Abstract
To achieve lightweight design of automotive bodies, this study focuses on the optimization of aluminum alloy steering knuckles through a combination of topology optimization and squeeze casting. An aluminum alloy steering knuckle solid model was established, and the SIMP (Solid Isotropic Material with Penalization) interpolation model was employed for multi-operating condition topology optimization. The optimized design was then refined considering the forming requirements of squeeze casting. Results indicate that the maximum stress on the aluminum alloy steering knuckle under various operating conditions is significantly lower than the yield limit, resulting in a weight reduction of 60.9% compared to a ductile cast iron steering knuckle. Post T6 heat treatment, the optimized aluminum alloy steering knuckle exhibited excellent mechanical properties, including an average tensile strength of 311.03 MPa, yield strength of 252.13 MPa, and elongation of 7.45%, all surpassing the specified values and meeting product performance requirements.
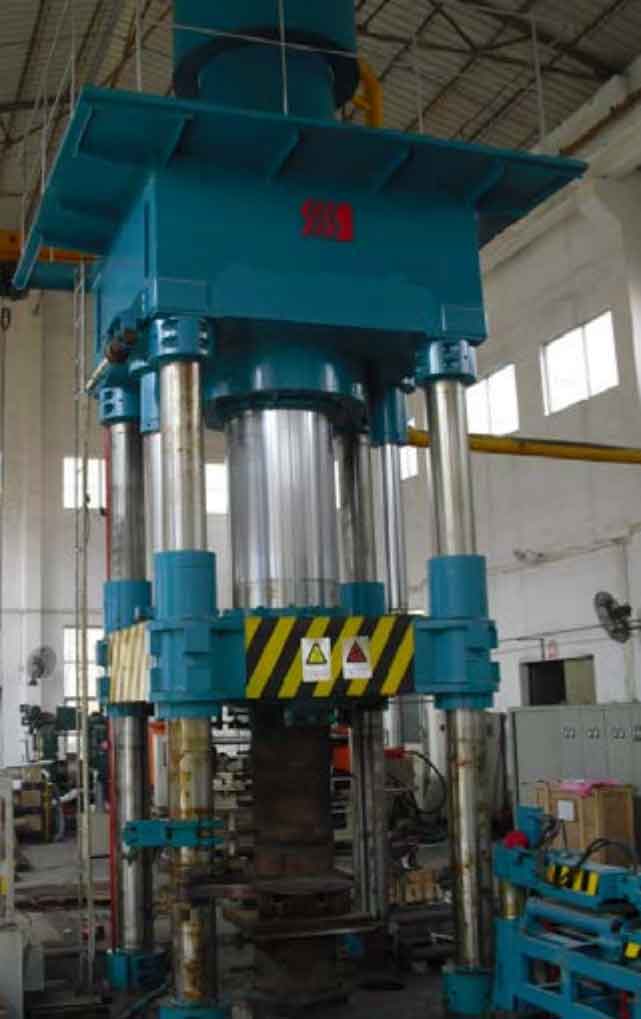
1. Introduction
The steering knuckle, as a critical component of the automotive suspension system, experiences complex and diverse loading conditions during driving. It is essential to ensure high strength and impact resistance to guarantee safe vehicle operation. Traditional steering knuckles are primarily manufactured using ductile cast iron via sand casting, which is relatively heavy. With the growing emphasis on vehicle lightweighting for improved fuel efficiency and reduced emissions, there is a shift towards using lightweight materials such as aluminum alloys.
Squeeze casting, also known as liquid forging, combines the advantages of casting and forging processes. It produces dense, high-quality castings with excellent mechanical properties and dimensional accuracy, making it suitable for high-performance structural components such as automotive steering knuckles. This study integrates topology optimization with squeeze casting to develop an optimized aluminum alloy steering knuckle.
2. Background and Literature Review
2.1 Topology Optimization
Topology optimization is a mathematical method that determines the optimal material distribution within a given design space to meet specific performance criteria while minimizing weight or material usage. It has been widely applied in various engineering fields, including automotive, aerospace, and civil engineering.
Several optimization methods exist, including the Solid Isotropic Material with Penalization (SIMP) method, which is favored due to its computational efficiency and ease of implementation. The SIMP method introduces a density variable for each element in the design domain, where an intermediate density value indicates a mix of solid and void phases. By penalizing intermediate densities, the optimization process converges towards a binary (0-1) solution, where 0 represents void and 1 represents solid material.
2.2 Squeeze Casting
Squeeze casting involves injecting molten metal into a closed die under high pressure, ensuring a more homogeneous microstructure and reduced porosity compared to conventional casting methods. This process results in castings with superior mechanical properties, close dimensional tolerances, and surface finish. Squeeze casting is particularly suitable for high-performance aluminum alloys due to their susceptibility to hot tearing and porosity issues in conventional casting processes.
