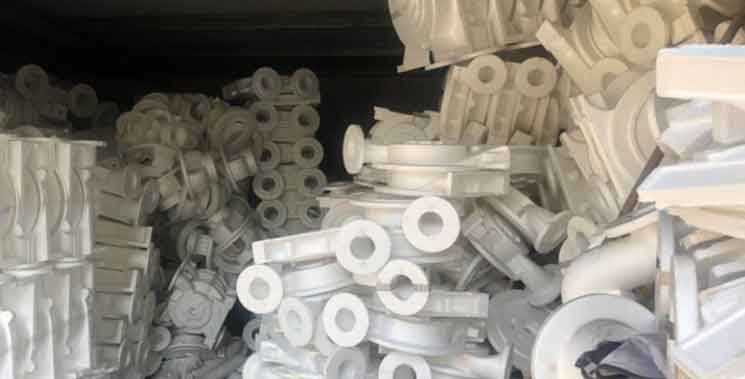
Lost foam casting is a process used for manufacturing complex metal parts by creating foam patterns that are coated with a refractory material, placed in a mold, and then replaced with molten metal. This casting method offers several advantages, including the ability to produce intricate designs and near-net-shape parts. However, like any manufacturing process, it also has its challenges. Here are some ways to overcome these challenges and achieve superior metal castings in lost foam casting:
1.Foam Pattern Quality:
The quality of the foam pattern used in lost foam casting plays a crucial role in the final product. To overcome this challenge, it is essential to use high-quality foam patterns that are dimensionally accurate and have a smooth surface. Quality control measures such as inspecting and validating each foam pattern before use can help ensure consistency and minimize defects.
2.Foam Pattern Coating:
Coating the foam pattern with a refractory material is crucial to achieve a high-quality casting. The coating should be uniform, free from cracks, and have good adhesion to the foam surface. Proper coating techniques, including using suitable refractory materials, controlling the coating thickness, and ensuring even distribution, can help overcome this challenge.
3.Mold Design and Construction:
Designing and constructing the mold appropriately is essential to avoid casting defects. Careful consideration should be given to factors such as gating, riser design, and venting to ensure proper filling of the mold, minimize the formation of defects like shrinkage, and ensure good ventilation to allow the escape of gases. Computer-aided design (CAD) software and simulation tools can be helpful in optimizing the mold design and identifying potential issues before casting.
4.Metal Pouring and Solidification:
Achieving optimal pouring and solidification conditions is crucial for obtaining superior metal castings. Proper control of metal pouring temperature, pouring rate, and filling technique can help prevent issues like misruns and cold shuts. Additionally, ensuring adequate riser placement and size can help promote proper solidification and minimize shrinkage defects.
5.Sand Compaction and Handling:
The quality and uniformity of the sand used in lost foam casting significantly impact the casting results. Proper sand compaction techniques, including using appropriate compaction pressure and methods, can help ensure uniform density and reduce the risk of defects like gas porosity. Proper sand handling practices, such as maintaining sand quality and preventing contamination, also contribute to achieving superior castings.
6.Process Monitoring and Quality Control:
Regular monitoring of process parameters, such as foam density, coating thickness, sand quality, and metal temperature, is crucial to maintain consistency and detect any deviations. Implementing robust quality control measures, including inspection and testing of castings, can help identify defects early on and take corrective actions promptly.
7.Continuous Process Improvement:
Lost foam casting is an iterative process, and continuous improvement is essential to overcome challenges and achieve superior castings. Collecting and analyzing data, incorporating feedback from quality inspections, and implementing corrective actions based on lessons learned can help refine the process and optimize the results.
By addressing these challenges and implementing best practices, manufacturers can enhance the quality, accuracy, and consistency of metal castings produced through the lost foam casting process, ultimately achieving superior results.