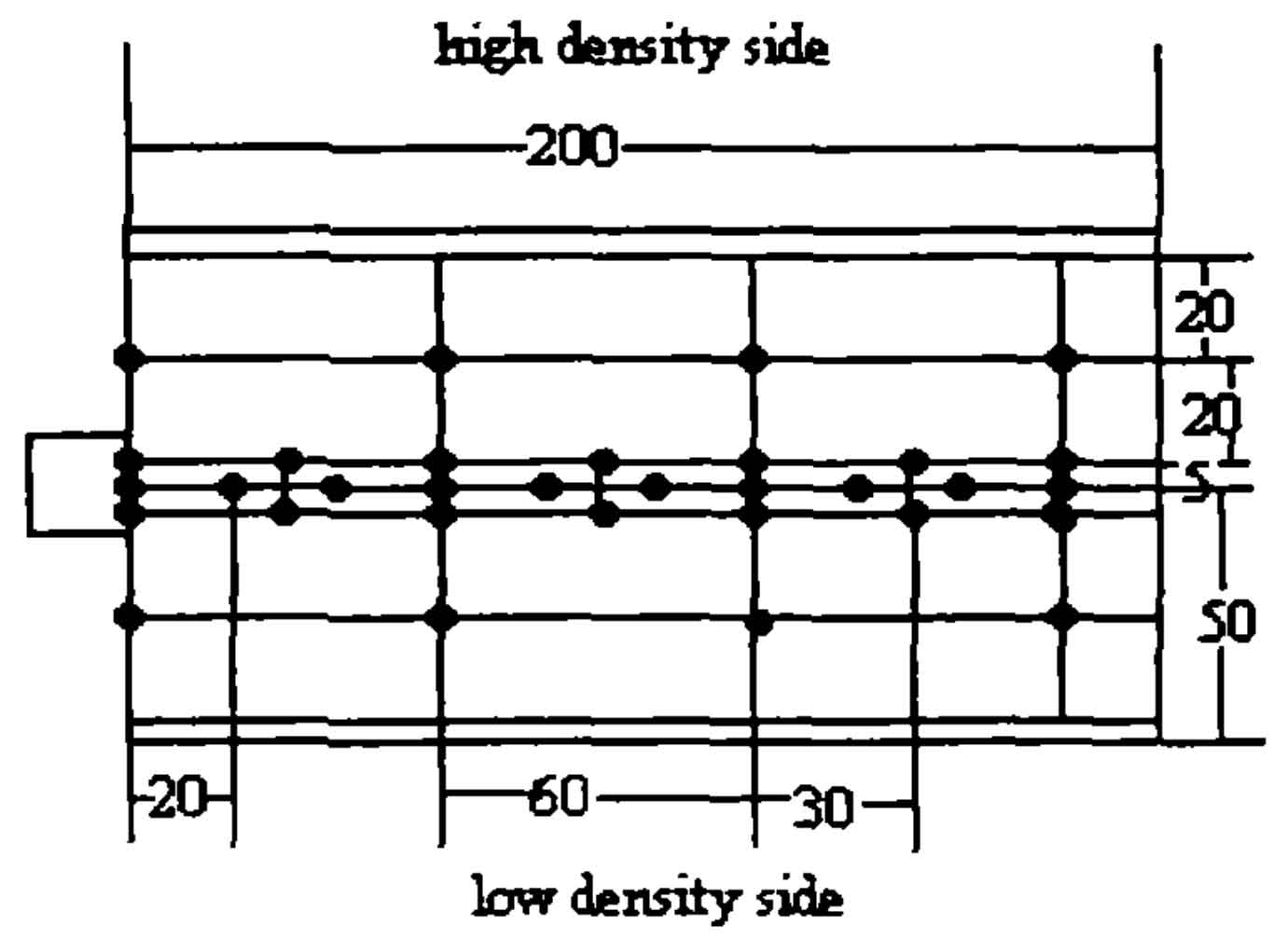
The model shown in Fig. 1 is made of two models with the same size and different density bonded by hot melt adhesive. The densities of the two models are 9g / I and 13.2g/i respectively. The geometric dimension of the model after bonding is 200mmx100mm x20mm. The model is placed horizontally in the sand box and the internal runner is introduced at the bonding position. See Fig. 2 for the filling form of molten metal.
