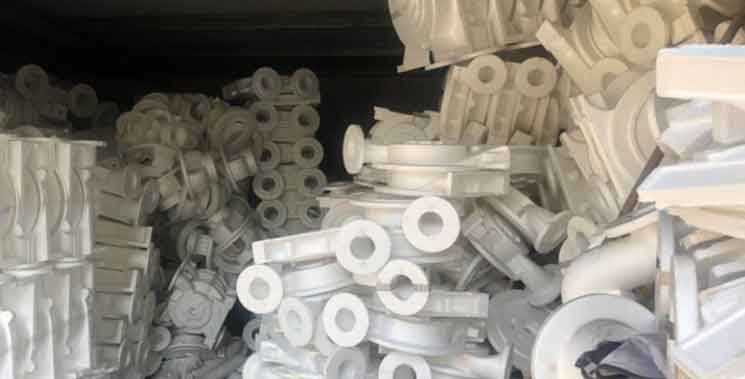
Lost foam casting, also known as evaporative pattern casting or full mold casting, is an innovative approach to precision metal casting. It involves creating a foam pattern that is coated with a refractory material, which is then buried in sand. When molten metal is poured into the mold, the foam pattern vaporizes due to the heat of the metal, leaving behind a cavity in the shape of the desired casting. Lost foam casting offers several advantages, making it a popular choice for certain applications. Here are some key features and benefits of lost foam casting:
1. Design Flexibility:
- Lost foam casting allows for intricate and complex designs that are difficult or impossible to achieve with traditional casting methods. The foam patterns can be easily shaped and manipulated, providing greater design freedom.
2. Near Net Shape Casting:
- Lost foam casting produces near net shape castings, which reduces the need for additional machining or finishing operations. This results in material and cost savings.
3. Smooth Surface Finish:
- Lost foam castings typically have a smooth surface finish, reducing the need for surface treatments or polishing.
4. Dimensional Accuracy:
- Lost foam casting offers high dimensional accuracy, as the foam pattern maintains its shape during the casting process, resulting in precise and consistent castings.
5. Reduction in Tooling Costs:
- Lost foam casting eliminates the need for complex and expensive dies or patterns used in other casting methods, reducing tooling costs.
6. Reduction in Material Waste:
- The foam pattern used in lost foam casting is expendable and can be easily recycled, minimizing material waste and promoting sustainable practices.
7. Increased Productivity:
- Lost foam casting can be a more rapid and efficient process compared to traditional casting methods, leading to increased productivity and shorter lead times.
8. Complexity of Assemblies:
- Lost foam casting allows for the integration of multiple components into a single casting, reducing the need for assembly processes and potential points of failure.
9. Wide Range of Materials:
- Lost foam casting can be used for a variety of metals and alloys, making it suitable for diverse industrial applications.
However, lost foam casting also has some limitations and challenges:
- Limited Size: Lost foam casting is best suited for small to medium-sized castings due to the size limitations of the foam patterns.
- Pattern Degradation: The foam patterns are susceptible to damage during handling, transportation, and assembly, which can affect casting quality.
- Equipment and Expertise: Lost foam casting requires specialized equipment and expertise, which may not be readily available in all foundries.
Despite these challenges, lost foam casting continues to gain popularity in various industries, such as automotive, aerospace, and marine, where precision, complexity, and cost-effectiveness are essential considerations. The ongoing advancements in casting technologies are expected to further improve the capabilities and cost-effectiveness of lost foam casting in the future.