Lost foam casting (LFC) continues to advance and evolve in the manufacturing industry, driven by technological innovations, industry demands, and environmental considerations. Several key advancements and trends are shaping the future of lost foam casting:
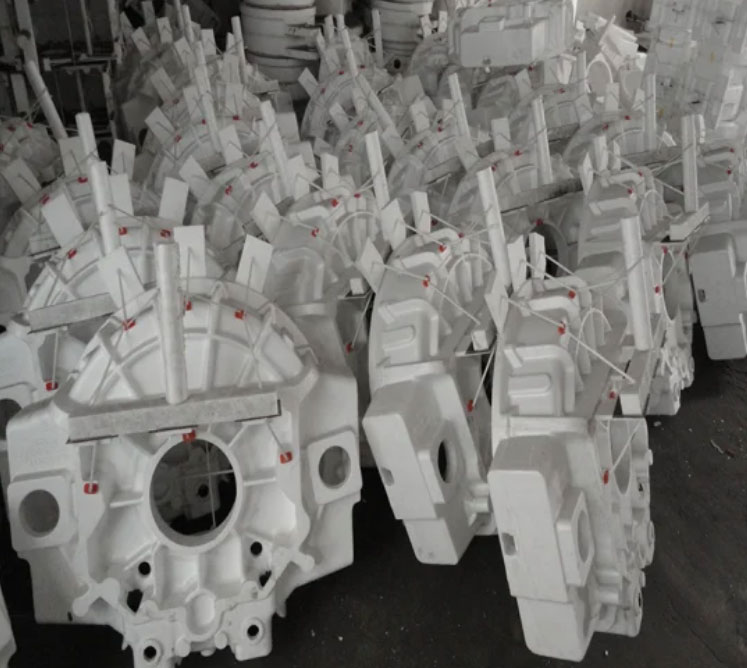
1. Integration of Additive Manufacturing:
The integration of additive manufacturing (3D printing) with lost foam casting is an emerging trend. 3D printing is used to create precise foam patterns directly or to produce complex sand molds for the casting process. This integration enhances design freedom, reduces lead times, and enables rapid prototyping and production of intricate parts.
2. Sustainable and Eco-Friendly Practices:
As environmental concerns become more prominent, lost foam casting is embracing sustainable practices. Manufacturers are exploring greener materials, eco-friendly binders, and energy-efficient technologies to reduce the environmental impact of the casting process.
3. Digitalization and Simulation:
Digitalization is playing a significant role in lost foam casting advancements. Advanced simulation tools, such as finite element analysis (FEA) and computational fluid dynamics (CFD), are used to optimize casting processes, predict defects, and improve casting quality. Virtual prototyping enables designers and engineers to validate designs before physical casting, reducing the number of iterations required.
4. Automation and Robotics:
Automation and robotics are increasingly integrated into lost foam casting foundries. Automated pouring systems, robotic handling of foam patterns and castings, and smart manufacturing practices enhance productivity, reduce labor requirements, and improve safety in the production process.
5. Multi-Material Castings:
Lost foam casting is being used to create multi-material castings with varying properties in different regions of the component. This capability allows for the production of hybrid components with optimized properties for specific applications.
6. Industry 4.0 and Data Analytics:
Foundries are adopting Industry 4.0 principles, utilizing data analytics and real-time monitoring to optimize processes, predict maintenance needs, and maximize overall efficiency. Data-driven decision-making enables continuous improvement in the casting process.
7. High-Performance Materials:
Lost foam casting is expanding its application to high-performance materials and alloys. These materials offer improved mechanical properties, temperature resistance, and corrosion resistance, making them suitable for critical applications in aerospace, automotive, and other industries.
8. Increased Adoption in Aerospace and Automotive Industries:
The aerospace and automotive industries are increasingly adopting lost foam casting due to its ability to produce complex, lightweight, and high-precision components. The process aligns well with the demand for improved fuel efficiency, reduced emissions, and enhanced performance in these sectors.
9. Design Optimization for Lightweighting:
Lost foam casting enables intricate and lightweight designs, contributing to the ongoing trend of lightweighting in various industries. Components designed for reduced weight while maintaining structural integrity lead to improved energy efficiency and performance.
10. Rapid Prototyping and Customization:
Lost foam casting’s ability to produce near-net-shape parts and rapidly create foam patterns allows for faster prototyping and customization of castings. This is particularly beneficial in industries with short product development cycles and unique requirements.
Lost foam casting is experiencing significant advancements and trends in the manufacturing industry. The integration of additive manufacturing, sustainable practices, digitalization, automation, and multi-material capabilities are transforming the lost foam casting process, making it more versatile, efficient, and environmentally friendly. As technology continues to progress, lost foam casting will remain a key player in the production of complex and lightweight components across various industrial sectors.