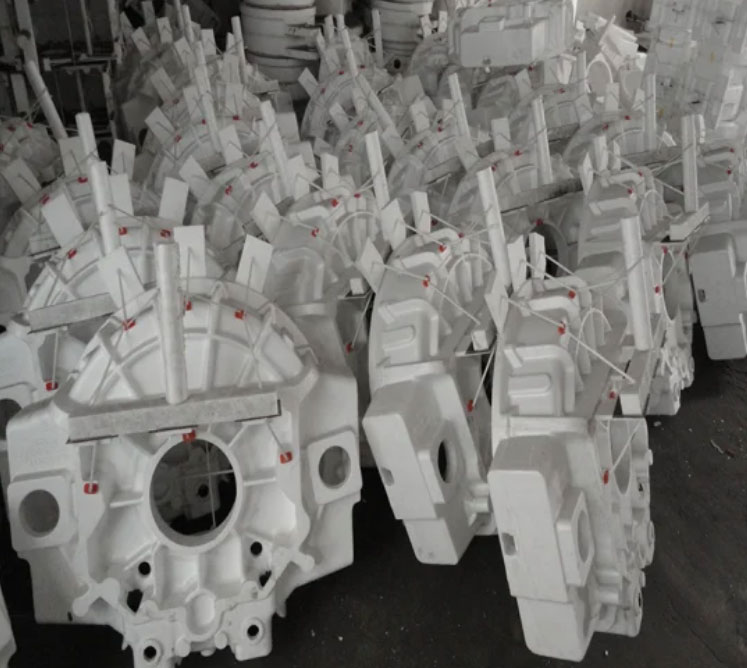
Lost foam casting (LFC) has indeed revolutionized metal casting techniques in foundries by offering numerous advantages over traditional casting methods. Foundries that adopt lost foam casting benefit from the following aspects:
1. Design Flexibility and Complexity:
Lost foam casting allows foundries to create complex and intricate designs that may not be feasible with other casting processes. This flexibility empowers designers to push the boundaries of conventional designs and explore innovative solutions for various industries.
2. Reduced Tooling Costs:
Unlike traditional casting methods that require expensive and time-consuming tooling, lost foam casting utilizes foam patterns that are relatively cost-effective and easy to produce. This reduction in tooling costs results in cost savings and quicker lead times for casting production.
3. Single-Piece Castings:
Lost foam casting can produce intricate components as a single piece, eliminating the need for assembly and welding of multiple parts. Single-piece castings enhance component integrity and reduce the risk of defects associated with welding.
4. Improved Dimensional Accuracy:
The precision and consistency of foam patterns in lost foam casting result in better dimensional accuracy and tighter tolerances in the final cast parts. This reduces the need for extensive post-casting machining and refining.
5. Enhanced Surface Finish:
The refractory coating on foam patterns creates smooth and high-quality surface finishes on the castings. This minimizes the need for additional surface finishing operations, such as grinding and polishing.
6. Lightweighting Opportunities:
Lost foam casting allows for the creation of hollow components, enabling foundries to produce lightweight parts with improved strength-to-weight ratios. This is particularly advantageous in industries aiming to reduce overall weight and enhance fuel efficiency.
7. Eco-Friendly and Reduced Waste:
The lost foam process generates minimal waste, as the foam patterns are easily recyclable. Additionally, the evaporated foam does not produce harmful emissions, making lost foam casting a relatively eco-friendly casting method.
8. Rapid Prototyping and Customization:
The ability to quickly create and modify foam patterns makes lost foam casting ideal for rapid prototyping and custom manufacturing. Foundries can rapidly develop and test new designs, leading to faster product development cycles.
9. Simplified Assembly and Fewer Defects:
With complex parts produced as single castings, lost foam casting reduces the need for assembly and minimizes the risk of defects associated with assembly processes.
10. Material Versatility:
Lost foam casting can be used with various metals and alloys, such as aluminum, cast iron, and steel, offering versatility to foundries for diverse industrial applications.
By leveraging the advantages of lost foam casting, foundries can optimize their casting processes, reduce production costs, and meet the increasing demand for complex and innovative metal components. The process has proven to be a game-changer in the foundry industry, opening up new possibilities for designers and manufacturers to produce high-quality, lightweight, and intricately designed components with efficiency and precision.