Previous studies have demonstrated the potential of squeeze casting for automotive components, such as wheel hubs and connecting rods. However, limited research has focused on integrating topology optimization with squeeze casting to further enhance lightweight design and performance.
3. Materials and Methods
3.1 Material Selection
Aluminum alloys were selected for this study due to their lightweight nature, good formability, and corrosion resistance. A specific aluminum alloy grade, tailored for high strength and toughness, was chosen for the steering knuckle.
3.2 Topology Optimization
3.2.1 Mathematical Formulation
The topology optimization problem was formulated as a minimization of structural compliance (i.e., maximizing stiffness) under multiple loading conditions, subject to volume and stress constraints. The mathematical model is expressed as:
begin{align*} text{minimize} \quad & C(\rho) = \sum_{k=1}^{m} \omega_k c_k(\rho) \\ text{subject to} \quad & V(\rho) \leq fV_0, \\ & \sigma_j(\rho) \leq \sigma_0, \quad \forall j, end{align*}
where:
- C(ρ) is the compliance (or objective function),
- ρ is the element density (design variable),
- ck(ρ) is the compliance under the k-th loading condition,
- ωk is the weight factor for the k-th condition (set to 1 for equal importance),
- V(ρ) and V0 are the optimized and initial volumes, respectively,
- f is the volume fraction constraint (set to 0.3),
- σj(ρ) and σ0 are the stress at node j and the allowable stress limit, respectively.
3.2.2 Finite Element Modeling
A three-dimensional finite element model of the existing ductile cast iron steering knuckle was developed using commercial finite element software. The model was then imported into a topology optimization module, where design spaces and constraints were defined. Loading conditions were simulated based on actual driving scenarios, including 4x overload, single-wheel drive over a curb, braking, and acceleration.
The element size was set to 1 mm, and material properties such as Young’s modulus (72.4 GPa) and Poisson’s ratio (0.33) were assigned to the aluminum alloy. Inertia relief was applied to simulate the non-rigid body motion of the steering knuckle during loading.
3.2.3 Optimization Process
The optimization was executed using the SIMP method, with a penalty factor of 3 to enforce a binary material distribution. After 29 iterations, the optimization converged, yielding a new material distribution that significantly reduced weight while maintaining structural integrity.
3.3 Squeeze Casting Process
Based on the optimized topology, a new steering knuckle design was created, considering the specific requirements of the squeeze casting process. Key design features included draft angles, parting lines, and gating systems to facilitate metal flow and ejection from the die.
4. Results and Discussion
4.1 Topology Optimization Results
The optimized topology significantly altered the material distribution, resulting in a more efficient structure. illustrates the optimized topology, with darker regions indicating retained material and lighter regions indicating removed material.
4.2 Structural Design and Squeeze Casting
The optimized topology was refined into a manufacturable design, incorporating features such as draft angles and gating systems. shows the final design ready for squeeze casting.
4.3 Finite Element Analysis
Finite element analysis was performed on the optimized steering knuckle under the same loading conditions used in the optimization phase. displays the stress distributions under various operating conditions, confirming that the maximum stresses are well below the yield strength of the aluminum alloy.
4.4 Mechanical Properties
After T6 heat treatment (540°C for 6 hours, followed by water quenching and aging at 175°C for 4 hours), mechanical property testing was conducted on the optimized steering knuckle. Table 1 summarizes the test results, demonstrating excellent tensile strength, yield strength, and elongation.
Property | Test Result (Average) | Specified Requirement |
---|---|---|
Tensile Strength | 311.03 MPa | ≥ 290 MPa |
Yield Strength | 252.13 MPa | ≥ 220 MPa |
Elongation | 7.45% | ≥ 6% |
Table 1: Mechanical properties of the optimized aluminum alloy steering knuckle.
5. Conclusion
This study successfully integrated topology optimization with squeeze casting to develop a lightweight aluminum alloy steering knuckle. The optimized design significantly reduced weight by 60.9% compared to the original ductile cast iron steering knuckle, while maintaining excellent mechanical properties. Finite element analysis confirmed that the maximum stresses under various operating conditions were well below the yield strength of the aluminum alloy. Post-heat treatment, the steering knuckle exhibited tensile and yield strengths exceeding specified requirements, demonstrating the effectiveness of the combined optimization and manufacturing approach.
Future work could explore further material and process optimization to enhance the performance and cost-effectiveness of the steering knuckle. Additionally, multi-objective optimization frameworks could be employed to balance weight reduction with other critical performance metrics, such as fatigue life and crashworthiness.