1. Introduction
Lost foam casting has witnessed remarkable growth in recent years, attributed to its numerous advantages such as low pollution levels, high flexibility in the manufacturing process, reduced labor intensity, and excellent repeatability. This technology has found extensive applications, especially in the production of box – shaped and shell – like components. However, during the casting process of products like flywheel housings, various defects frequently occur, including sand adhesion, porosity, and sand wash. These defects not only compromise the quality of the castings but also lead to increased production costs and waste. Therefore, it is of great significance to conduct in – depth research on these defects to improve the quality of lost foam castings.
2. Sand Adhesion Defects in Flywheel Housings
2.1 Causes of Sand Adhesion
Sand adhesion is a defect where the molten metal bonds with the molding sand on the surface of the casting during the pouring process. For flywheel housing castings, improper placement methods, structural designs, or process designs can result in the inability to compact the mold cluster in the sand box, thereby causing sand adhesion.
Take the 9661 flywheel housing as an example. Its material is HT250, with a mass of approximately 22 kg, and outline dimensions of 440 mm×440 mm×220 mm, and a product wall thickness of 5 mm. The existing process has an inner gate size of 50 mm (length)×30 mm (height)×6 mm (width), with the molten iron tapping temperature ranging from 1460 – 1470 °C (using an electric furnace as the melting equipment), the pouring temperature from 1430 – 1440 °C, a vacuum degree of – 0.025 MPa, without film covering and pressure maintaining. The main defect is the sand inclusion on the top of the inner cavity of the flywheel housing, with a scrap rate of 20%.
The current process places the motor hole at the bottom. The top of the inner cavity of this product often suffers from sand adhesion issues. This is because the top – angle is greater than 90°, causing the molding sand to be unable to fill and compact the mold cluster during the vibration process. As a result, the molding sand at the top is loose, and during the filling process of the molten iron, local molten metal adheres to the molding sand, generating sand adhesion. The 9661 flywheel housing’s sand adhesion is characterized by the mechanical mixture of sand grains and metal adhering to the shell surface. When cleaned, the surface shows a metallic luster, which is a typical feature of mechanical sand adhesion. The main influencing factors include the compactness of the molding sand during molding, the refractoriness of the coating, the pouring temperature, and the coating thickness. Since only the top of the casting has sand adhesion and the rest of the flywheel housing is normal, the issue is likely related to the compactness of the molding sand. The reasons are as follows: ① Insufficient molding sand can be filled at the top of the flywheel housing, or the existing molding sand cannot be compacted; ② The gap between two flywheel housings is too small, resulting in weak molding sand strength.
Influence Factor | Impact on Sand Adhesion |
---|---|
Molding Sand Compactness | Low compactness leads to loose sand, facilitating metal – sand adhesion |
Coating Refractoriness | Insufficient refractoriness may cause the coating to be damaged by high – temperature molten metal, increasing the likelihood of sand adhesion |
Pouring Temperature | High pouring temperature can intensify the interaction between molten metal and sand, promoting sand adhesion |
Coating Thickness | Unreasonable coating thickness can affect the gas – permeability and protection of the coating, related to sand adhesion |
2.2 Control Measures for Sand Adhesion
In response to the generation mechanism of casting sand adhesion and its influencing factors, the following measures are mainly adopted: (1) Adjust the placement method of the white mold according to the product structure. Place the motor hole of the flywheel housing upwards to facilitate the filling of molding sand and ensure that there is sufficient molding sand at the top of the flywheel housing. (2) Increase the distance between two flywheel housings. Change the original distance of 80 mm to 120 mm to ensure an adequate gap between the two mold clusters, thereby guaranteeing the compactness of the molding sand.
2.3 Production Verification of Sand Adhesion Control
After analyzing the reasons for the compactness problem of the flywheel housing molding sand and making two improvements to the existing combination process, namely the product placement method and the combination spacing, production verification was carried out from small – batch to large – batch production. During the normal production process, with the premise that variable factors such as the dip – coating process, pouring temperature, and vacuum pumping remained unchanged, the sand adhesion defect rate dropped to 0. Through these measures, the goal of completely solving the sand adhesion defect at the top of the flywheel housing was achieved.
