Lost foam casting is a casting method that bridges the gap between prototyping and production, offering several benefits for both stages of the manufacturing process. Here’s how lost foam casting facilitates the transition from prototyping to production:
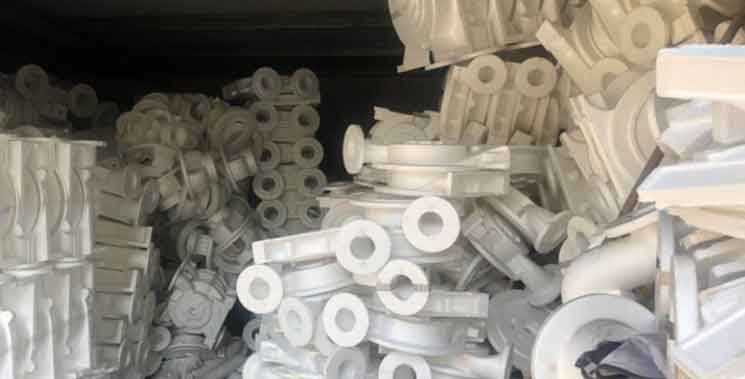
- Rapid Prototyping: Lost foam casting allows for the rapid production of complex prototypes with intricate geometries and fine details. Foam patterns can be easily and quickly fabricated using CAD models, eliminating the need for expensive and time-consuming tooling. This enables faster design iterations and concept validation during the prototyping stage.
- Design Validation: Lost foam casting provides an accurate representation of the final casting during the prototyping phase. The foam patterns used in lost foam casting closely replicate the shape and features of the desired part, allowing engineers to assess the form, fit, and function of the component before proceeding to production. This helps identify any design flaws or areas for improvement early on, reducing the risk of costly modifications during the production phase.
- Cost Efficiency: Lost foam casting offers cost advantages during prototyping. Since the foam patterns can be easily modified or replaced, it enables the production of multiple design iterations without incurring significant expenses for tooling changes. This flexibility allows for cost-effective prototyping and design optimization.
- Smooth Transition to Production: Lost foam casting facilitates a smooth transition from prototyping to production. The same foam patterns used in the prototyping phase can be scaled up for larger-scale production, eliminating the need for new tooling or pattern modifications. This streamlines the production process, reduces lead time, and ensures consistency between the prototype and the final production component.
- Complex Geometry Replication: Lost foam casting excels in replicating intricate and complex geometries, making it suitable for components with challenging shapes or internal features. This capability ensures that the prototypes accurately represent the intended design, allowing engineers to assess the performance and feasibility of the component under real-world conditions.
- Material Selection: Lost foam casting accommodates a wide range of materials, including ferrous and non-ferrous alloys, enabling the use of production-grade materials during prototyping. This provides a more accurate assessment of the mechanical properties and performance of the prototype, ensuring that it aligns with the intended production material.
- Process Optimization: The experience gained during the prototyping phase using lost foam casting can be utilized to optimize the production process. Lessons learned, design improvements, and process enhancements from prototyping can be incorporated into the production workflow, resulting in higher efficiency and improved quality in the final components.
By offering rapid prototyping, design validation, cost efficiency, smooth transition to production, complex geometry replication, material flexibility, and process optimization, lost foam casting serves as a valuable bridge between the prototyping and production stages. It accelerates the product development cycle, reduces costs, and ensures that the final production components meet the desired specifications and performance requirements.