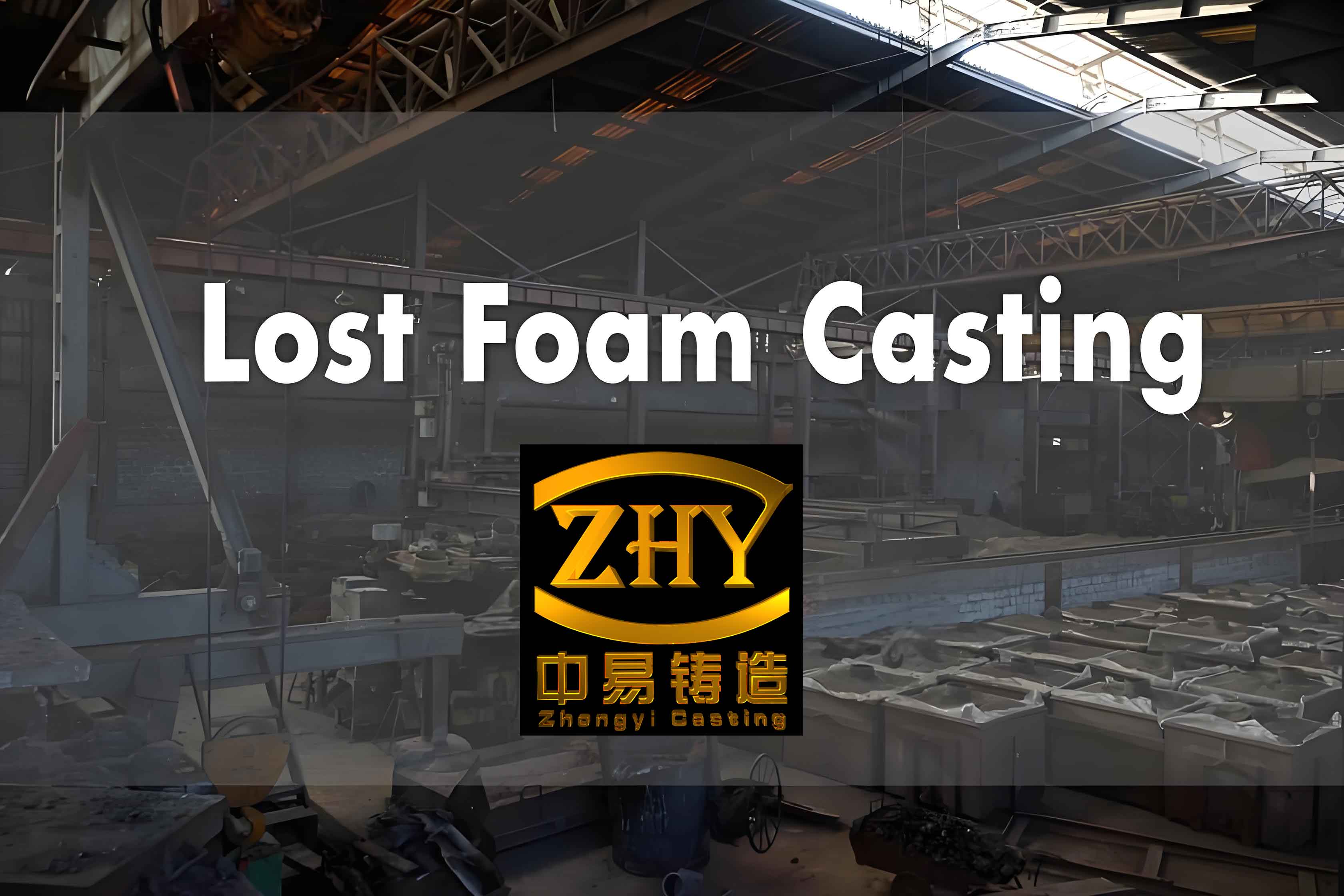
Lost foam casting is a versatile and efficient casting process widely used in the manufacturing industry. Its unique ability to produce complex and large-scale industrial components with high precision makes it an ideal choice for many applications. This article explores the use of lost foam casting for large-scale industrial components, discussing its advantages, process details, and specific applications.
Introduction to Lost Foam Casting
Lost foam casting involves creating a foam pattern of the desired component, which is then coated with a refractory material and placed in a sand mold. When molten metal is poured into the mold, the foam pattern vaporizes, leaving a metal casting that takes the shape of the original foam pattern. This process is particularly advantageous for producing large-scale industrial components due to its flexibility, precision, and cost-effectiveness.
