Investment casting, also known as precision casting or lost wax casting, is a metal casting technique that offers high precision and versatility in producing complex and intricate parts. It involves creating a wax pattern, investing it in a ceramic shell, melting out the wax, and pouring molten metal into the resulting cavity. Here are some key aspects of investment casting:
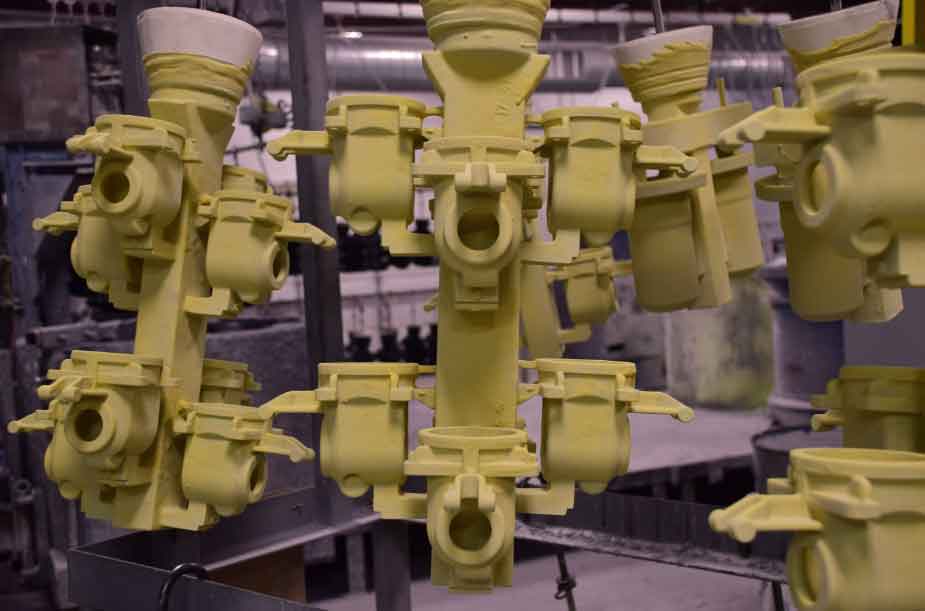
- Complex Geometries: Investment casting is renowned for its ability to produce parts with intricate shapes, thin walls, and complex internal features that are difficult or impossible to achieve with other casting methods. It allows for the production of highly detailed and precise components, including turbine blades, medical implants, jewelry, and art pieces.
- Accuracy and Precision: Investment casting provides excellent dimensional accuracy and tight tolerances, resulting in parts with high precision. The process captures the details of the original wax pattern, ensuring that the final casting matches the desired specifications. This level of accuracy makes investment casting suitable for applications where precise fit and performance are critical.
- Versatility in Materials: Investment casting supports a wide range of materials, including ferrous and non-ferrous alloys, stainless steel, aluminum, titanium, and superalloys. This versatility enables the production of parts with specific material properties, such as high strength, corrosion resistance, heat resistance, and wear resistance, to meet the requirements of various industries.
- Surface Finish and Detail: Investment casting produces parts with excellent surface finish, eliminating or minimizing the need for extensive post-casting machining. The ceramic shell used in the process provides a smooth and detailed surface, reducing the surface roughness and enhancing the aesthetics of the final part. This feature is particularly important for applications in industries like jewelry and art.
- Design Freedom: Investment casting offers design freedom, allowing for the creation of complex and intricate parts with minimal restrictions. It enables designers to incorporate intricate details, undercuts, thin walls, and internal features that may be challenging to achieve with other manufacturing methods. This flexibility in design makes investment casting a preferred choice for customized or low-volume production.
- Cost Efficiency: Although investment casting can be more expensive than other casting methods due to the complex process and materials involved, it can be cost-effective for producing high-quality, low-volume or complex parts. The ability to eliminate or reduce the need for extensive machining and assembly operations can help offset the initial investment.
- Reduced Material Waste: Investment casting minimizes material waste since the process uses only the exact amount of metal required to fill the mold cavity. Additionally, the ability to reuse the ceramic shell and recycle excess metal contributes to a more sustainable and environmentally friendly manufacturing process.
- Wide Range of Applications: Investment casting finds applications in various industries, including aerospace, automotive, medical, jewelry, defense, and industrial sectors. It is commonly used for producing components such as turbine blades, aircraft engine parts, medical implants, automotive parts, and intricate jewelry pieces.
Investment casting combines precision, versatility, and design freedom, making it a preferred choice for manufacturing complex and high-quality parts. Its ability to produce intricate details, achieve tight tolerances, and work with a variety of materials makes it a valuable technique in numerous industries where precision and complexity are paramount.