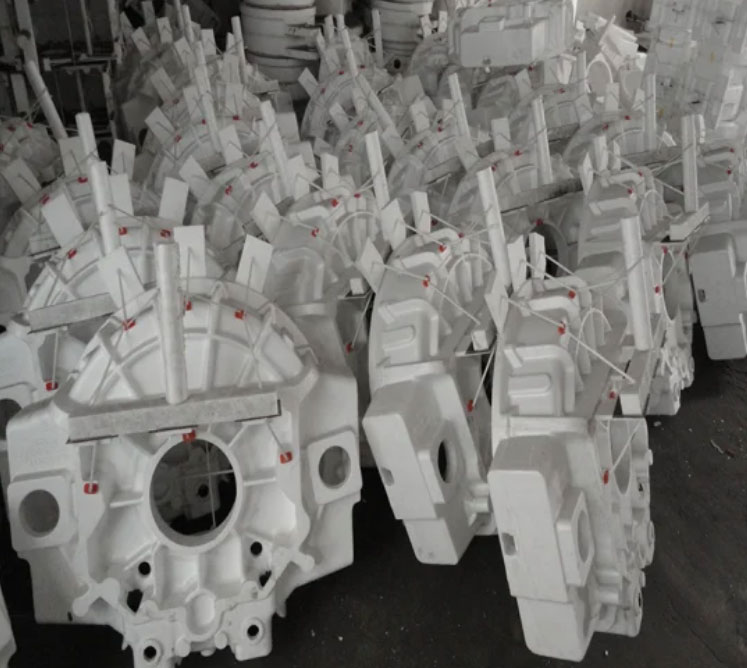
Streamlining production with lost foam casting (LFC) involves optimizing the entire process from concept to creation. By carefully managing each step, foundries can enhance efficiency, reduce lead times, and ensure high-quality castings. Here’s how to streamline production with lost foam casting:
1. Design and Prototyping:
- Use computer-aided design (CAD) software to create precise 3D models of the desired components.
- Work closely with designers and engineers to ensure that the designs are suitable for lost foam casting and can be cast without complexity issues.
- Rapidly produce foam prototypes for testing and validation, allowing for quick design iterations and improvements.
2. Foam Pattern Production:
- Utilize advanced molding techniques and high-quality foam materials to produce accurate and durable foam patterns.
- Implement efficient batch production methods to create multiple patterns simultaneously, reducing production time and costs.
3. Mold Making and Coating:
- Automate the mold making process to ensure consistent mold quality and reduce production time.
- Optimize the refractory coating process to achieve uniform and smooth coatings on the foam patterns, enhancing surface finish and casting quality.
4. Casting Process:
- Implement process controls and automation to ensure precise pouring and minimize the risk of defects during casting.
- Adopt real-time monitoring systems to track process parameters and identify any deviations or issues promptly.
5. Post-Casting Operations:
- Minimize the need for post-casting machining by achieving tight dimensional tolerances with precise foam patterns.
- Integrate any secondary operations, such as heat treatment or surface finishing, efficiently into the workflow to reduce lead times.
6. Quality Control:
- Establish a comprehensive quality control system to inspect castings at various stages of the process, from the foam patterns to the final products.
- Utilize non-destructive testing (NDT) methods to identify defects and ensure the integrity of the castings.
7. Workflow Optimization:
- Analyze the entire production workflow to identify bottlenecks and areas for improvement.
- Streamline material flow, tooling changes, and personnel assignments to maximize efficiency.
8. Training and Skill Development:
- Invest in training and skill development for operators and technicians to ensure that they are well-equipped to handle lost foam casting equipment and processes.
- Foster a culture of continuous improvement and encourage feedback from the workforce to identify areas for optimization.
9. Environmental Considerations:
- Incorporate eco-friendly practices into the production process, such as recycling foam patterns and using sustainable materials.
- Monitor and reduce energy consumption, waste generation, and emissions to support sustainability goals.
By adopting these strategies and continuously refining the lost foam casting process, foundries can streamline production, optimize resource utilization, and deliver high-quality castings efficiently. Proper planning, collaboration between design and manufacturing teams, and a commitment to process improvement are key to the successful implementation of lost foam casting in an optimized production environment.