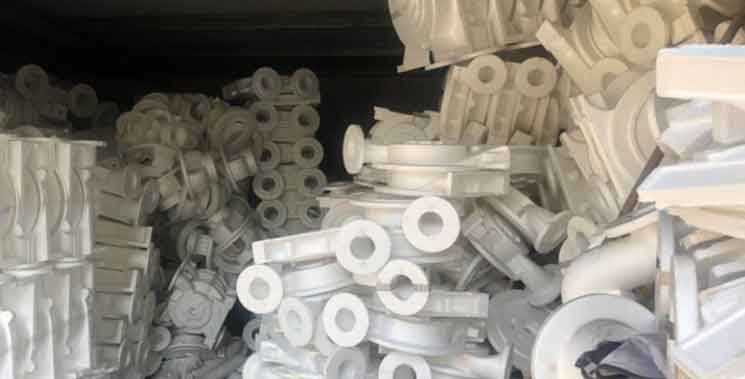
Lost foam casting has made significant contributions to innovation and efficiency in both automotive and industrial applications. This casting method offers numerous advantages that align with the requirements of these industries, driving advancements and improving overall performance. Here’s how lost foam casting is driving innovation and efficiency in automotive and industrial applications:
1. Lightweighting in Automotive:
Automotive manufacturers strive to reduce vehicle weight to improve fuel efficiency and reduce emissions. Lost foam casting enables the production of lightweight components with complex geometries, such as engine blocks, cylinder heads, intake manifolds, and suspension components. By replacing heavier parts with lighter castings, automotive manufacturers can achieve significant weight savings without compromising strength or performance.
2. Design Freedom and Integration:
Lost foam casting allows for the integration of multiple features into a single casting, reducing the need for separate components and assembly operations. In the automotive industry, this facilitates the production of complex engine components and structural parts with integrated cooling passages, reinforcement ribs, and mounting points. The ability to consolidate parts and optimize designs enhances overall efficiency and reduces assembly time and costs.
3. Engine Performance Optimization:
Lost foam casting enables the production of intricate engine components that contribute to improved performance. Cylinder heads, intake manifolds, and exhaust manifolds can be designed with precise control over fluid flow, optimizing combustion efficiency and power output. The ability to create complex cooling passages and fine-tune designs helps manage engine temperature, contributing to enhanced performance and durability.
4. Versatility in Industrial Applications:
Lost foam casting is not limited to the automotive industry and finds applications in various industrial sectors. It is used to produce complex components for pumps, compressors, valves, and other industrial machinery. The ability to create intricate designs with internal features and optimized flow passages allows for improved equipment efficiency, reduced energy consumption, and enhanced reliability.
5. Cost-Effective Production:
Lost foam casting offers cost-effective production solutions for automotive and industrial applications. The elimination of cores and the ability to produce near-net shape castings reduce material waste, machining requirements, and assembly operations. This results in cost savings in terms of material usage, labor, and overall production time. Additionally, the ability to rapidly produce prototypes and transition to mass production further enhances cost-effectiveness.
6. Improved Component Performance:
Lost foam casting allows for the production of high-quality, dimensionally accurate components with excellent surface finishes. This contributes to improved component performance, reduced friction, enhanced wear resistance, and optimized functionality. The ability to achieve complex geometries without compromising integrity ensures reliable and efficient operation in demanding automotive and industrial environments.
7. Environmental Sustainability:
Lost foam casting aligns with the growing focus on environmental sustainability in automotive and industrial sectors. The lightweight nature of castings reduces vehicle emissions in the automotive industry, while optimized designs and improved energy efficiency contribute to reduced environmental impact in industrial applications. Furthermore, the reduced material waste and energy consumption associated with lost foam casting make it a greener alternative to traditional manufacturing methods.
Lost foam casting’s lightweighting capabilities, design freedom, integration of features, cost-effectiveness, and environmental sustainability align with the goals of the automotive and industrial sectors. By driving innovation and efficiency, lost foam casting enables the production of high-performance components that meet the demands of these industries while supporting sustainability initiatives.