To improve casting integrity and address defects in lost foam casting, several strategies can be employed. Here are some key strategies to consider:
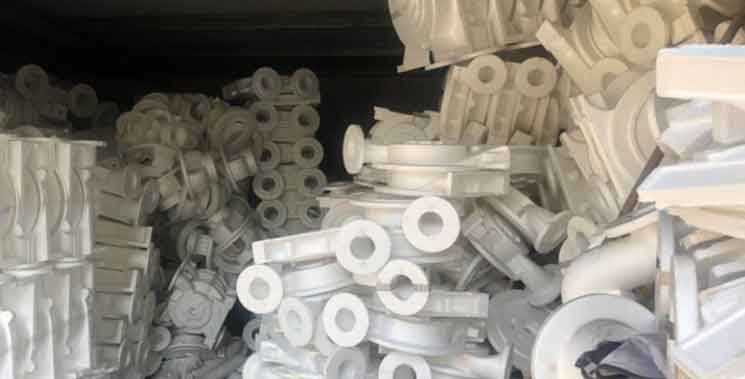
- Pattern Design and Construction:
- Optimize the design of foam patterns to ensure proper filling and solidification.
- Use high-quality foam materials with consistent density and dimensional accuracy.
- Pay attention to the pattern construction process to avoid defects like loose or distorted patterns.
- Mold Coating and Preparation:
- Apply a uniform and appropriate mold coating to enhance surface finish and reduce defects.
- Ensure proper drying of the mold to eliminate moisture and prevent gas-related defects.
- Pouring Parameters:
- Control pouring temperature to avoid overheating or underheating the metal, which can lead to defects.
- Optimize pouring rate and time to achieve complete filling without causing turbulence.
- Gating System Design:
- Design a well-balanced gating system to ensure smooth metal flow and minimize turbulence.
- Use a proper sprue, runner, and gate dimensions to facilitate efficient filling and reduce defects.
- Riser Design:
- Position risers correctly to provide adequate feeding and minimize shrinkage-related defects.
- Optimize the size and placement of risers to promote proper directional solidification.
- Metal Quality and Treatment:
- Use high-quality molten metal with appropriate alloy composition and proper treatment processes.
- Implement effective degassing and filtration techniques to remove impurities and minimize gas and inclusion defects.
- Process Control and Monitoring:
- Implement rigorous process control measures to ensure consistency and repeatability.
- Monitor and control critical process parameters such as mold temperature, pouring temperature, and cooling rate.
- Quality Assurance and Inspection:
- Implement comprehensive quality assurance procedures to detect and address defects.
- Conduct regular inspections using visual examination, dimensional measurements, and non-destructive testing methods.
- Training and Knowledge Sharing:
- Provide training to personnel involved in the lost foam casting process to ensure proper technique and understanding of quality requirements.
- Encourage knowledge sharing and collaboration among team members to learn from experiences and improve the process.
- Continuous Improvement and Lessons Learned:
- Analyze casting defects and their root causes to identify areas for improvement.
- Implement corrective actions based on lessons learned to prevent future defects and enhance casting integrity.
By implementing these strategies and continuously refining the lost foam casting process, manufacturers can address defects, improve casting integrity, and achieve higher-quality castings.