Lost foam casting molding is completed by model disappearance, decomposition products escaping from the mold, and liquid metal replacement model. The pattern material determines the quantity and type of decomposition products, while lost foam casting coating determines the escape speed and mode of decomposition products. Extensive research shows that lost foam casting coating plays a decisive role in the success of the process. The functions of lost foam casting coating include preventing the surface of the pattern from being damaged due to sand flow friction during molding, increasing the rigidity of the pattern, preventing the deformation of the model during molding, isolating the liquid metal and dry sand, preventing the infiltration and sand sticking of liquid metal, maintaining the stability of the mold, supporting dry sand, and preventing the box from collapsing.
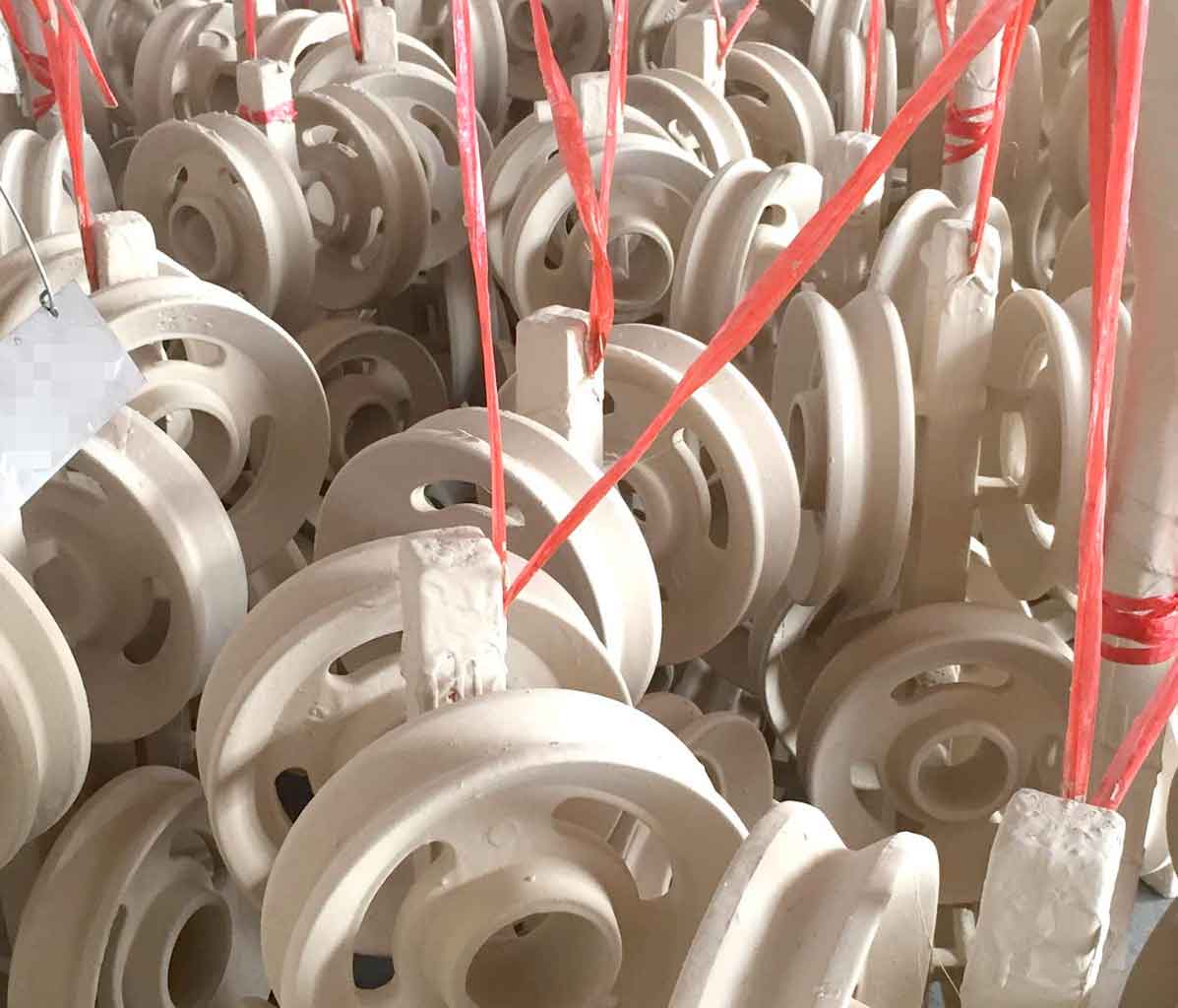
In lost foam casting, coating should meet the following conditions:
- Convenient coating;
- No cracks during drying;
- The molding will not be damaged when filling sand;
- It can prevent the stress on the model caused by the compaction of molding sand and should have sufficient mechanical strength to protect the surface of the model;
- It can withstand the thermal shock and pressure of molten metal during pouring;
- No infiltration;
- The thermal decomposition products of EPS model do not stay in the model cavity and have good air permeability;
- Good separation;
The mechanical strength and permeability of lost foam casting coating are the most important. The so-called mechanical strength refers to the ability to resist the deformation of the model during modeling, and the permeability refers to the difficulty of the thermal decomposition products of the model escaping from the coating during lost foam casting.
The surface of the foam plastic mold is hydrophobic, and its affinity and water absorption to the lost foam casting water-based coating are poor. Therefore, the lost foam casting coating needs to have good wettability to the pattern and strong coverage ability. When coating, it can get a complete, uniform and sufficient thickness coating, and can accurately copy the surface and size of complex mold samples.
In the pouring process, the coating is required to have good high temperature crack resistance. The coating is not easy to crack after being subjected to the rapid heating effect of liquid metal, and can withstand the impact and isolation effect of high-temperature liquid metal, so as to ensure the mechanical strength of castings and prevent chemical sand sticking defects.