Lost foam casting is indeed redefining the future of foundries by offering numerous advantages and driving advancements in the field. Here’s a closer look at how lost foam casting is shaping the future of foundries:
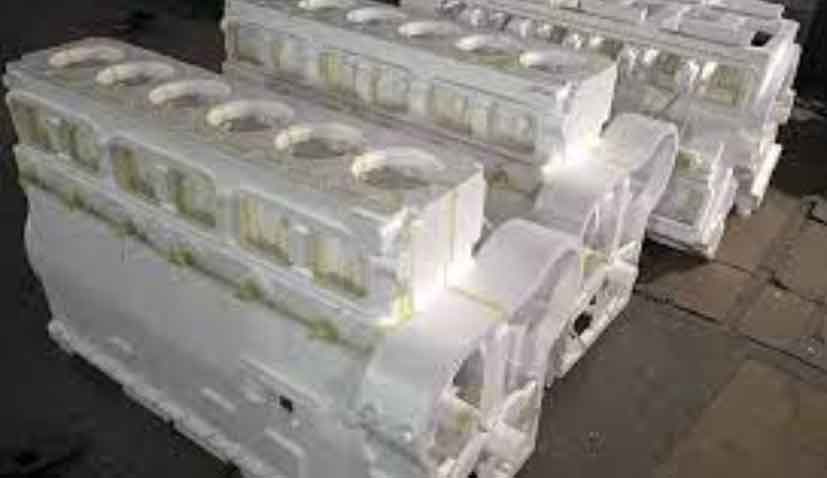
- Enhanced Efficiency:
- Lost foam casting improves overall foundry efficiency through reduced material waste, streamlined processes, and optimized production cycles.
- The near-net shape capability minimizes the need for extensive post-casting machining, reducing both time and cost.
- Faster production cycles and reduced lead times contribute to increased productivity and improved overall efficiency.
- Complex Part Production:
- Lost foam casting enables foundries to produce highly complex and intricate parts with ease.
- The foam patterns used in the process can be easily shaped and assembled to achieve intricate geometries, thin walls, and internal features.
- This capability opens up new possibilities for foundries to meet the increasing demand for intricate and customized components.
- Design Freedom and Innovation:
- Lost foam casting provides foundries with unparalleled design freedom, fostering innovation and encouraging the exploration of new possibilities.
- The flexibility of foam patterns allows designers to create intricate and optimized part designs without the constraints of traditional tooling limitations.
- Foundries can collaborate closely with designers and engineers to push the boundaries of what is achievable, leading to innovative and improved products.
- Cost-Effectiveness:
- Lost foam casting offers cost advantages for foundries, particularly in terms of tooling and material savings.
- The elimination of expensive permanent molds or complex sand molds reduces tooling costs.
- Near-net shape castings minimize material waste, leading to cost savings in material consumption and machining operations.
- Sustainability and Environmental Considerations:
- Lost foam casting aligns with sustainability goals due to reduced material waste and energy consumption.
- The foam patterns used in the process are easily recyclable or disposable, contributing to reduced environmental impact.
- The absence of sand molds and associated binders reduces the generation of harmful emissions or byproducts.
- Versatility and Material Options:
- Lost foam casting is compatible with a wide range of metals and alloys, offering versatility in material selection.
- Foundries can cast various metals, including aluminum, iron, steel, and non-ferrous alloys, depending on the specific application requirements.
- This versatility allows foundries to cater to diverse industries and expand their market reach.
- Automation and Advanced Manufacturing Integration:
- Lost foam casting can be integrated with automation and advanced manufacturing technologies, further enhancing foundry operations.
- Robotic systems can be employed for pattern production, mold coating, pouring, and shakeout, reducing manual labor and improving process consistency.
- Foundries can leverage digital technologies, such as simulation software and data analytics, to optimize the casting process and enhance overall efficiency.
Lost foam casting is redefining the future of foundries by offering enhanced efficiency, enabling complex part production, fostering design freedom and innovation, providing cost-effectiveness, promoting sustainability, offering material versatility, and integrating with advanced manufacturing technologies. With its numerous advantages, lost foam casting is driving the evolution of foundries and paving the way for efficient, sustainable, and innovative casting processes.