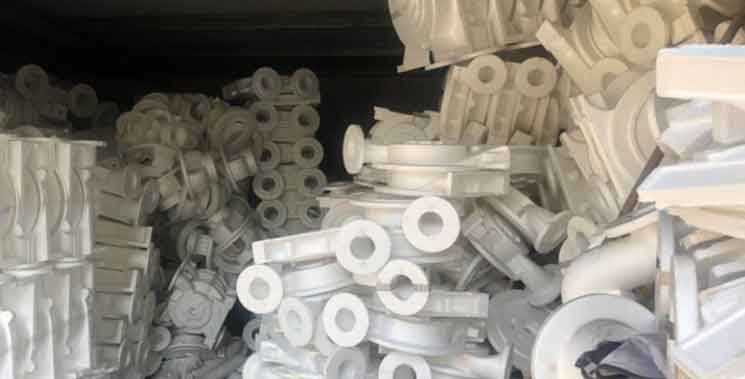
Investment casting, also known as precision casting or lost wax casting, unlocks a powerful combination of customization and efficiency in component manufacturing. This versatile process offers several benefits that contribute to both the customization of components and the overall manufacturing efficiency. Here’s how investment casting achieves this balance:
- Design Flexibility and Customization: Investment casting allows for the creation of highly customized components. The process accommodates intricate and complex designs, enabling the production of components with unique shapes, intricate details, and specialized features. This design flexibility empowers engineers and designers to tailor components to specific requirements, incorporating features that optimize performance, functionality, and aesthetics.
- Material Selection: Investment casting accommodates a wide range of materials suitable for different applications. From various metals like stainless steel, titanium, and aluminum to specialized alloys and superalloys, investment casting offers a choice of materials to match the specific performance and property requirements of the component. This versatility in material selection allows for customization based on factors such as strength, weight, corrosion resistance, and heat resistance.
- Near-Net Shape Production: Investment casting excels at near-net shape production, meaning that the components are cast close to their final shape with minimal machining or post-casting operations required. This capability significantly reduces material waste, machining time, and associated costs. Near-net shape production also contributes to greater efficiency in manufacturing, as it eliminates the need for extensive material removal or complex machining setups.
- Complex Geometry and Intricate Details: Investment casting enables the production of components with intricate geometries and fine details that are difficult to achieve with other manufacturing methods. This capability is particularly beneficial for components with internal passages, thin walls, complex curves, or internal features that require precision and accuracy. Investment casting captures the intricate details of the pattern, resulting in high-quality castings with excellent dimensional accuracy.
- Consistent Quality and Performance: Investment casting ensures consistent quality and performance across multiple components. The process enables the replication of intricate patterns and designs with high fidelity, resulting in consistent dimensions, tolerances, and mechanical properties. This consistency is crucial for components that require uniformity in performance, fit, and functionality.
- Reduced Assembly and Joining: Investment casting allows for the integration of multiple components into a single casting, minimizing the need for separate parts and subsequent assembly operations. This reduces the risk of failure at joints or interfaces and simplifies the manufacturing process. Integration of components also enhances the overall structural integrity and reliability of the final product.
- Efficient Production Workflow: Investment casting offers an efficient production workflow by reducing the number of manufacturing steps and eliminating the need for extensive machining or fabrication. The process streamlines the manufacturing cycle, reducing lead times, labor costs, and the potential for errors or inconsistencies associated with manual assembly or joining processes.
- Scalability: Investment casting is scalable, making it suitable for both low-volume and high-volume production. The process can accommodate varying production requirements, allowing manufacturers to scale production based on market demand without compromising on customization or quality.
Investment casting strikes a balance between customization and manufacturing efficiency, enabling engineers and designers to create highly customized components while maintaining cost-effectiveness and production efficiency. The process unlocks new possibilities in component manufacturing, offering the flexibility to meet diverse application requirements while delivering consistent quality, precision, and performance.