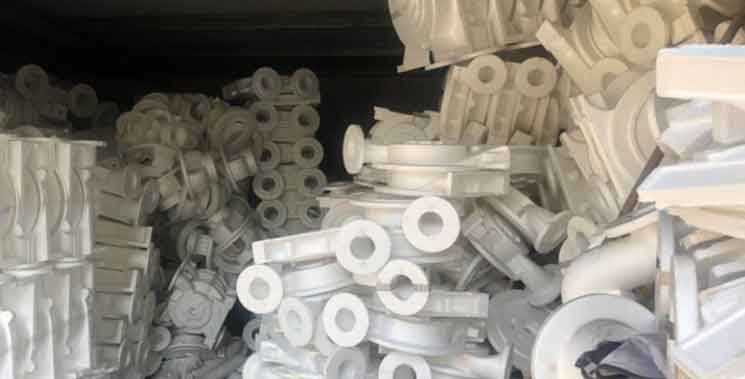
Lost foam casting plays a significant role in automotive manufacturing, contributing to increased efficiency, enhanced performance, and cost-effectiveness in producing various automotive components. Here are some ways in which lost foam casting benefits the automotive industry:
- Lightweight Components: Lost foam casting allows the production of lightweight and complex components with thin walls and intricate geometries. This is especially valuable in the automotive sector, where lightweight materials are essential for improving fuel efficiency and overall vehicle performance.
- Integration of Multiple Components: Lost foam casting enables the integration of multiple components into a single casting. For example, engine blocks can be cast with integrated coolant passages, oil galleries, and other internal features. This reduces assembly time and the need for additional components, enhancing overall part strength and reliability.
- High Precision: Lost foam casting produces near-net-shape castings with tight tolerances, minimizing the need for extensive machining and finishing. This precision is crucial for automotive parts that require accurate fits and optimal performance.
- Cost-Effectiveness: The near-net-shape capability of lost foam casting reduces material waste and machining costs, leading to cost-effective production processes. It also lowers the overall weight of the vehicle, contributing to fuel efficiency and lower emissions.
- Complex Cooling Passages: Lost foam casting allows for the creation of intricate cooling passages within the engine components, such as cylinder heads and engine blocks. These optimized cooling passages enhance engine performance and thermal efficiency.
- Noise and Vibration Damping: Lost foam casting can be used to manufacture components with integrated features that help dampen noise and vibration in the vehicle. For example, engine mounts and suspension components can be cast with built-in isolation features.
- Heat Resistance and Durability: Lost foam casting can produce parts with exceptional heat resistance and durability, making it suitable for high-temperature applications in engines and exhaust systems.
- Flexibility in Material Selection: Lost foam casting can work with a wide range of materials, including aluminum, iron, and various alloys, allowing automotive manufacturers to choose materials that best suit the specific application requirements.
- Simplified Tooling: Lost foam casting requires less complex tooling compared to traditional casting methods, making it more cost-effective for low to medium volume production runs.
Automotive components that can be manufactured using lost foam casting include engine blocks, cylinder heads, intake manifolds, transmission cases, suspension components, and other critical parts. The ability to create lightweight, precise, and complex components with improved performance characteristics makes lost foam casting a valuable technology in the automotive industry. It helps automakers meet the demands of fuel efficiency, emissions reduction, and overall vehicle performance, contributing to advancements in automotive manufacturing and design.