Advantages of Lost Foam Casting for Large-Scale Components
Complex Geometry and Precision
Lost foam casting allows for the creation of components with complex geometries and intricate details. The foam patterns can be easily shaped to include internal cavities, undercuts, and fine features that would be challenging to achieve with other casting methods. This capability is especially beneficial for large-scale industrial components that require precise dimensions and intricate designs.
Cost-Effectiveness
Lost foam casting is a cost-effective method for producing large-scale components. The foam patterns are relatively inexpensive to produce, and the simplicity of the mold-making process reduces labor costs. Additionally, the ability to produce near-net-shape castings minimizes the need for extensive machining, further lowering production costs.
Versatility in Material Selection
Lost foam casting is compatible with a wide range of metals, including aluminum, cast iron, and steel. This versatility allows manufacturers to select the most appropriate material for the specific application, ensuring optimal performance and durability of the final components.
Reduced Machining and Finishing
The precision of lost foam casting results in castings that require minimal machining and finishing. This reduction in post-casting processes not only saves time and labor but also enhances the overall efficiency of the production process.
Key Steps in Lost Foam Casting for Large-Scale Components
- Pattern Creation: A foam model of the desired component is created using polystyrene or a similar material.
- Pattern Assembly: For larger components, multiple foam sections may be joined together to form a single pattern.
- Coating: The foam pattern is coated with a refractory material to create a durable shell.
- Molding: The coated pattern is placed in a sand mold, which is then compacted to provide support during metal pouring.
- Metal Pouring: Molten metal is poured into the mold, causing the foam pattern to vaporize and the metal to fill the cavity.
- Cooling and Removal: The metal is allowed to cool and solidify before the sand mold is removed to reveal the final casting.
- Finishing: Any remaining refractory material is removed, and lost foam casting is cleaned and inspected for quality.
Applications of Lost Foam Casting in Large-Scale Industrial Components
Automotive Industry
Lost foam casting is extensively used in the automotive industry for producing large-scale components such as engine blocks, cylinder heads, and transmission cases. The ability to create complex geometries and lightweight structures makes it ideal for manufacturing high-performance automotive parts.
Heavy Machinery and Equipment
In the heavy machinery and equipment sector, lost foam casting is employed to produce large components like pump housings, valve bodies, and gearboxes. The precision and durability of lost foam cast components ensure reliable performance in demanding industrial environments.
Construction and Mining Equipment
Lost foam casting is also utilized in the construction and mining industries for manufacturing components such as excavator arms, bulldozer blades, and mining equipment frames. The process’s capability to produce large, durable parts with intricate designs is crucial for these applications.
Comparative Analysis of Lost Foam Casting and Other Casting Methods
Aspect | Lost Foam Casting | Sand Casting | Die Casting |
---|---|---|---|
Pattern Material | Foam | Sand | Metal |
Mold Material | Sand | Sand | Steel |
Complexity of Geometry | High | Moderate | Low |
Production Volume | Medium to High | Low to High | High |
Surface Finish | Good | Moderate | Excellent |
Initial Tooling Cost | Low | Moderate | High |
Typical Applications | Automotive components, heavy machinery parts | General engineering, prototyping | High-volume production, small components |
Tables for Process Parameters
Table 1: Typical Process Parameters for Lost Foam Casting
Parameter | Value Range |
---|---|
Foam Density | 20-30 kg/m³ |
Coating Thickness | 1-3 mm |
Sand Compaction Pressure | 0.3-0.5 MPa |
Pouring Temperature | 700-800°C (for aluminum) |
Cooling Time | Dependent on component size |
Table 2: Comparison of Different Casting Methods
Aspect | Lost Foam Casting | Sand Casting | Die Casting |
---|---|---|---|
Complexity of Setup | Moderate | Low | High |
Pattern Reusability | Single-use | Single-use | Reusable |
Production Speed | Moderate | Slow | Fast |
Surface Roughness (Ra) | 3.2-6.3 µm | 6.3-12.5 µm | 1.6-3.2 µm |
Conclusion
Lost foam casting is an efficient and cost-effective method for producing large-scale industrial components. Its ability to create complex geometries, reduce machining and finishing requirements, and provide versatility in material selection makes it an ideal choice for various industrial applications. From the automotive industry to heavy machinery and construction equipment, lost foam casting offers numerous advantages that enhance the overall efficiency and performance of large-scale components. By understanding the key steps and benefits of lost foam casting, manufacturers can optimize their production processes and achieve high-quality, durable castings for their industrial needs.