3. Porosity Defects in Flywheel Housings
3.1 Causes of Porosity
When the molten iron enters the mold cluster, the white mold gasifies and decomposes, generating a large amount of gas and residues. If these substances cannot be discharged from the casting body in a timely manner, pores will form on the surface of the casting. The occurrence of pores is related to factors such as the pouring temperature, the gas – permeability of the coating, and the pouring speed.
For the SAIC Maxus flywheel housing, with the molten iron tapping temperature of 1460 – 1470 °C (using an electric furnace as the melting equipment), the pouring temperature of 1430 – 1440 °C, a vacuum degree of – 0.025 MPa, without film covering and pressure maintaining, the main defect is the pores in the motor hole at the top of the product, with a scrap rate of 30%.
This pore defect is characterized by normal appearance detection on the surface or near – surface of the casting, but there are smooth holes of different sizes on the surface after processing, and the pore walls have an oxidized luster. The pores are mainly concentrated at the top of the product, which is a typical feature of subcutaneous pores. The main influencing factors are as follows: ① Pouring temperature: When the pouring temperature is low, the foam does not burn completely, and the gas cannot be completely discharged, forming pores under the skin; ② Local coating thickness: If the coating thickness at the motor hole is too thick, the gas generated after the foam burns cannot be discharged, resulting in pores; ③ Vacuum degree: Insufficient vacuum pumping means that the gas cannot be evacuated in time, forming pores; ④ Unreasonable process design: The lack of exhaust ports at the top of the flywheel housing causes the gas to accumulate at the top of the body and not be completely discharged, forming pores.
Influence Factor | Impact on Porosity |
---|---|
Pouring Temperature | Low temperature leads to incomplete foam combustion and gas entrapment |
Local Coating Thickness | Thick coating restricts gas escape, increasing the chance of pore formation |
Vacuum Degree | Insufficient vacuum cannot effectively remove gas, causing pores |
Process Design (Lack of Exhaust Ports) | Gas accumulation due to poor exhaust design results in pore formation |
3.2 Control Measures for Porosity
In view of the generation mechanism of casting pores and their influencing factors, the following measures are mainly taken: (1) Increase the pouring temperature from 1430 – 1440 °C to 1450 – 1460 °C, and conduct 10 sets of pourings. (2) Reduce the coating thickness at this position from 2.0 mm to 0.5 mm, and conduct 10 sets of pourings. (3) Increase the vacuum degree from – 0.025 MPa to – 0.045 MPa, and conduct 10 sets of pourings. (4) Add an exhaust piece at the motor hole with dimensions of 50 mm (length)×30 mm (height)×5 mm (width), and conduct 10 sets of pourings.
3.3 Production Verification of Porosity Control
After analyzing the reasons for the pores in the flywheel housing and making four improvements to the existing process parameters, namely the product pouring temperature, coating thickness, pouring vacuum degree, and adding an exhaust piece, a process test was carried out. By using the control variable method, different improvement measures were tested separately. Among them, Plan 1 was to increase the pouring temperature, with 20 pieces produced and processed, 4 of which had pores, and the proportion of pores in the motor hole was 20%; Plan 2 was to reduce the coating thickness, with 20 pieces produced and processed, 5 of which had pores, and the proportion of pores in the motor hole was 25%; Plan 3 was to increase the vacuum degree, with 20 pieces produced and processed, 3 of which had pores, and the proportion of pores in the motor hole was 15%; Plan 4 was to add an exhaust piece, with 20 pieces produced and processed, and no pores were found, and the proportion of pores in the motor hole was 0%. Through testing, Plan 4 showed the best result. Subsequent small – batch to large – batch verification also indicated normal processing. Through these measures, the goal of completely solving the pores in the motor hole was achieved.