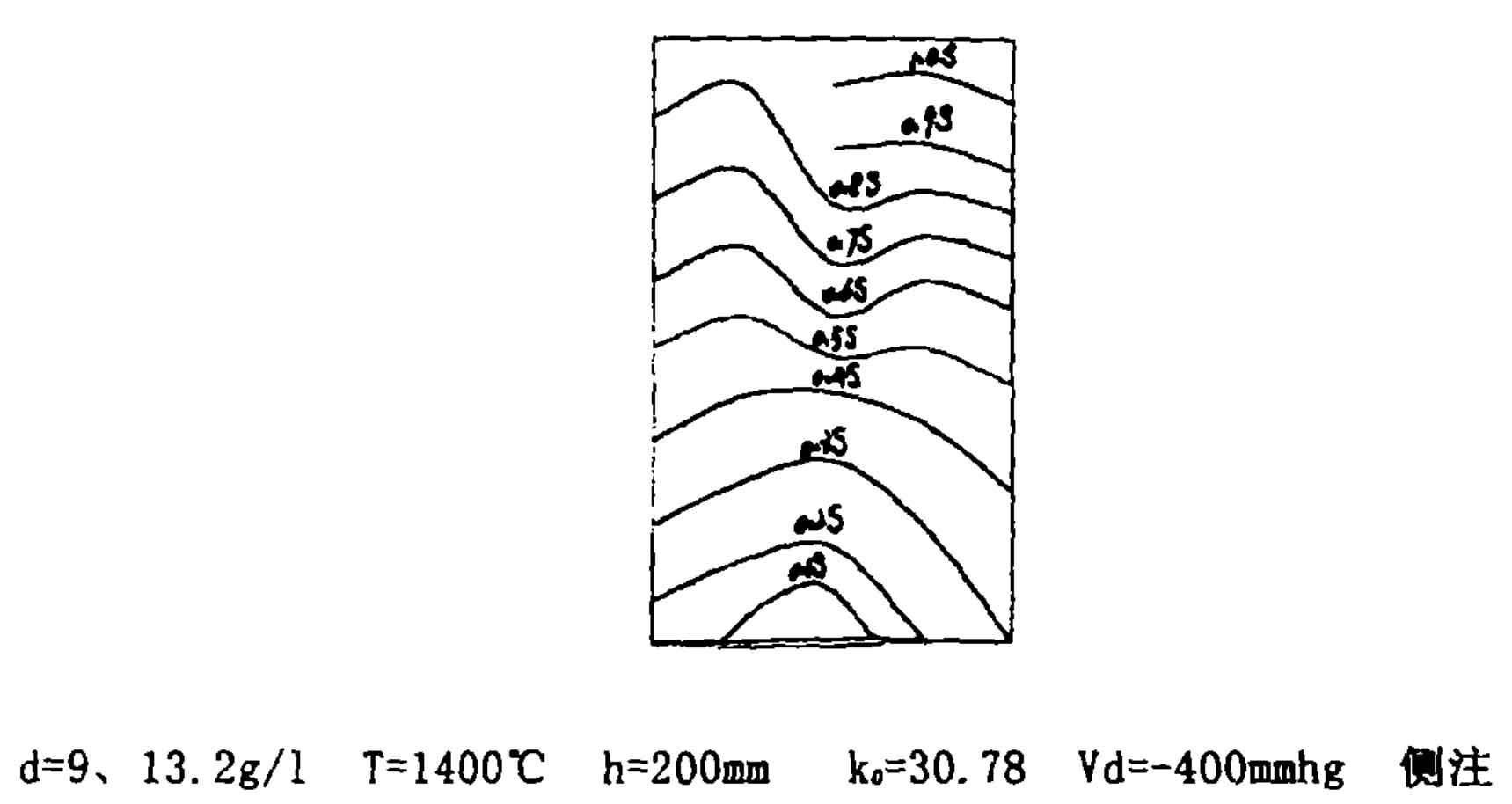
It can be seen from the figure that two different radial arc-shaped curves are formed on both sides of the center line after the molten metal of lost foam casting enters the model from the inner gate. The density of the isochronous curve is different. On the side of the high-density model, the isochronous curve is dense, and the filling speed of the molten metal is slow. On the side of the low-density model, the isochronous curve is sparse, and the filling speed of the molten metal of lost foam casting is fast. At the initial stage of filling, the front of the flowing metal is convex, and the intersection of the two radial arcs is at the center of the model. With the filling process, the filling speed of the edge of the model is faster, while the filling speed of the molten metal at the center is slower. The front of the flowing metal is concave, the edge of the model is filled first, and the middle part is filled last. The filling time of the molten metal at the high density side and the low density side is 0.74s and 0.96s respectively.
During the filling process of molten metal in lost foam casting, under the action of vacuum and negative pressure, the molten metal will produce wall attachment effect, and the filling speed at the edge of the model tends to be higher than that at the middle part. The central part of the model is bonded with hot melt adhesive, and the presence of hot melt adhesive affects the filling characteristics of molten metal. Although the hot melt adhesive is organic, the density of the hot melt adhesive is much higher than that of the pattern material. Even if a small amount of hot melt adhesive is used, the weight of the pattern will be significantly increased. The vaporization and decomposition of hot melt adhesive is also an endothermic process, which needs to absorb a large amount of heat from the molten metal to form an influence area of hot melt adhesive at the central bonding part. The vaporization disappearance time of the model increases, the filling speed of the molten metal slows down, and the front edge of the molten metal is concave. At the same time, the existence of a large number of decomposition products increases the possibility of forming casting defects such as pores, cold shuts and wrinkles, Therefore, in the process of lost foam casting model combination, the amount of hot melt adhesive should be reduced as much as possible under the condition of ensuring the adhesive strength.