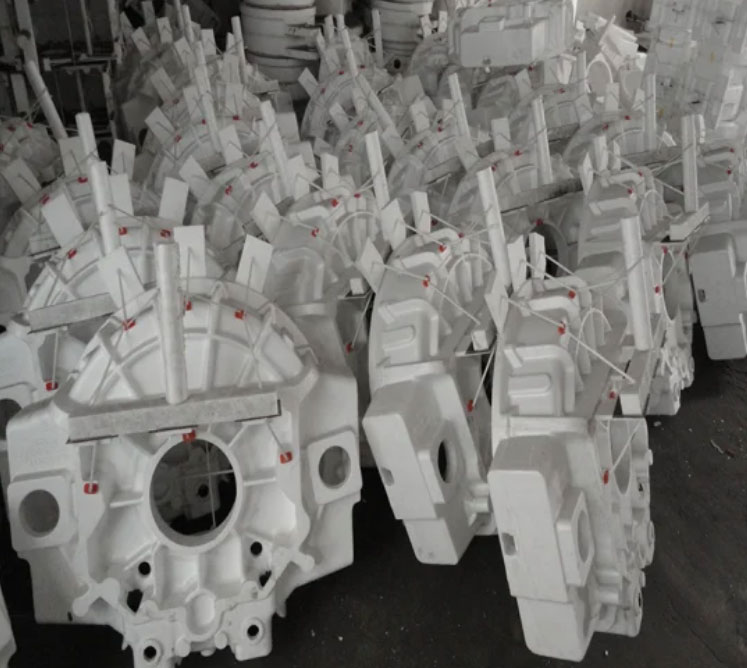
Lost foam casting (LFC) offers several advantages that contribute to enhanced casting quality and surface finish. These benefits make it an attractive casting method for applications where precision, dimensional accuracy, and surface aesthetics are crucial. Here’s how LFC achieves these improvements:
1. Precision Foam Patterns:
Lost foam casting utilizes precision foam patterns that are made using advanced molding techniques. These foam patterns accurately replicate the desired shape of the final casting. The use of high-quality foam patterns ensures that the castings are produced with tight dimensional tolerances and consistent part geometry.
2. Reduced Mold Material Contact:
In LFC, the foam pattern is surrounded by unbonded sand inside the mold, which eliminates direct contact between the molten metal and the mold material. This reduced mold contact minimizes the chances of mold-related defects, such as sand inclusions and surface imperfections.
3. Smooth Refractory Coating:
Before casting, the foam pattern is coated with a refractory material to create a ceramic shell. This shell provides a smooth and even surface finish to the casting. The refractory coating contributes to the final part’s improved surface quality and minimizes the need for extensive post-casting surface finishing.
4. Reduced Shrinkage Defects:
LFC reduces the risk of shrinkage defects, such as shrinkage porosity and cavities, due to its near-net-shape casting capability. The foam pattern compensates for solidification shrinkage, resulting in denser and more uniform castings.
5. Minimal Core Shift and Distortion:
Since the foam pattern is vaporized during the casting process, there is minimal core shift or distortion in the mold, ensuring the integrity of the casting’s shape and preventing warping issues.
6. Single-Piece Castings:
LFC can produce complex parts as single castings, eliminating the need for assembly and welds. Single-piece castings enhance the structural integrity of the final component and reduce the risk of defects associated with joining processes.
7. Reduced Fettling and Machining:
The high dimensional accuracy and precision of LFC parts reduce the need for extensive fettling and machining after casting. This saves time and resources, resulting in cost savings and improved overall production efficiency.
8. Improved Surface Finish:
The smooth refractory coating on the foam pattern transfers to the casting, resulting in a fine surface finish. The castings typically require minimal surface finishing, contributing to the overall aesthetics of the final product.
9. Better Heat Transfer Properties:
The uniformity and consistency of the LFC castings contribute to improved heat transfer properties. This is especially advantageous in applications where efficient heat dissipation or conduction is crucial.
Lost foam casting’s precision foam patterns, reduced mold contact, smooth refractory coating, and near-net-shape capabilities all contribute to enhancing casting quality and surface finish. The process minimizes defects, reduces post-casting machining, and allows for the production of complex and aesthetically pleasing parts with excellent dimensional accuracy and performance characteristics.