There are eight vertical parting boxless sand injection extrusion molding production lines, mainly producing refrigerator refrigeration compressor castings, automobile brake, clutch, steering knuckle and other castings, using the wet clay sand molding process. The selection of pulverized coal for wet mold clay sand mainly plays a role in sand resistance and surface smoothness of castings. The selection of pulverized coal is due to its low price, easy supply and convenient application.
However, the use of pulverized coal also has disadvantages: the dirty and deteriorating working conditions, the residue of pulverized coal in the air of the working environment accounts for about 50%, and a large amount of volatile gas harmful to health will be emitted during casting; The ash and coke formed after shakeout remain in the sand mold, and it is necessary to add more water and bentonite to maintain the appropriate strength and toughness of the wet clay sand; Pulverized coal may also cause spontaneous combustion during molding.
Therefore, in the 1960s and 1970s, European and American countries made great efforts to study and try out the wet-formed clay sand without coal powder. Some units in China have also carried out similar research since the late 1970s, and are still studying the wet-formed clay sand without coal powder or reducing the amount of coal powder.
The cylinder base of refrigerator compressor is the company’s highest annual output casting product, made of HT200, with a single piece of about 2 kg. However, the problem of sand sticking in the muffler cavity of the cylinder seat casting has not been completely solved, as shown in the figure. The red mark in the figure shows the phenomenon of sand sticking in the muffler cavity, and the inner wall is rough and white.
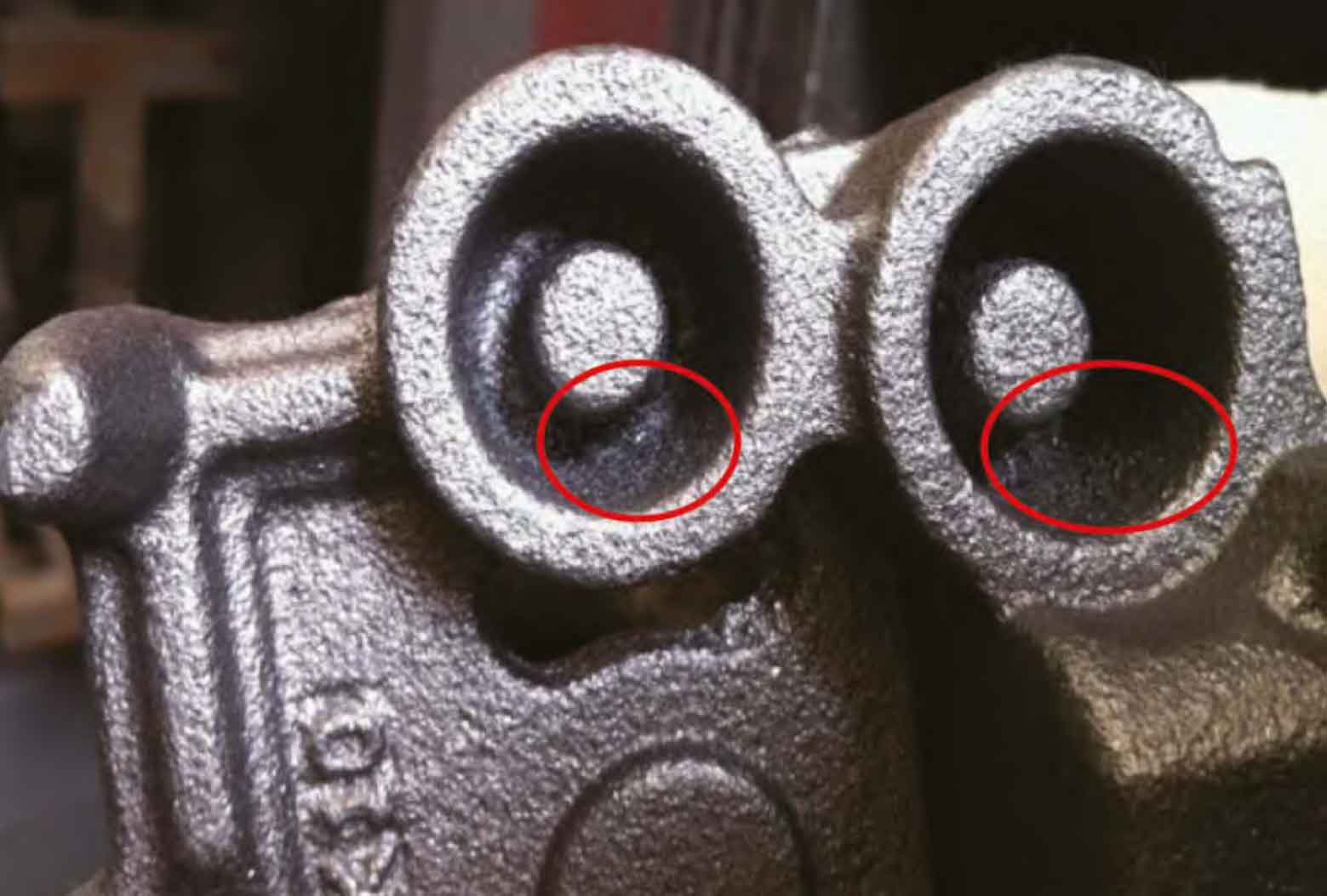
To sum up, it is feasible to improve the current molding process of wet clay sand, that is, to cancel the molding process of pulverized coal; In order to ensure the mass production of qualified gray iron castings without sand sticking and blowhole defects, it is necessary to control the oolization rate of molding sand to be less than 15% for the regeneration and recycling of non-pulverized coal wet molding clay sand.