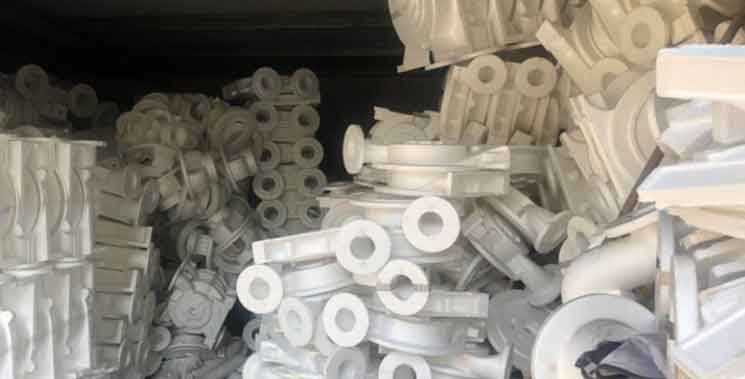
Lost foam casting is indeed a revolutionary method for precise metal component production. It offers numerous advantages and has gained popularity in various industries. Lost foam casting, also known as evaporative pattern casting, involves creating a foam pattern that is coated with refractory material and then placed in a mold. The molten metal is poured into the mold, which vaporizes the foam pattern, leaving behind the metal component.
Here are some key aspects that make lost foam casting a revolutionary method:
- Complex Geometries: Lost foam casting enables the production of complex geometries that may be difficult or costly to achieve with other casting methods. The foam patterns can be easily shaped and manipulated to create intricate and detailed features in the final metal component, including thin walls, internal cavities, and intricate shapes.
- Dimensional Accuracy: Lost foam casting offers excellent dimensional accuracy. The foam patterns can be precisely manufactured using computer-aided design (CAD) and computer-aided manufacturing (CAM) technologies, ensuring that the final cast component closely matches the intended design. The absence of parting lines and cores eliminates the potential for mismatch or misalignment, resulting in highly accurate and near-net-shape components.
- Reduced Tooling Costs: Lost foam casting eliminates the need for complex and expensive molds and cores, reducing tooling costs. The foam patterns can be easily and cost-effectively produced using molds or 3D printing techniques, reducing the initial investment required compared to traditional tooling methods. This makes lost foam casting a viable option for small to medium-scale production runs and prototypes.
- Design Freedom: Lost foam casting offers design freedom and flexibility. Since the foam patterns are easily moldable, designers have more freedom to create intricate shapes, thin sections, and internal features. This allows for innovation and the realization of complex design concepts that would be challenging with other casting methods.
- Minimal Post-Casting Operations: Lost foam casting produces near-net-shape components with excellent surface finish, reducing the need for extensive post-casting operations. The elimination of cores and parting lines eliminates the need for core removal and minimizes the need for machining or other finishing processes. This saves time and cost in the overall production process.
- Material Variety: Lost foam casting can be performed with a wide range of metals and alloys, including aluminum, iron, and steel. This versatility allows for the production of components with specific material properties, such as strength, corrosion resistance, or heat resistance, to meet the requirements of various industries and applications.
- Environmental Sustainability: Lost foam casting is considered a more environmentally friendly casting method compared to traditional techniques. The foam patterns used in the process are made from expandable polystyrene (EPS), which can be recycled or even reused. The absence of binders and the reduced need for core production contribute to lower emissions and waste generation.
Lost foam casting has revolutionized metal component production by offering designers and manufacturers greater design freedom, cost-effectiveness, and precision. Its ability to create complex and accurate components with minimal post-casting operations has made it a preferred choice in industries such as automotive, aerospace, and machinery manufacturing. As technology continues to advance, lost foam casting is likely to further evolve, providing even more opportunities for innovative and efficient metal component production.