4. Sand Wash Defects in Connecting Rod Rests
4.1 Causes of Sand Wash
During the pouring process, if the pouring system of the mold cluster, such as the sprue, runner, and ingate, is not completely closed, especially the sprue, siphoning is likely to occur, resulting in sand wash defects. In addition, an unreasonable product pouring system design can cause poor mold filling, high local pressure in the ingate, and the rupture of the coating due to the scouring of the molten iron, which can also lead to sand wash defects as the molding sand enters the mold cavity with the molten iron.
For the connecting rod rest casting, its material is HT200, with a mass of approximately 50 kg, outline dimensions of 572 mm×380 mm×348 mm, and a bottom plate thickness of 12 mm. The existing process introduces molten iron through 3 – point side ingates, with the ingate size of 60 mm×30 mm×6 mm. The process parameters include the molten iron tapping temperature of 1460 – 1470 °C (using an electric furnace as the melting equipment), the pouring temperature of 1430 – 1440 °C, a vacuum degree of – 0.03 MPa, without film covering and pressure maintaining. The main defect is sand wash, which is concentrated near the bottom ingate, with a scrap rate of 20%.
The sand wash defect is located at the bottom of the mold cavity along the straight line of the gate and the part of the mold cavity where the molten iron from the ingate flows in. The appearance of lumps composed of a mixture of sand and metal at this position is a typical feature of sand wash. The main influencing factors are as follows: ① Low coating strength of the ingate, resulting in coating rupture due to the scouring of the molten iron; ② High pressure in the ingate, leading to coating rupture; ③ During the pouring process, severe back – spraying of the molten iron causes coating rupture. However, since the molten iron pouring of this product is stable without back – spraying, the first two factors are mainly considered.
Influence Factor | Impact on Sand Wash |
---|---|
Ingate Coating Strength | Weak coating is easily damaged by molten iron scouring, causing sand wash |
Ingate Pressure | High pressure can break the coating, allowing sand to enter the mold cavity |
Molten Iron Back – spraying | Severe back – spraying can damage the coating, contributing to sand wash |
4.2 Control Measures for Sand Wash
According to the generation mechanism of casting sand wash and its influencing factors, the following measures are mainly adopted: (1) The existing process involves dipping the coating twice with a thickness of 1.5 mm. Add one more dipping process for the ingate to increase the coating thickness to 2.2 mm. (2) Increase the number of ingates. Add another ingate with the same size at the bottom.
4.3 Production Verification of Sand Wash Control
After analyzing the reasons for the sand wash in the connecting rod rest and making two improvements to the existing process parameters, namely the coating thickness of the water inlet and the number of water inlets, a production verification was carried out from small – batch to large – batch production while keeping the influencing parameters such as the pouring temperature and vacuum degree unchanged. Plan 1 was to add one more dipping of the coating on the ingate. 50 pieces were produced, and 6 of them had sand wash, with a proportion of 12%. Plan 2 was to add 1 ingate at the bottom. 50 pieces were produced, and no sand wash occurred. After verification, Plan 2 was the best. Subsequent small – batch to large – batch verification also showed normal processing. The optimized process with 3 ingates at the bottom can play a role in shunting and reducing pressure. There is 1 ingate at the top, and the cross – sectional area of a single ingate is 60 mm×8 mm. The ratio of the sprue area (a 50 – mm – diameter round pipe): runner area (50 mm×40 mm): ingate area is approximately \(1960 ~mm^{2}: 2000 ~mm^{2}: 1920 ~mm^{2}\), basically meeting the 1∶1∶1 condition, achieving the goal of completely solving the sand wash defect of the connecting rod rest.
5. Conclusion
In the process of developing new products, it is necessary to skillfully avoid casting defects through reasonable process design based on the causes of these defects. During the process of process verification, the number of product verifications should be gradually increased from small – batch to large – batch production to avoid significant losses caused by insufficient consideration. In the process verification, it is essential to advance step by step from five major aspects, including understanding the current situation, analyzing the causes, formulating plans, implementing countermeasures, and confirming the effects, so as to ultimately achieve the goal of completely solving the problem.
