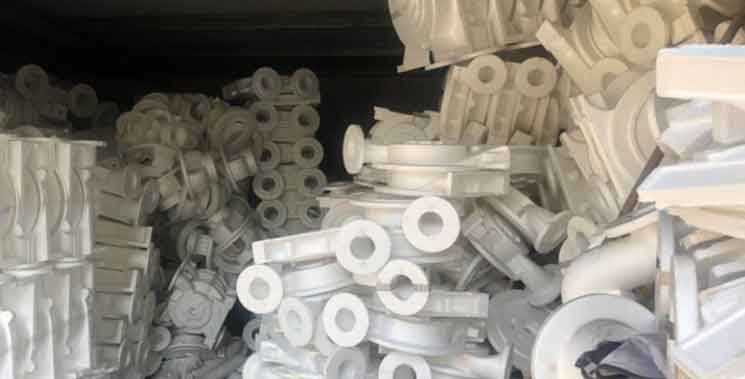
Lost foam casting is indeed a sustainable approach to metal component manufacturing that offers several advantages over traditional casting methods. It is a casting process that involves creating a foam pattern in the shape of the desired metal component, coating it with refractory material, and then pouring molten metal into the mold. The foam pattern vaporizes upon contact with the molten metal, leaving behind a cavity that is filled with the metal, resulting in the desired component.
Here are some reasons why lost foam casting is considered a sustainable approach:
1.Material Efficiency:
Lost foam casting eliminates the need for traditional pattern materials like wood or plastic, which are typically used in other casting processes. Foam patterns used in lost foam casting can be made from expanded polystyrene (EPS) or other similar materials, which are easily recyclable. This reduces material waste and promotes resource conservation.
2.Energy Efficiency:
Lost foam casting requires lower energy consumption compared to other casting methods. The foam pattern is easily vaporized by the heat of the molten metal, eliminating the need for a separate pattern removal step. This reduces the energy requirements for pattern removal and results in overall energy savings.
3.Reduced Emissions:
Since lost foam casting does not involve the use of binders or core materials, it significantly reduces the emissions of volatile organic compounds (VOCs) associated with traditional casting processes. This makes it a cleaner and more environmentally friendly manufacturing method.
4.Design Flexibility:
Lost foam casting allows for intricate and complex shapes to be produced with relative ease. The foam patterns can be easily manipulated and shaped, enabling the creation of intricate details and undercuts in the final metal component. This design flexibility reduces the need for secondary machining operations, further minimizing material waste and energy consumption.
5.Process Integration:
Lost foam casting can integrate multiple components into a single casting, eliminating the need for separate manufacturing and assembly steps. By consolidating parts into a single casting, material waste is reduced, and the overall manufacturing process becomes more streamlined and efficient.
6.Recycling and Reusability:
The foam patterns used in lost foam casting can be easily recycled and reused. Any excess or scrap foam can be recycled back into new foam patterns, minimizing waste generation and promoting a closed-loop system.
Overall, lost foam casting offers a sustainable alternative to traditional casting methods by reducing material waste, energy consumption, emissions, and promoting recycling and reusability. Its advantages make it an attractive option for manufacturers looking to optimize their processes while minimizing their environmental impact.