Lost foam casting is known for its cost-effectiveness, especially when it comes to the production of complex metal components. Here’s how lost foam casting offers a cost-effective solution for complex metal fabrication:
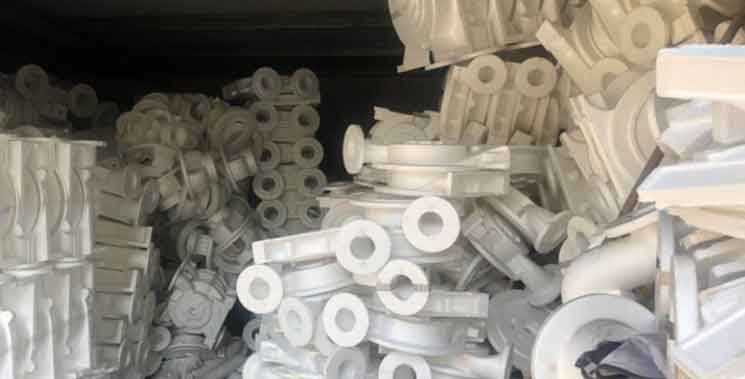
1. Reduced Tooling Costs:
Lost foam casting requires less complex tooling compared to other casting methods. The foam patterns used in the process are relatively inexpensive to produce and can be easily modified or replaced. This reduces the initial tooling costs and allows for more cost-effective design changes or iterations during the production process.
2. Elimination of Cores and Assembly Operations:
Lost foam casting eliminates the need for separate cores and assembly operations. The foam pattern serves as both the pattern and the core, resulting in a single-piece mold. This eliminates the cost associated with producing, handling, and aligning multiple core segments. It also reduces the time and labor required for assembly, resulting in cost savings.
3. Near-Net Shape Casting:
Lost foam casting produces near-net shape castings, which means that the final components require minimal post-casting machining or finishing. The foam patterns accurately reproduce the desired shape, reducing the material that needs to be removed during machining. This minimizes material waste and lowers the costs associated with machining operations.
4. Improved Production Efficiency:
Lost foam casting streamlines the production process and improves overall efficiency. The simplified tooling, elimination of cores, and reduced machining requirements result in shorter production cycles. This allows for faster turnaround times, increased production capacity, and reduced labor costs.
5. Design Optimization and Integration:
Lost foam casting allows for complex design optimization and integration of features. The foam patterns can be easily shaped and molded to incorporate intricate details, undercuts, and internal features without the need for separate cores or assembly operations. This eliminates the costs associated with additional parts or processes required for achieving complex designs.
6. Material Savings:
Lost foam casting minimizes material waste during the production process. The near-net shape capability of the process reduces the amount of material that needs to be machined or discarded. This results in material savings and cost reductions, making it a cost-effective solution for complex metal fabrication.
7. Single-Piece Castings:
Lost foam casting enables the production of complex components as single-piece castings. This eliminates the need for joining or welding multiple parts together, reducing labor costs and potential weak points in the final product. Single-piece castings also reduce the risk of component failure, ensuring long-term cost savings through improved reliability.
8. Versatility with Material Selection:
Lost foam casting is compatible with a wide range of metals and alloys, offering versatility in material selection. Manufacturers can choose the most suitable material based on performance requirements, cost considerations, and industry standards. This flexibility allows for cost-effective solutions tailored to specific applications.
Lost foam casting’s reduced tooling costs, elimination of cores and assembly operations, near-net shape casting, improved production efficiency, design optimization, material savings, single-piece castings, and material versatility contribute to its cost-effectiveness in complex metal fabrication. It provides an economical solution for producing high-quality, intricate components while minimizing waste and optimizing production processes.