Resin sand casting has indeed taken the spotlight in the field of foundry processes due to several innovative advancements. These innovations have significantly enhanced the efficiency, precision, and overall capabilities of resin sand casting. Here are some notable innovations in resin sand casting:
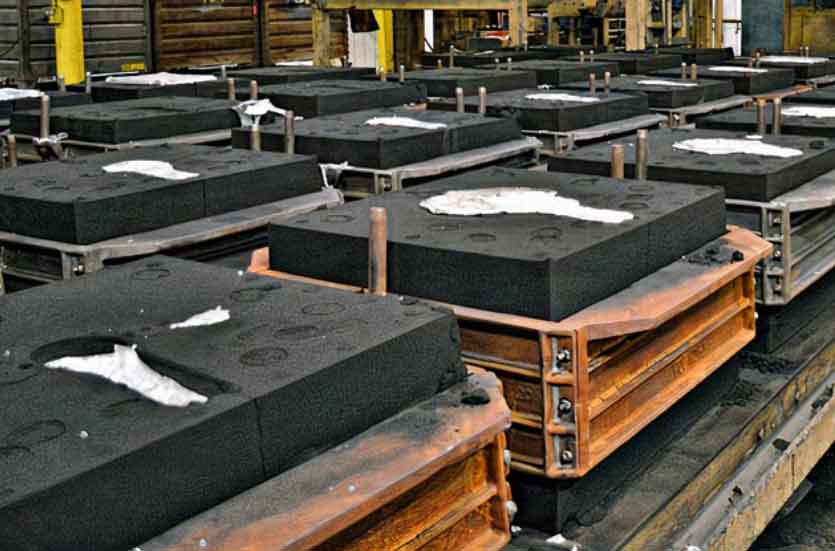
- Digital Design and Simulation: The integration of digital design and simulation tools has revolutionized resin sand casting. Advanced computer-aided design (CAD) software allows for the creation and modification of intricate patterns with high precision. Simulation software enables engineers to predict and optimize the casting process, reducing the need for costly trial and error iterations.
- Additive Manufacturing of Patterns: The emergence of additive manufacturing, commonly known as 3D printing, has provided a new approach to pattern production in resin sand casting. 3D printing allows for the direct fabrication of complex patterns with high accuracy, eliminating the need for traditional pattern-making techniques. This enables faster prototyping, design iteration, and customization.
- Improved Pattern Materials: The development of new foam and resin materials for pattern production has enhanced the quality and durability of patterns in resin sand casting. Advanced foam materials provide increased dimensional stability, better surface finish, and improved resistance to thermal expansion and contraction during the casting process.
- Automation and Robotics: Automation and robotics have found their way into resin sand casting processes, improving efficiency and consistency. Automated systems can handle various tasks such as pattern assembly, mold preparation, pouring, and post-casting operations. Robotic arms can handle complex operations with precision, speed, and repeatability, minimizing human error and enhancing production throughput.
- Real-Time Monitoring and Quality Control: Innovations in sensing technologies and data analytics have enabled real-time monitoring and quality control in resin sand casting. Sensors embedded in molds and casting equipment can capture and analyze data on factors like temperature, pressure, and vibrations during the casting process. This data can be used to optimize process parameters, identify defects, and ensure consistent quality.
- Environmental Considerations: Sustainable practices have gained importance in foundry processes, including resin sand casting. Innovations in environmental control and waste management have reduced the environmental impact of resin sand casting. These innovations include the use of eco-friendly resins, recycling of sand molds, energy-efficient equipment, and advanced air filtration systems to minimize emissions.
- Integration of Artificial Intelligence (AI) and Machine Learning (ML): The integration of AI and ML technologies is revolutionizing resin sand casting by enabling predictive modeling, optimization, and process control. AI algorithms can analyze large amounts of data and make predictions on casting quality, defect detection, and process optimization. ML algorithms can learn from historical data and improve process parameters for enhanced casting outcomes.
These innovative advancements in resin sand casting have transformed the traditional foundry processes, leading to improved productivity, cost-effectiveness, and product quality. The integration of digital tools, additive manufacturing, automation, real-time monitoring, sustainability practices, and AI/ML technologies has positioned resin sand casting at the forefront of modern foundry practices. These innovations continue to push the boundaries of what is possible in metal component manufacturing.