Lost foam casting technology has great potential for development. By continuously studying and solving various defects in the casting process, we can further improve the quality of castings, reduce production costs, and promote the wider application of this technology in the manufacturing industry. Future research can focus on more in – depth exploration of defect formation mechanisms, the development of new coating materials and process optimization methods to continuously enhance the competitiveness of lost foam casting technology.
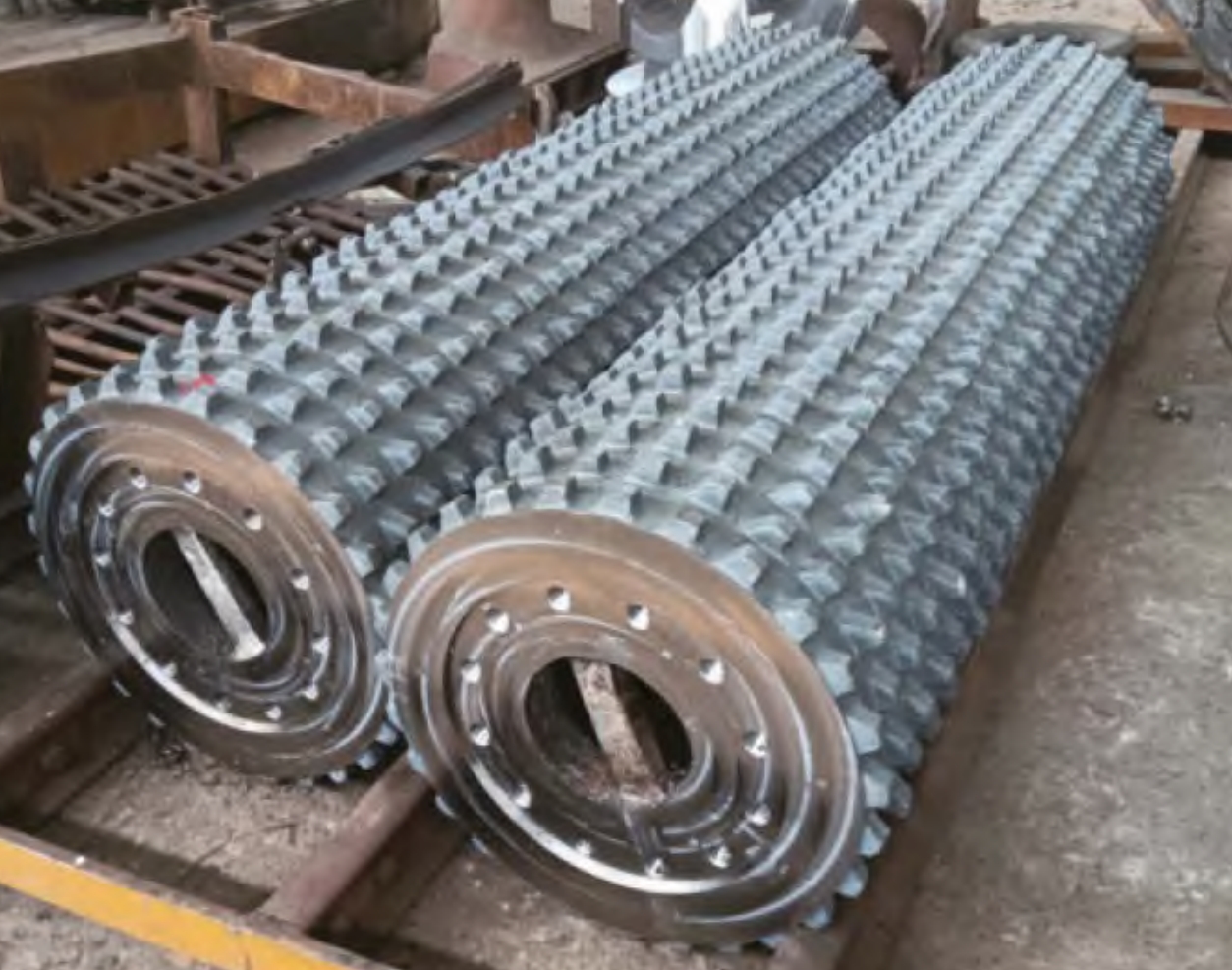