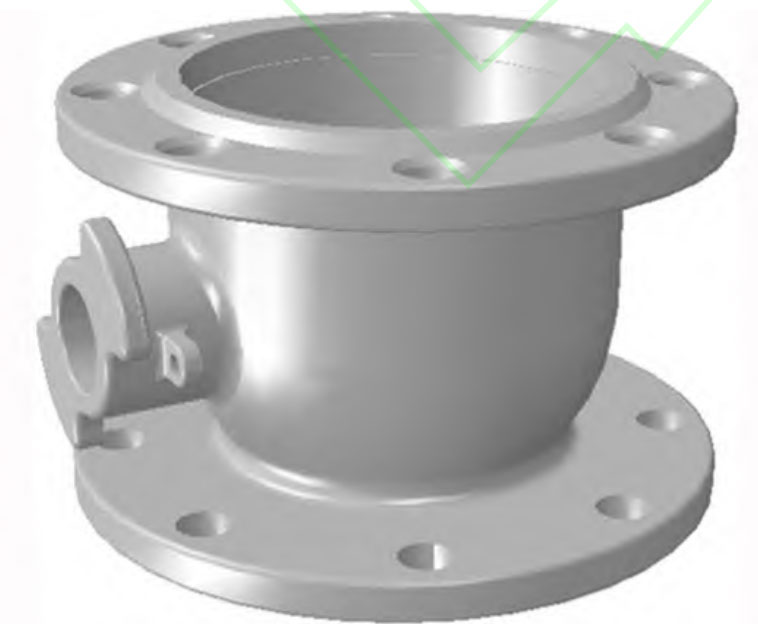
In some recent studies on investment casting, Xu Rongfu et al. studied the investment centrifugal casting process of high Nb titanium aluminum based exhaust valve castings. Through a combination of simulation and experiment, it was confirmed that castings with qualified metallographic structure can be produced under the conditions of mold shell filling time of 3.8 s, powder liquid ratio of 1.5:1, and stirring time of 30 minutes. Yang Xindi et al. conducted research on the problem of shrinkage and porosity in the support plates of turbine casings. By improving the exhaust channel, adjusting the pouring position and duration of the support plates, and adjusting the solidification sequence of the castings, the quality of the castings produced met the requirements of ASTM E192 standard. Zhang Xiaoguang et al. studied the investment casting process of automotive transmission control rods and eliminated the shrinkage porosity and shrinkage defects of 45 steel control rods by changing the pouring system. Song Wei et al. used ProCAST software to simulate and analyze the solidification process of large section cast steel main bearing seat. The results showed that the shrinkage defects in the key areas of the casting could be significantly reduced by horizontal pouring and placing the external chill. Huang et al. simulated and studied the investment casting process of 17-4PH stainless steel impeller in centrifugal pumps using AnyCasting simulation software. They found that the complex internal structure and uneven thickness of the impeller were the reasons for the shrinkage and porosity of the impeller blades. Finally, the defects were eliminated by adding a riser, changing its size, and adjusting process parameters. Suwankan et al. analyzed the solidification process of 431 stainless steel fishing net hooks and identified the reasons for the easy occurrence of shrinkage, cold shuts, pinholes, and cracks in fishing net hooks. By designing a 90 ° tree structure mold and comparing the filling of circular and hexagonal section flow channels, the defects at the top of the hook were ultimately eliminated.
At present, there is relatively little research on optimizing the shrinkage defects of 304 stainless steel hydraulic valves. In order to improve the overall performance of castings and reduce the scrap rate of products, simulation was conducted on the traditional process of 304 stainless steel ball valves to identify the causes of defects. By designing the pouring system and designing orthogonal experiments, a set of optimal process parameters was found to optimize the shrinkage defects at the corners of the casting valve body and flange. After production verification, the shrinkage hole defect at the corner of the ball valve body and flange has disappeared.