Lost foam casting is particularly well-suited to the aerospace industry due to its ability to produce complex, high-integrity, and precision components essential for aerospace applications. This method’s unique advantages make it an attractive choice for manufacturing parts used in aircraft, spacecraft, and associated systems. Here’s how lost foam casting is applied in aerospace and why it stands out:
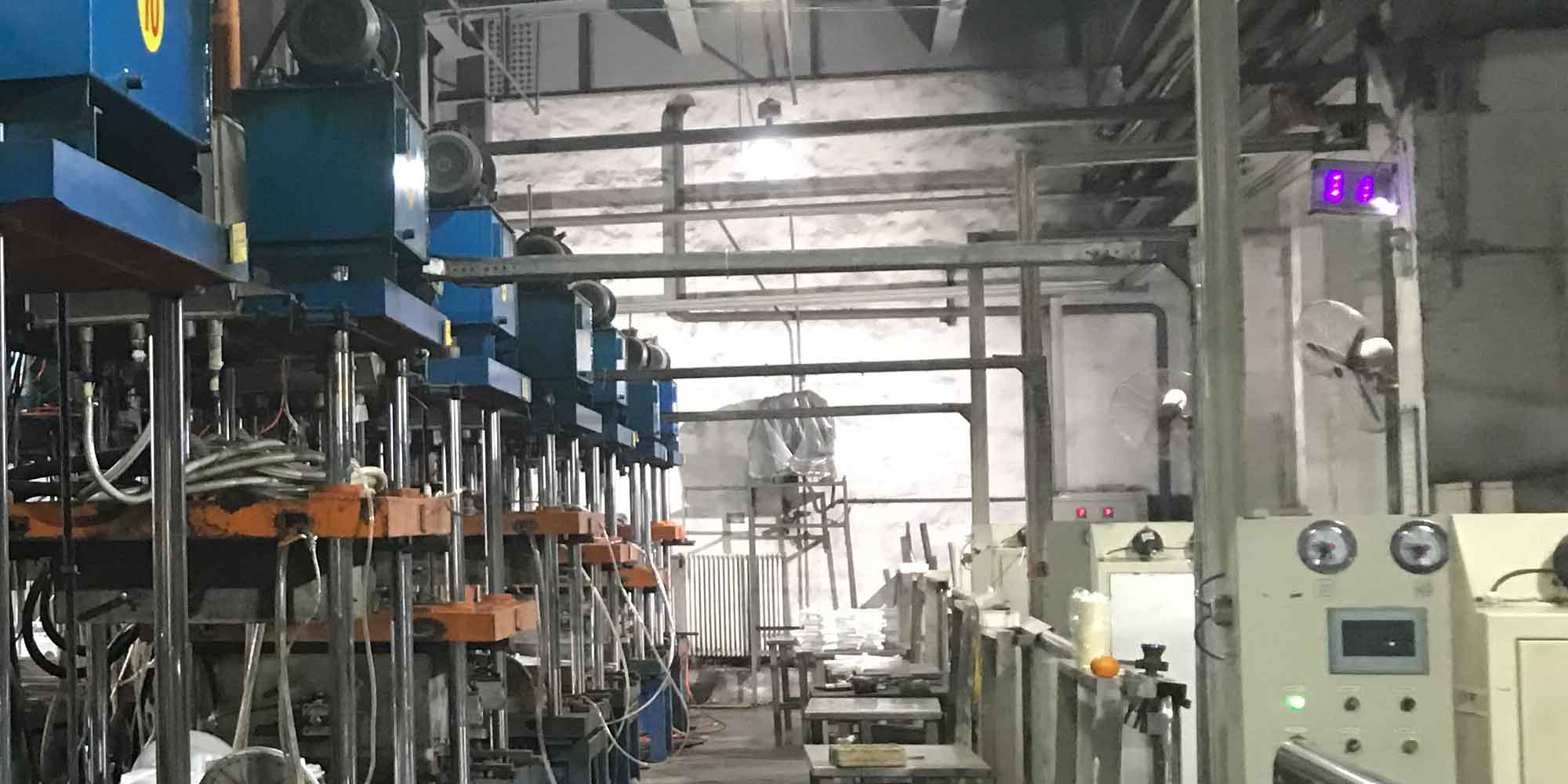
1. Complexity and Precision
- Intricate Designs: Lost foam casting allows for the creation of highly complex geometries that are often required in aerospace components. These include intricate passageways, heat exchangers, and structural parts with complex internal features that would be difficult or impossible to achieve with other casting methods.
- High Dimensional Accuracy: The process delivers excellent dimensional accuracy and surface finish, reducing the need for subsequent machining and finishing processes. This is critical in aerospace where the precision of each component impacts overall system performance.
2. Material Diversity
- Advanced Alloys: Aerospace applications often require materials that have superior mechanical properties, such as high strength-to-weight ratios and excellent corrosion resistance. Lost foam casting is compatible with a wide range of alloys, including aluminum, magnesium, titanium, and nickel-based superalloys, making it ideal for aerospace use.
3. Weight Reduction
- Lightweight Parts: The ability to produce lightweight components is crucial in aerospace for fuel efficiency and payload maximization. Lost foam casting allows for the production of parts that are both lightweight and structurally sound, a vital attribute for aircraft and spacecraft components.
4. Reduced Assembly
- Integration of Features: Parts can be cast as single pieces that would otherwise have to be assembled from several different components. This not only reduces the weight and increases the strength of the parts but also cuts down on assembly time and costs.
5. Quality and Reliability
- Non-Destructive Testing Compatibility: Aerospace components require rigorous testing to ensure reliability and safety. The high-quality surfaces and consistent properties of lost foam castings make them ideal candidates for advanced non-destructive testing methods such as X-ray and ultrasonic inspections.
- Consistent Reproducibility: Once a foam pattern is designed and the casting parameters are set, lost foam casting allows for the high-volume production of parts with very little variation, essential for maintaining the stringent quality standards of the aerospace industry.
6. Cost-Effectiveness
- Tooling and Equipment Costs: Although the initial setup and tooling costs can be higher than some other casting methods, the reduction in machining and finishing requirements, coupled with the minimal waste production, makes lost foam casting cost-effective for many aerospace applications.
- Economies of Scale: For large production runs, the economies of scale achievable with lost foam casting can significantly drive down the cost per unit, an important consideration in large aerospace projects.
7. Customization and Prototyping
- Rapid Prototyping: The process is compatible with rapid prototyping technologies. Foam patterns can be quickly produced using CNC machining or 3D printing, allowing for fast design iterations and development cycles, which are crucial during the prototyping phase of aerospace components.
8. Sustainability
- Reduced Waste and Environmental Impact: Lost foam casting produces less waste compared to traditional casting methods, aligning with the increasing environmental regulations and sustainability goals in the aerospace industry.
Lost foam casting’s unique capabilities enable it to meet the aerospace industry’s demanding requirements for precision, performance, and reliability. As technology advances and the need for more sophisticated components grows, lost foam casting will likely continue to play a critical role in aerospace manufacturing.