As a commercial metal structure material, magnesium alloy has the advantages of high specific strength, good casting formability, superior damping, shock absorption and noise reduction performance, strong electromagnetic shielding ability, good machining and surface decoration performance, easy recycling and other advantages .
Magnesium alloy precision castings have been widely used in the aviation industry since the 1950s. In b236 bombers, a total of 8600kg of magnesium has been used, 30% of which are magnesium alloy precision castings [13]. In recent years, the aviation industry has adopted various measures to increase the consumption of magnesium alloy precision castings, such as aero-engine parts, fuel tank partitions, aircraft stringers, wing ribs, aircraft compartment partitions, helicopter engine rear reduction gearbox, turbojet engine front support shell and other bearing and auxiliary components.
Through in-depth research on the technical foundation of precision casting of magnesium alloy in Europe and America and other developed countries, we have improved the quality of raw and auxiliary materials for precision casting, adopted advanced process equipment, integrated computer-aided process design and advanced management technology, and developed the integrated gas protection technology of magnesium alloy smelting, liquid metal transportation and counter gravity casting, The melt of magnesium alloy is effectively protected by gas during smelting, transferring and pouring, and the mass production of magnesium alloy precision casting is realized. Figure 4 shows typical magnesium alloy precision casting for foreign aeroengine. The domestic cast magnesium alloy has few brands, low strength and poor corrosion resistance, which is mainly used in various parts of aeroengine, such as gearbox, shell, air inlet, etc. At present, the maximum size of domestic magnesium alloy precision casting is about 2000 mm, and the wall thickness is about 5 mm.
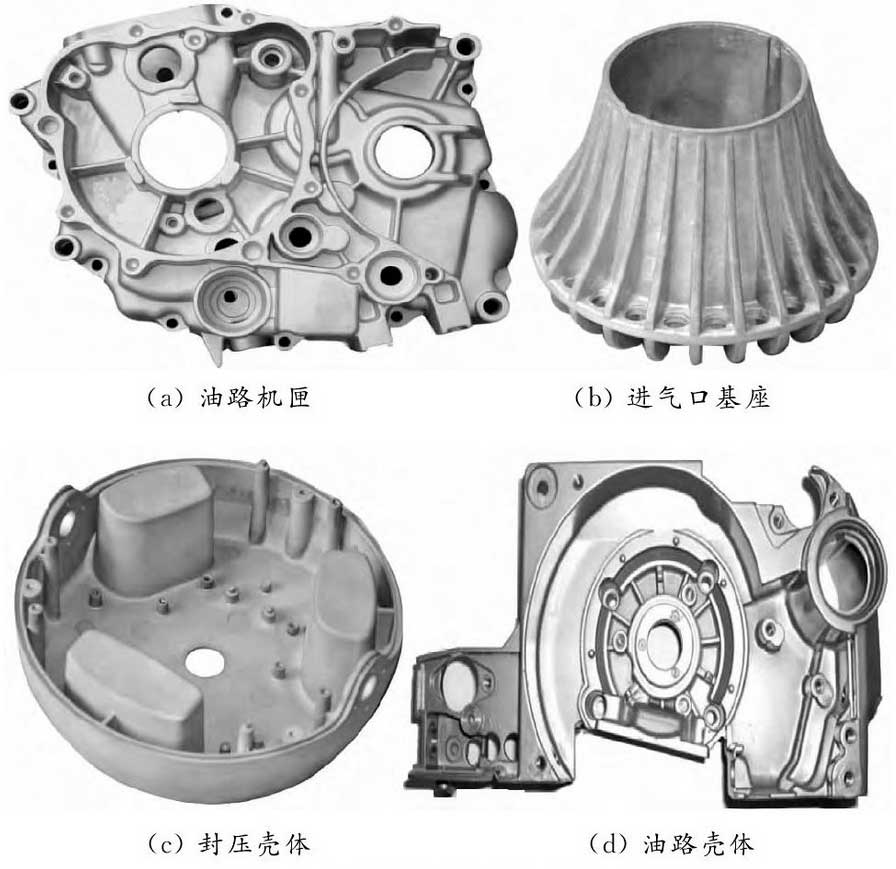