The samples of gray cast iron were treated by isothermal quenching and boronizing. The isothermal quenching process of gray cast iron is as follows: the sample is heated to 900 ℃ in an electric furnace for 30 minutes to austenitize, and then the gray cast iron is isothermal quenched for 1 h, 2 h, 3 h and 4 h in a salt bath of 240 ℃, 300 ℃ and 360 ℃, and air cooled. The boronizing isothermal quenching process of gray cast iron is as follows: heat preservation in 950 ℃ salt bath containing borax (sodium borate PA: Na2B4O7 · 10h2o) and aluminum (10%, mass fraction) for 2 h and 4 h, and then isothermal quenching the sample directly in another bath. The gray cast iron isothermal quenching bath has three temperatures to determine the most economical and feasible process without additional heating. The optical microscope (OM) was used to analyze the metallography of the sample, study the characteristics of its microstructure and surface layer, and determine the hardness of the sample matrix (HRC) and the hardness of the infiltrated layer (hv0.1).
The adhesive wear characteristics of Austempered samples and boronized layer of gray cast iron were tested by calotest test method with sphere fixed. The diameter of 52100 steel sphere is 25.4 mm and the hardness is 60 HRC. The test force is 160 G and the rotating speed is 400 R / min. The test duration of each sample is 5 min, 10 min, 15 min, 20 min and 40 min respectively. After each test, calculate the volume of wear (spherical cap) according to the formula.
Where: V is the worn volume; D is the diameter of spherical cap; R is the radius of the sphere. Figure 1 shows the microstructure of pearlite matrix gray cast iron as cast and after isothermal quenching. The original pearlite structure of gray cast iron was successfully transformed into austenitic ferrite by isothermal quenching (Fig. 1 (b), Fig. 1 (c) and Fig. 1 (d)). Fig. 1 (b) and Fig. 1 (d) show that the microstructure of gray cast iron isothermal quenched at 240 ~ 300 ℃ is smaller than that of gray cast iron isothermal quenched at 360 ℃, which is caused by the large difference between austenitizing temperature and isothermal quenching temperature. A lower austenitizing temperature will reduce the diffusion rate of carbon in the original austenite (slow down the growth of ferrite crystals), but it is conducive to the nucleation of ferrite sheets, resulting in the production of a large number of smaller crystals and the formation of a fine structure called lower austenite ferrite. When the isothermal quenching temperature of gray cast iron is high, i.e. 360 ℃, the diffusion rate of carbon is large, resulting in the formation of coarse microstructure called upper austenitic ferrite. On the other hand, the isothermal time of isothermal quenching has no obvious effect on the microstructure of gray cast iron.
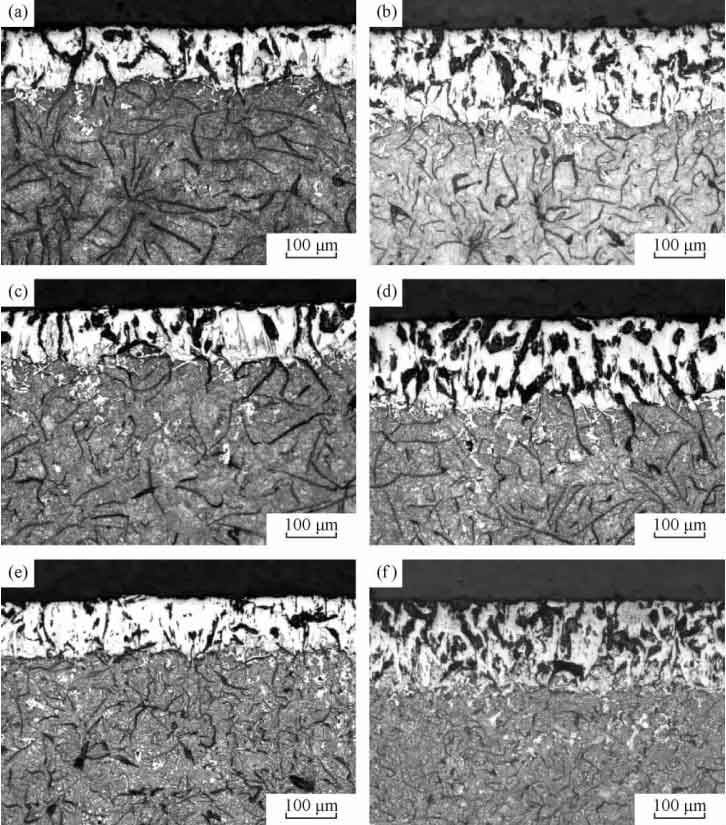
The cross-sectional structure of the sample boronized and Austempered at three temperatures is shown in Figure 2. It can be seen that there are three characteristic areas: (I) iron boride layer containing graphite sheet; (II) infiltration layer matrix interface; (III) matrix. The average thickness of boride layer formed by Boronizing for 2 h and 4 h is 100 respectively μ M and 135 μ m. It shows that the growth of boronizing layer depends on Boronizing time.
The hardness measurement results of samples and as cast materials of gray cast iron Austempered at 240 ℃, 300 ℃ and 360 ℃ for 1 h, 2 h, 3 h and 4 h are shown in Fig. 3. The data in Fig. 3 shows that the hardness of the sample Austempered at a lower temperature (240 ~ 300 ℃) is higher than that of the sample Austempered at 360 ℃. The reason is that the microstructure of gray cast iron is relatively fine when the isothermal quenching temperature is low. Interestingly, at a certain isothermal temperature, the hardness does not change significantly with the change of isothermal time. The average hardness of boronized isothermal quenching layer obtained after 2 h and 4 h boronizing is 1473.5 ± 88 HV and 1562.5 ± 37 HV respectively.
Fig. 4 ~ Fig. 6 show the micro adhesive wear test results of Austempered gray cast iron samples at 240 ℃, 300 ℃ and 360 ℃ and as cast material samples. The wear resistance of Austempered samples of gray cast iron at 240 ℃ and 300 ℃ is obviously better than that of as cast materials, which is related to the highest hardness of Austempered samples. The properties of isothermal quenched samples of gray cast iron at 360 ℃ are still better than those of as cast samples, but much lower than those of isothermal quenched samples of gray cast iron at lower temperatures. Compared with the samples quenched at the other two temperatures, the wear resistance of the samples quenched at 300 ℃ is medium, which further confirms the principle that the hardness is higher due to the refinement of the structure, which will reduce the wear.
Fig. 7 and Fig. 8 show the adhesive wear test results of samples with boride layer. In order to prove that boride layer can effectively improve wear resistance, the wear test results of isothermal quenched samples of gray cast iron are shown in the figure.